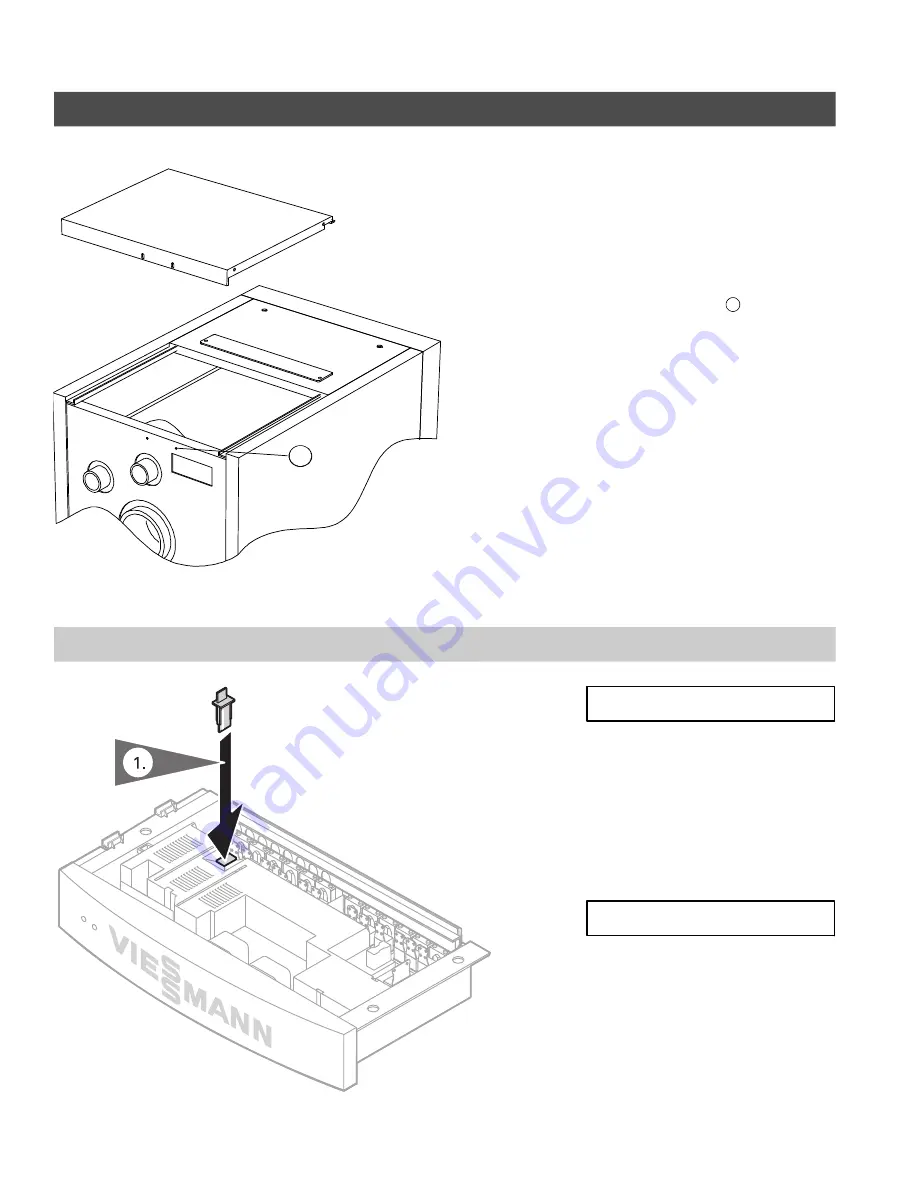
Connections
56
Burner Set-up (Riello)
(continued)
1.
To avoid problems with removing the
top panel, we recommend moving the
top panel screw approximately 3” to
the left or right. To do this, pre-drill
the panels with an
1
/
8
” drill bit.
To reinstall the top panel, drill a new
1
/
8
” pilot hole through the top back
panel and into the back panel.
Reinstall the screw
P
into this new
mounting hole.
Boiler coding card
Only the boiler coding card supplied
with the standard equipment of the
boiler may be used. The coding card is
enclosed in the accessory pack of the
boiler.
1.
Push boiler coding card through
recess in the cover and insert it into
plug-in location ”X7”.
If the boiler coding card is not installed
the following fault code will be
displayed on the boiler control:
“
b
b
b
b7
7
7
7
“
.
P
Fig. 55
5
6
7
1
0
4
4
v
1
.0
Fig. 56
IMPORTANT
IMPORTANT