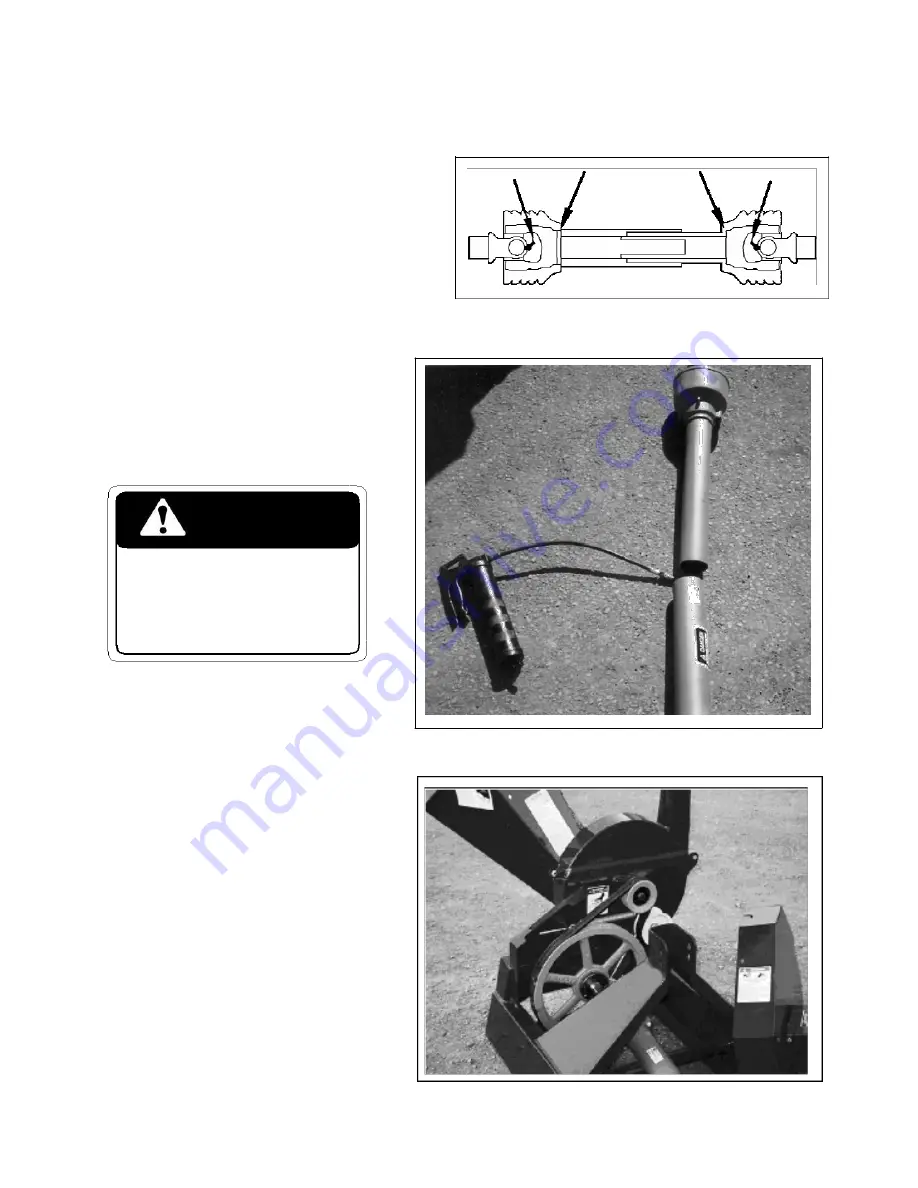
6.1 .3 SERVICING INTERVALS
The period recommended is based on normal
operating conditions. Severe or unusual cond-
tions may require more frequent lubrication or oil
changes.
Hours or Daily
1. Grease PTO driveline.
40 Hours or Weekly
1. Grease the telescoping section of
the PTO shaft.
WARNING
Machine is shown with guard re-
moved or rotor cover opened for
illustrative purposes only. Do not
operate machine with guard
removed or cover opened.
Fig. 38
PTO driveline
Fig. 39
TELESCOPING SECTION
2. Check input drive belt tensioner.
Fig. 40
BELT TENSION
Содержание BX32
Страница 1: ...Wood Chipper Operator s Manual BX42S BX72R Please read this manual prior to operation ...
Страница 2: ...IMPORTANT READ THESE INSTRUCTIONS BEFORE INSTALLING AND USING THIS IMPLEMENT ...
Страница 18: ...4 Cut the tie down straps Fig 2 TIE DOWNS 5 Lay out components next to machine BX32 BX62 Fig 3 LAY OUT ...
Страница 48: ...Annually 1 Clean machine BX32 BX42 BX62 Fig 45 MACHINE ...
Страница 54: ...BX42S Wood Chipper ...
Страница 57: ...BX72R ...
Страница 62: ...67 03 05 7809 UCP208 inserted bearing with housing UCP208 68 03 02 6182 M14 locking nut M14 ...