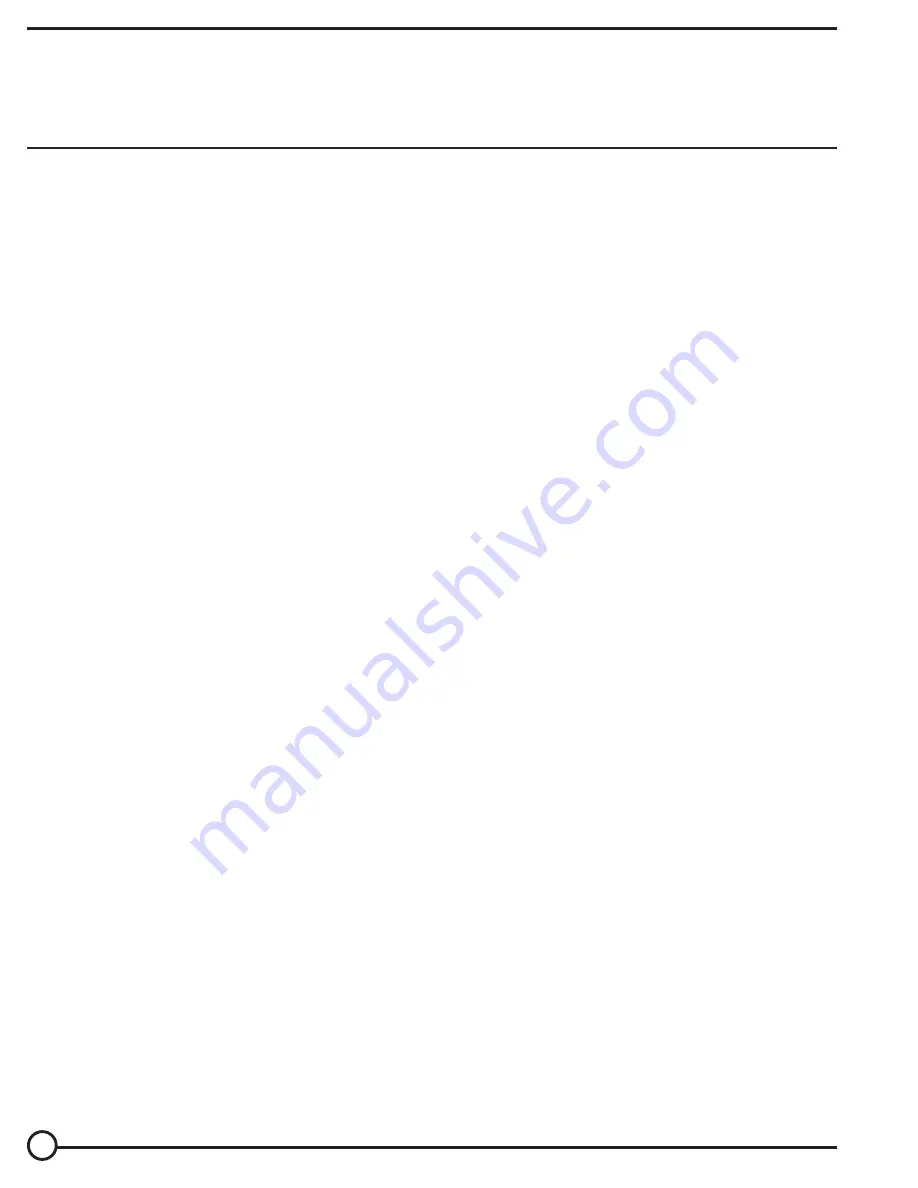
14
TROUBLESHOOTING GUIDE - HDC-305
Before performing any task, always lower the carrier fully to the floor and disconnect the power supply.
Consult the factory for problems at time of installation, or for any problems not addressed below.
*Check the DC notes page for troubleshooting other problems specific to battery-powered units.
Power unit doesn't run when "UP"
button is pressed.
Motor runs properly, carrier
doesn't move. Motor and pump
not noisy.
Motor or control enclosure hums,
chatters, or buzzes, or some
type of squeal can be heard;
the carrier does not move, or
the carrier moves only slowly.
Carrier raises, then drifts down.
Carrier lowers too quickly.
Carrier lowers too slowly.
Carrier won't lower.
Spongy or jerky carrier motion.
Transformer fuse is blown.
No supply voltage.
Upper-travel limit switch is
engaged or bad.
Bad connection in control circuit.
Bad control transformer.
Open motor relay coil.
Battery voltage low.
Motor rotation is wrong.
Pump has failed.
Fluid level is low.
See second item above, for when
carrier doesn't raise.
Excess voltage drop to motor,
due to power wire size too
small, wire run to long, or
incoming voltage too low.
Motor is "single-phasing".
Pressure relief opening a full
pressure.
Contamination holding open the
lowering valve or the check
valve.
See last paragraph, above.
See above.
Flow control spool is stuck.
Flow control spool is stuck.
Pinched hose.
Velocity fuse locking (carrier only
slowly creeps down).
Velocity fuse locking.
Control transformer fuse blown.
No supply-voltage.
Valve solenoid is bad.
Bad connection in control circuit.
Physical blockage of the
structure.
Solenoid valve or suction hose
screen plugged.
Excessive air in the hydraulic
cylinder.
Possible Cause(s)
Action
Problem
Test with meter; replace if bad.
Test with meter. Check fuses, break-
ers, and overloads to determine the
cause.
Inspect and test switch. Replace
if bad
Test all parts of circuit with meter.
Check for 24 VAC; replace if bad.
Test with meter; replace if bad.
Test with meter. Charge battery
if low (is motor relay LED on?)
Verify motor shaft rotates CCW.
Consult factory for replacement.
Ensure reservoir is filled.
Same as above.
Check power installation for
adequacy. Check incoming
voltage while motor is running.
Correct problem found.
Determine cause of loss of
voltage on one phase; correct.
Check for structural damage or
binding of the scissor legs, etc.
Check for carrier overload
condition.
Remove and inspect. Clean per
instructions in this manual.
Same as above.
Same as above.
See below.
Remove plug from FC port; push
on flow spool to ensure it is
fully pressed into the cavity.
Check pressure, supply, and
return hoses for kinks.
Same as for jerky carrier motion.
Same as for jerky carrier motion.
Test with meter; replace if bad.
Test with meter. Check for
cause of power loss.
Check with multimeter on diode-
check function. (Reading for
ohms will not provide an
accurate test of the coil.)
Test all parts of circuit with meter.
Inspect for foreign material or
objects that might block the leg
set or its rollers.
Remove and inspect. Clean per
instructions in this manual.
Bleed air per procedure described
in manual