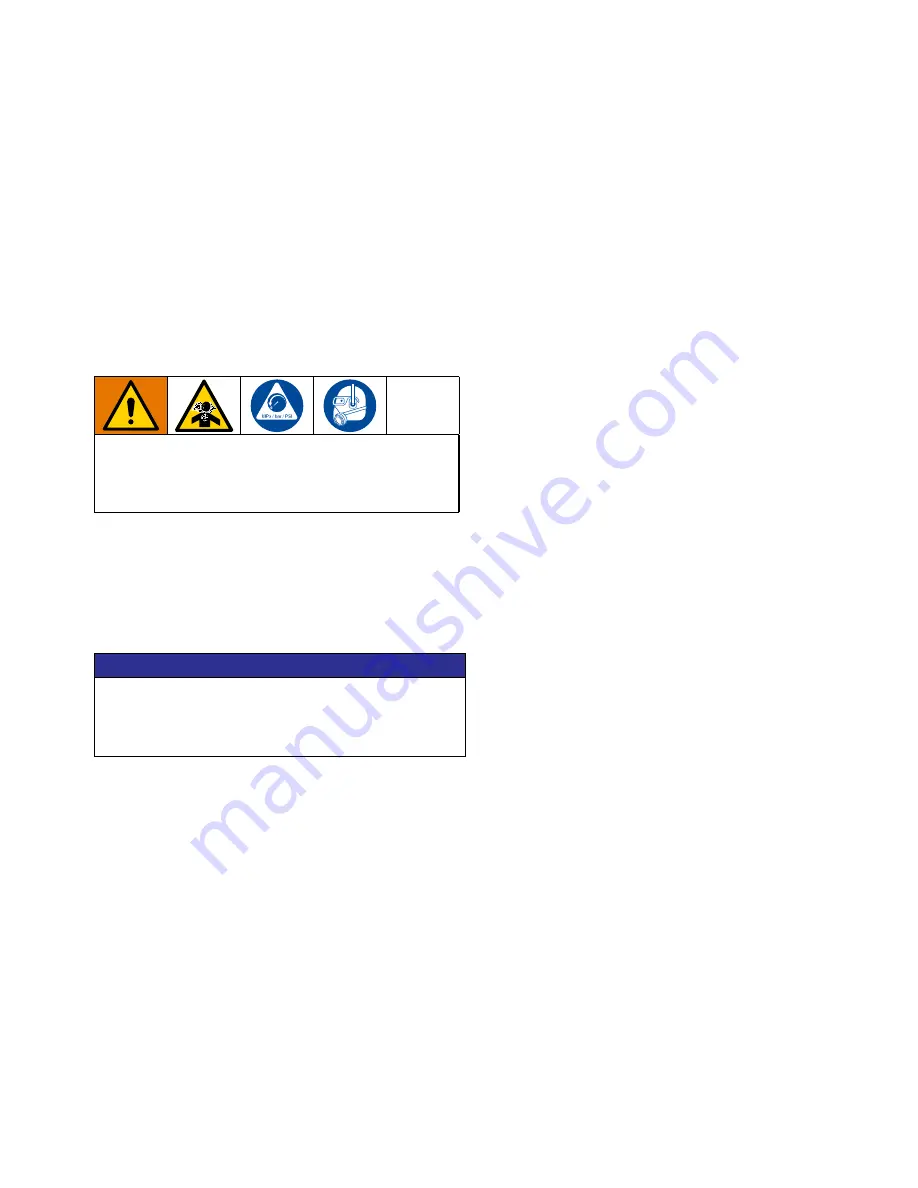
Installation
812.0061
9
Fluid Suction and Outlet Lines
For best sealing results, use a standard tri-clamp or DIN
style sanitary gasket of a flexible material such as
EPDM, Buna-N, fluoroelastomer, or silicone.
NOTE:
Compliance with 3A sanitary standards requires
DIN connections to use certain gaskets. See CCE
Coordination Bulletin Number 2011-3.
1. Install flexible, conductive fluid lines (G and H).
2. Install a fluid drain valve (K) close to the pump fluid
3. Install a fluid shutoff valve (J) in the fluid outlet line
(G) downstream from the fluid drain valve (K).
NOTE:
For best results, always install the pump as
close as possible to the material source. See the
Technical Data
for maximum suction lift (wet and dry).
Tips to Reduce Cavitation
Cavitation in a diaphragm pump is the formation and
collapse of bubbles in the pumped liquid. Frequent or
excessive cavitation can cause serious damage,
including pitting and early wear of fluid chambers, balls,
and seats. It may result in reduced efficiency of the
pump. Cavitation damage and reduced efficiency both
result in increased operating costs.
Cavitation depends on the vapor pressure of the
pumped liquid, the system suction pressure, and the
velocity pressure. It can be reduced by changing any of
these factors.
1. Reduce vapor pressure: Decrease the temperature
of the pumped liquid.
2. Increase suction pressure:
a. Lower the installed position of the pump relative
to the liquid level in the supply.
b. Reduce the friction length of the suction lines.
Remember that fittings add friction length to the
lines. Reduce the number of fittings to reduce
the friction length.
c. Increase the diameter of the suction lines.
d. Ensure the inlet fluid pressure does not exceed
25% of the outlet working pressure.
3. Reduce liquid velocity: Slow the cyclic rate of the
pump.
Pumped liquid viscosity is also very important but
normally is controlled by factors that are process
dependent and cannot be changed to reduce cavitation.
Viscous liquids are more difficult to pump and more
prone to cavitation.
Verder recommends taking all of the above factors into
account in system design. To maintain pump efficiency,
supply only enough air to the pump to achieve the
required flow.
Verder distributors can supply site-specific suggestions
to improve pump performance and reduce operating
costs.
A fluid drain valve (K) is required to relieve pressure
in the fluid outlet line if it is plugged. The drain valve
reduces the risk of serious injury, including splashing
in the eyes or on the skin, when relieving pressure.
NOTICE
The pump can be damaged if flexible fluid lines are
not used. If hard-plumbed fluid lines are used in the
system, use a short length of flexible, conductive fluid
line to connect to the pump.