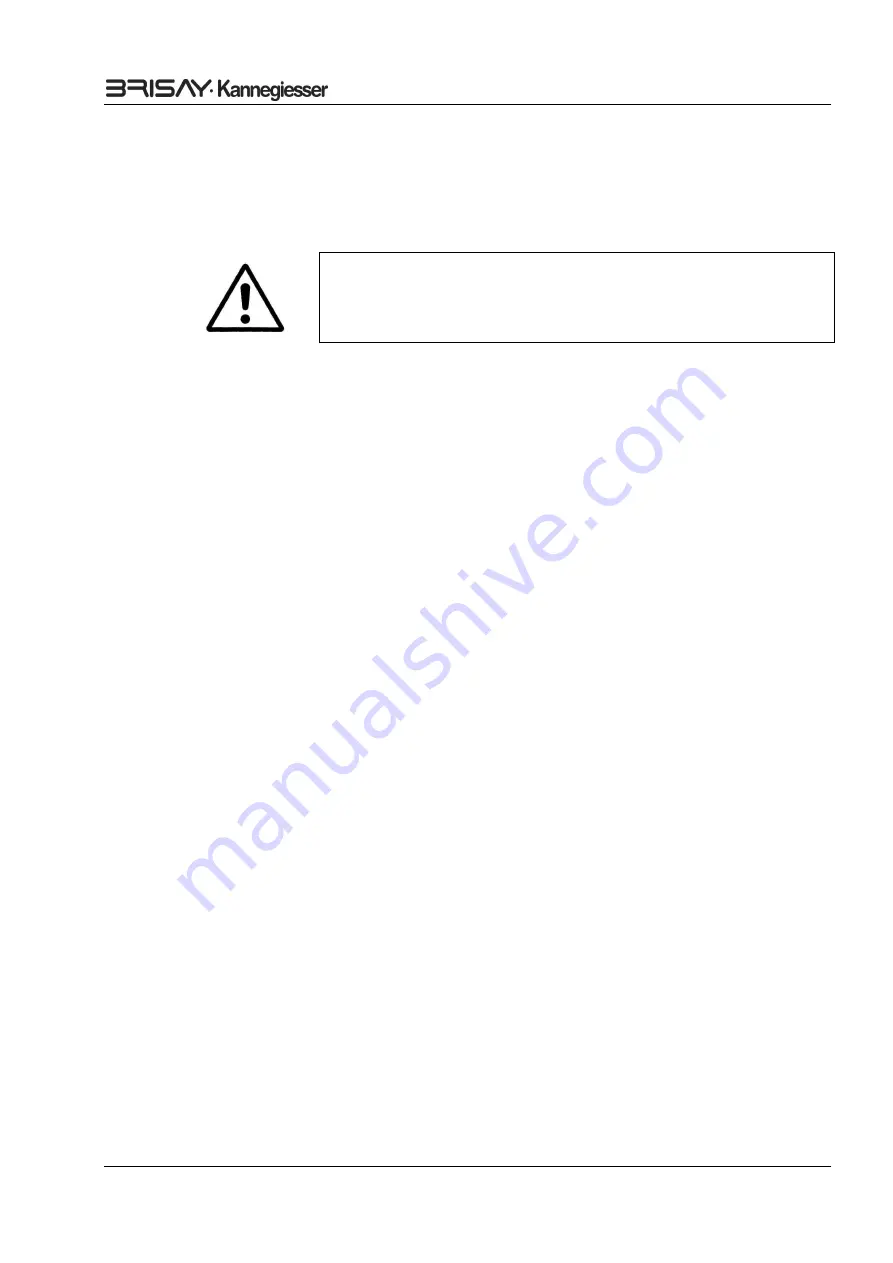
Maintenance and inspection table
14.02.11
BRI-7570_020
49
8.2.1. Machine checks
If all functions are faultless, the machine is handed over to the
operator.
After having examined and replace the wear parts, check all
safety devices for their functioning.
After having finished this work, check
•
the machine for loose connections of the supply lines
(compressed air, steam, condensate, oil),
•
the machine for wear marks or damages and remedy them
if necessary,
•
the earth connections at the machine,
•
that the work has been carried out completely,
•
that no tools have been left in the machine,
•
that the switch cabinet is closed.
Содержание BRI-7570/101 FPD
Страница 10: ...Scope of delivery 6 BRI 7570_020 14 02 11 ...
Страница 18: ...Safety tests 14 BRI 7570_020 14 02 11 ...
Страница 24: ...Disconnect procedures 20 BRI 7570_020 14 02 11 ...
Страница 54: ...Maintenance and inspection table 50 BRI 7570_020 14 02 11 ...
Страница 60: ...Emergency 56 BRI 7570_020 14 02 11 ...
Страница 62: ...Dismantling Disposal 58 BRI 7570_020 14 02 11 ...
Страница 67: ...EC declaration of conformity 14 02 11 BRI 7570_020 63 13 EC DECLARATION OF CONFORMITY ...
Страница 68: ...EC declaration of conformity 64 BRI 7570_020 14 02 11 ...