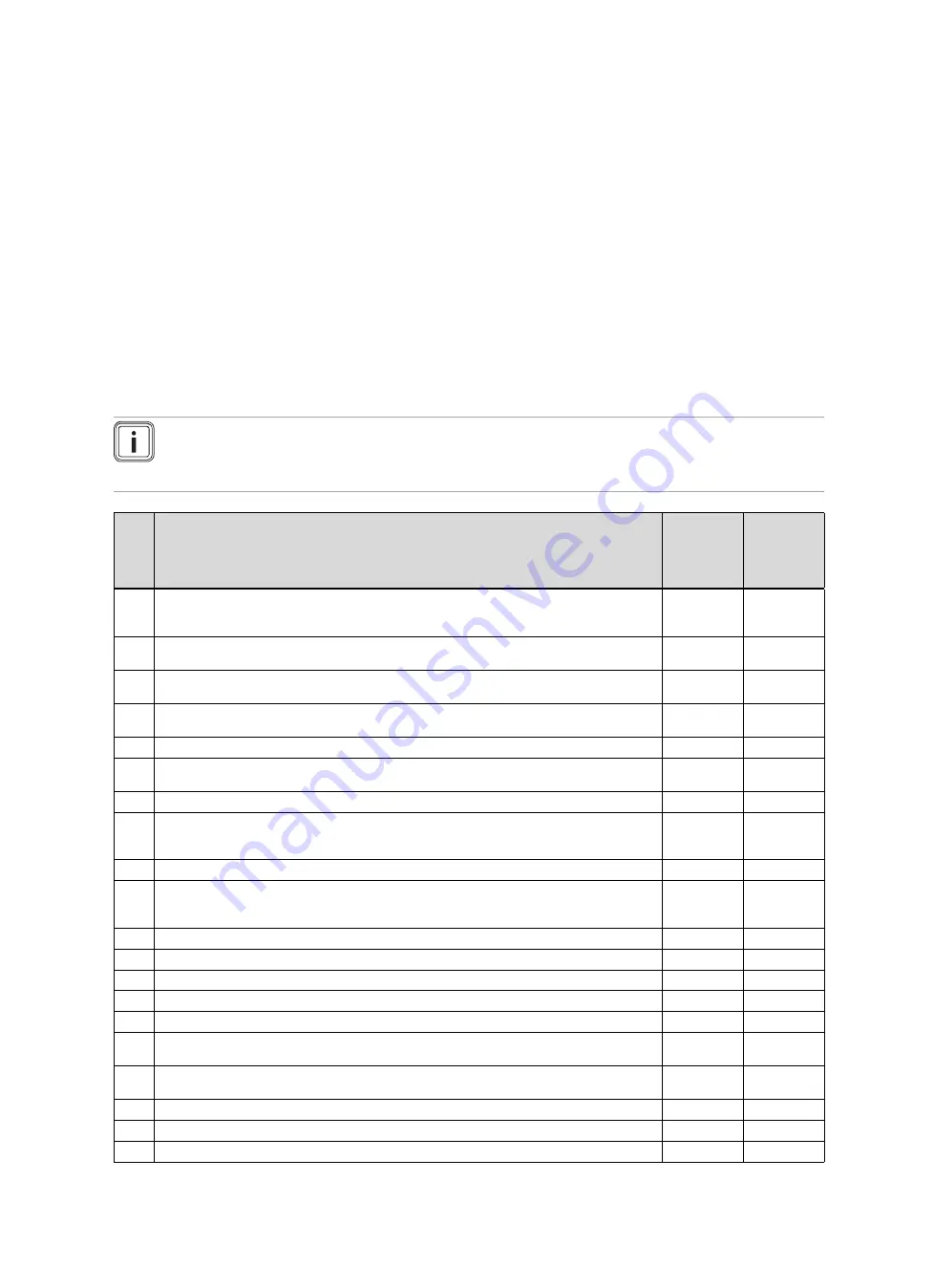
Appendix
46
Installation and maintenance instructions ecoTEC exclusive 0020186710_06
1
Main PCB
2
Control panel PCB
3
All-gas sensor
4
Gas valve assembly
5
Outdoor temperature sensor, flow temperature
sensor (optional, external), DCF receiver
6
Circulation pump remote control
7
Return temperature sensor
8
Flow temperature sensor
9
Fan
10
Surface-mounted thermostat/burner off
11
24 V DC room thermostat
12
Bus connection (digital room thermostat/control)
13
Prioritising diverter valve
14
Water pressure sensor
15
Cylinder temperature sensor
16
Cylinder contact "C1/C2"
17
Internal heating circuit flow rate sensor
18
Internal heating circuit differential pressure sensor
19
Internal pump
20
Gas family coding resistor
21
Additional relay (select via D.026)
22
Circulation pump
23
Ignition electrode
24
Communication unit (optional)
G
Inspection and maintenance work
–
Overview
Note
The table below lists the manufacturer requirements with respect to minimum inspection and maintenance inter-
vals. If national regulations and directives require shorter inspection and maintenance intervals, you should ob-
serve these instead of the intervals listed in the table.
No.
Work
Inspection
(annual)
Mainten-
ance
(At least
every
two years)
1
Check the air/flue pipe for leak-tightness and to ensure that it is fastened correctly. Make sure
that it is not blocked or damaged and has been installed in accordance with the relevant set-up
instructions.
X
X
2
Check the general condition of the product. Remove any dirt from the product and the vacuum
chamber.
X
X
3
Visually inspect the general condition of the product. In doing so, pay particular attention to signs
of corrosion, soot and other defects.
X
X
4
Check the gas flow pressure at maximum heat input. If the gas flow pressure is not within the
correct range, carry out maintenance work.
X
X
5
Check the product's CO
₂
content (air ratio) and adjust this, if required. Keep a record of this.
X
X
6
Disconnect the product from the power grid. Check that the electrical plug connections and other
connections are seated correctly and correct these if necessary.
X
X
7
Close the gas stopcock and the service valves.
X
8
Drain the product on the water side (observe the manometer). Check the pre-charge pressure
of the expansion vessel and top the vessel up, if necessary (approx. 0.3 bar below the system
filling pressure).
X
9
Remove the compact thermal module.
X
10
Check the insulating mats in the combustion area. If you notice any damage, replace the insu-
lating mats. Replace the burner flange seal
each time
it is opened and accordingly
each time
maintenance work is carried out.
X
11
Clean the heat exchanger.
X
12
Check the burner for damage and replace it if necessary.
X
13
Check the condensate siphon in the product, clean and fill if necessary.
X
X
14
Install the compact thermal module.
Caution: Replace the seals.
X
15
Open the gas stopcock, reconnect the product to the mains and switch it on.
X
X
16
Open the service valves, fill up the product/heating installation to 1.0-2.0 bar (depending on the
static height of the heating installation) and start the purging programme
P.00
.
X
17
Run a function test for the product and the heating installation
–
especially the domestic hot
water generation. Then purge the installation again, if required.
X
X
18
Check the gas type.
X
19
Visually inspect the ignition and burner behaviour.
X
X
20
Check the CO
₂
content (the air ratio) of the product again.
X