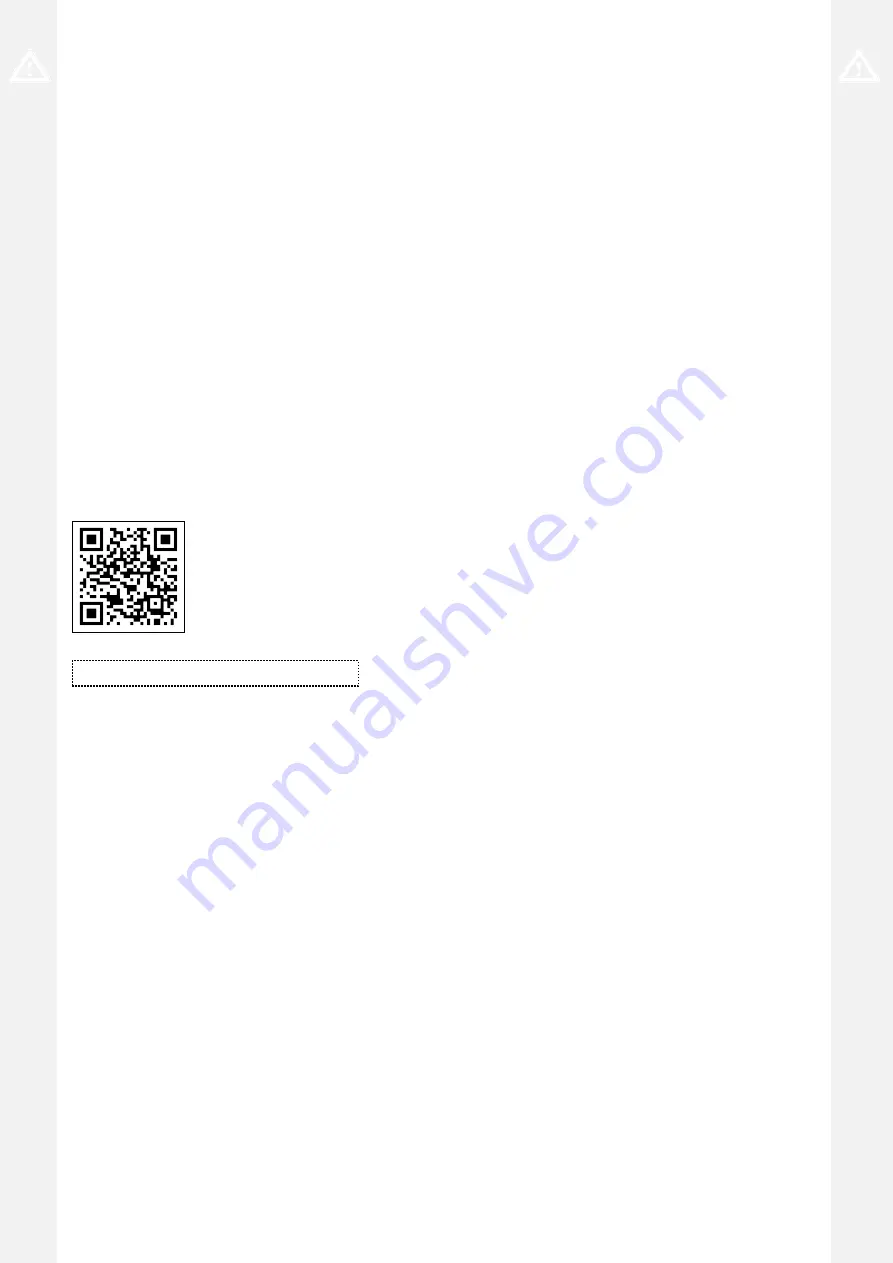
0020230531_06 ecoFIT pure Installation and maintenance instructions
5
▶
Observe local regulations on neutralising
condensate.
1.3.9 Frost
To prevent material damage:
▶
Do not install the product in rooms prone
to frost.
1.3.10 Safety devices
▶
Install the necessary safety devices in the
installation.
1.4
Regulations (directives, laws,
standards)
▶
Observe the national regulations, stand-
ards, directives, ordinances and laws.
1.5
List of relevant standards for Great
Britain and Ireland
▶
Observe the national regulations, stand-
ards, directives, ordinances and laws.
You can find a list of relevant standards at
:
Содержание ecoFIT pure Series
Страница 1: ...en Installation and maintenance instructions ecoFIT pure 825 835 0020230531_06 27 07 2020...
Страница 55: ......