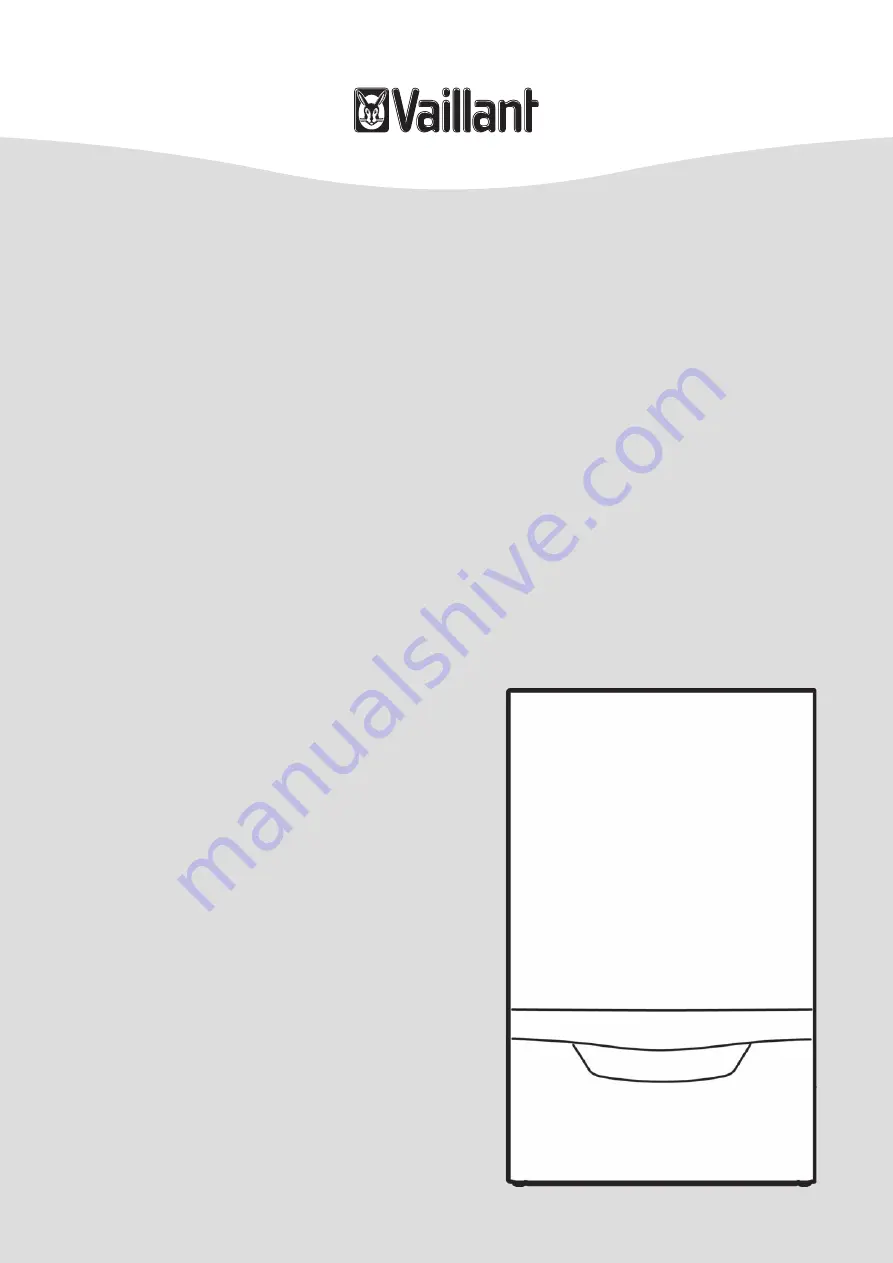
Installation and maintenance instructions
ecoTEC plus
VU ..6/6-5 OVZ (H-GB)
0020238195_07 - 12.10.2020
Содержание 0010015674
Страница 1: ...en Installation and maintenance instructions ecoTEC plus VU 6 6 5 OVZ H GB 0020238195_07 12 10 2020...
Страница 54: ......
Страница 55: ......