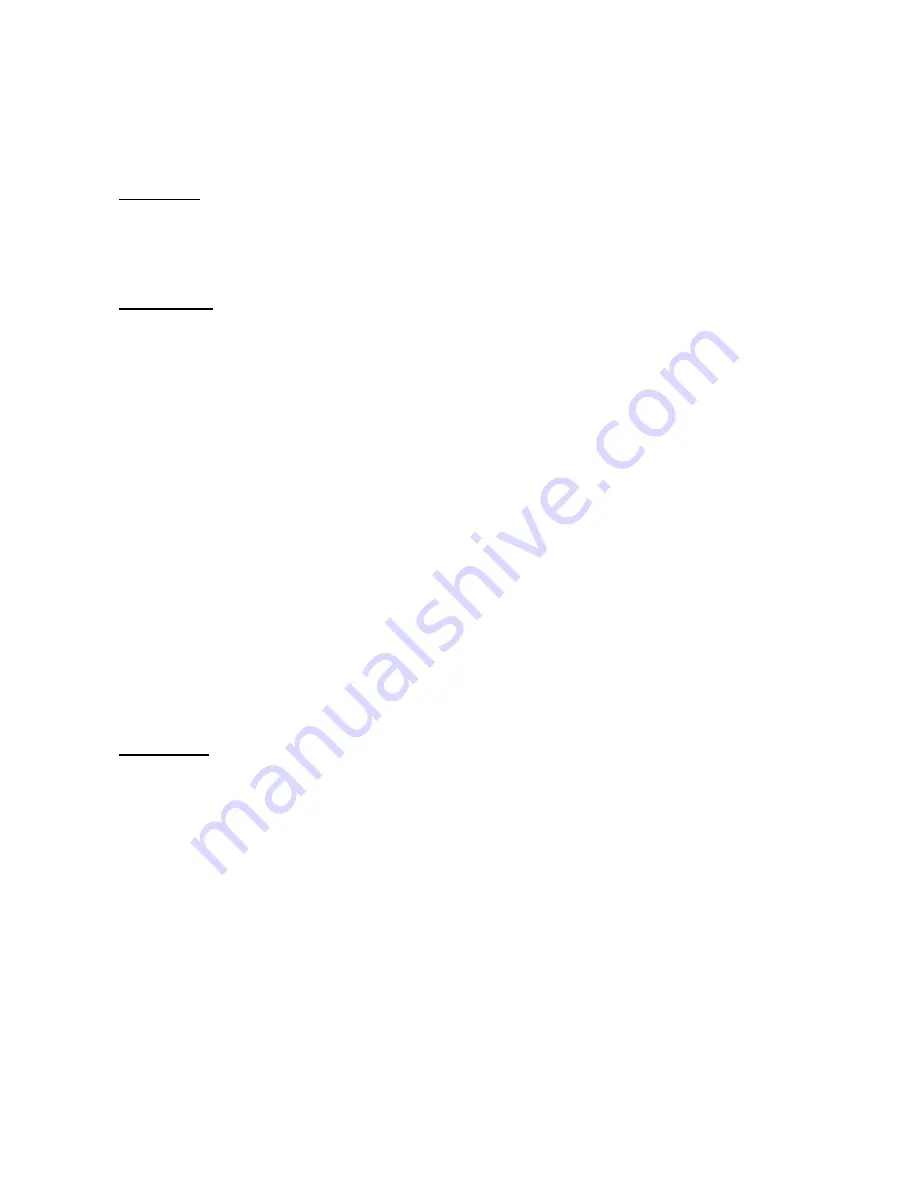
37
21. ENCLOSURE
21.1 RECOMMENDATIONS FOR A GOOD WORKING BOOSTER UNIT
In order to get a good working booster unit we would like to point out a few things that are important.
Circulation
The capacity of one circulation/booster pump should be 2,5 to 4 times the max fuel
consumption
The capacity of one feeder pump should be 1,5 to 2 times the max fuel consumption
Fuel velocity
Fuel velocity depends on the capacity of the circulation/booster pump and the inner diameter of the
pipe that is used. A larger inner diameter will give a slower fuel velocity.
The recommended fuel velocity in the booster unit is 1 - 2 m/sec
The recommended fuel velocity to and from the engines is 0,25 – 0,5 m/sec
Remarks:
A too high fuel velocity will result in larger pressure losses within the booster unit.
A too high fuel velocity can result in unstable viscosity measurements.
A too low fuel velocity will result in a slow and possibly unstable viscosity control
VAF Instruments delivers the
ViscoSense
®
3
with housing. Refer to the table below for flow rate
corresponding to the size of housing:
Fluid flow rate in piping
(Recommended for correct control function)
All at 0-50 mPa.s
2” - Max 20 m3/h, Min 7m
3
/h
2.5” - Max 34 m3/h, Min 12m
3
/h
3” - Max 51 m3/h, Min 18m
3
/h
4” - Max 80 m3/h, Min 28m
3
/h
For lower flowrates a smaller pipe diameter is
recommended.
Mixing tank
The mixing tank is an important part of the booster system that has several functions.
The mixing of MDO and HFO to a homogeneous emulsion.
The mixing of hot ( +/- 130° C ) with colder (+/- 80 °C ) fuel, to a fuel with a single temperature
Compensation of pressure pulses
Prevention of a thermal shock of the engine when changing over from HFO to MDO.
Remarks
If hot and cold HFO is not mixed well, it can result is incorrect viscosity measurements, which
will result in an incorrect viscosity control of the system
High or constant pressure pulses in the system can lead to damage to the
ViscoSense
®
3
sensor or other components of the booster unit.