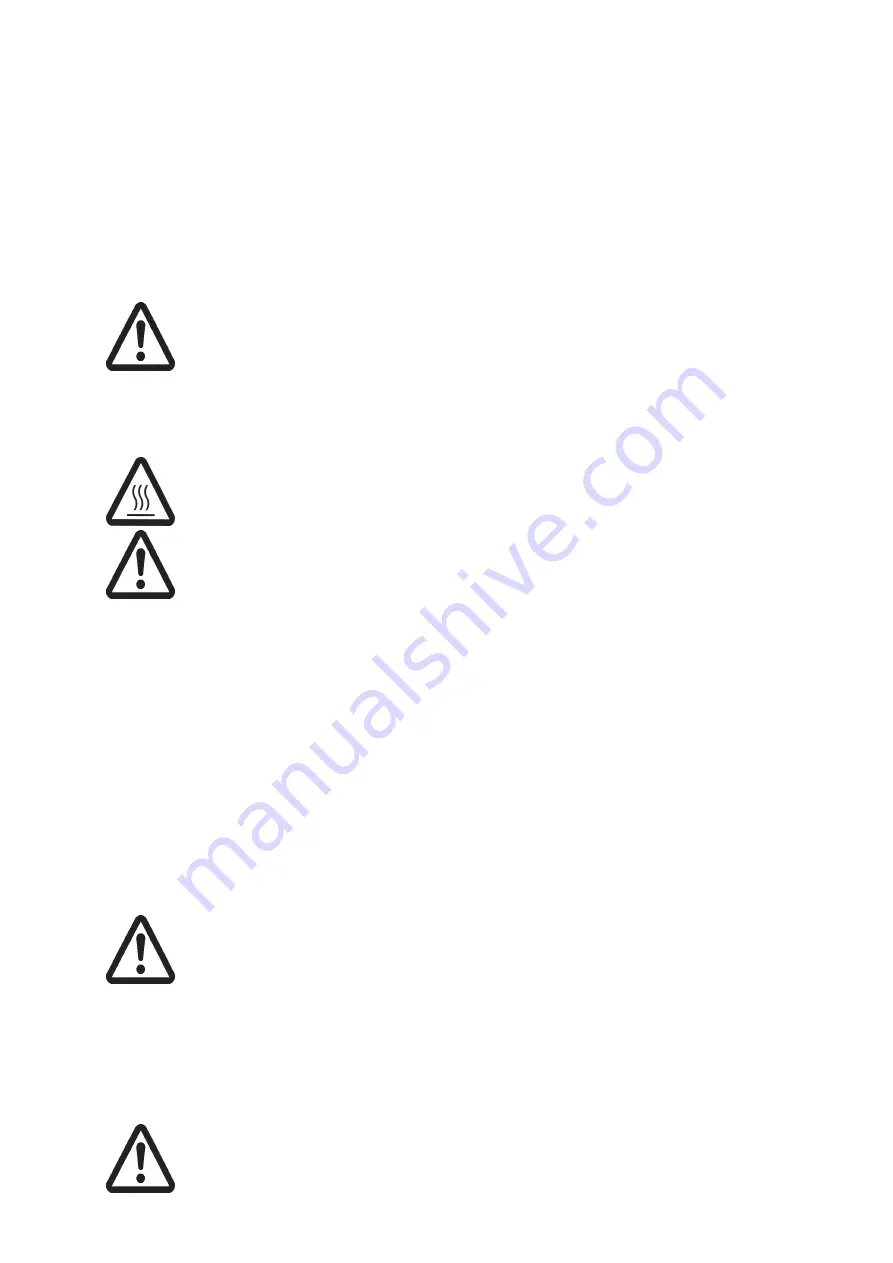
page 5 of 49
Documents are only to be used and distributed completely and unchanged. It is strictly the users´ responsibility to check
carefully the validity of this document with respect to his product. manual-no.: 999100 / 06/05/2008
☞
Ensure that the system design does not allow the coolant outlet pipeline to become
blocked.
☞
Secure coolant hoses at the hose nozzles (e.g. with hose clip) to prevent their
accidental slipping.
☞
Check liquid level in both catchpots regularly and drain condensate in time.
☞
Check the overpressure safety relief device at the exhaust waste vapour condenser
in appropriate intervals.
☞
Avoid overpressure of more than 0.2 bar in case inert gas is connected.
☞
The diameter of the inlet and outlet pipeline should be at the least as large as the
diameter of the pump connection pipelines.
To the best of our knowledge the equipment is in compliance with the requirements of
the applicable EC-directives and harmonized standards (see “Declaration of conform-
ity”) with regard to design, type and model, especially directive IEC 1010. This directive
gives in detail conditions, under which the equipment can be operated safely (see also
IP degree of protection).
☞
Adopt suitable measures in case of differences, e. g. using the equipment outdoors,
installation in altitudes of more than 1000 m above mean sea level, conductive
pollution or dewiness.
Pay attention to symbol “hot surfaces“ on the equipment (according to IEC 1010 rec-
ommendation).
☞
Adopt suitable measures to prevent any danger arising from the formation of hot
surfaces or electric sparks.
The pumps have no approval for operation in or for pumping of potentially ex-
plosive atmospheres.
If pumping
different substances
, purge the pump with inert gas prior to changing the
pumped media in order to pump out residues and to avoid reactions of the pumped
substances with each other with and the pump material.
Take into consideration interactions and chemical reactions of the pumped media.
The pumps are
not suitable
for pumping substances which may form
deposits
inside
the pump.
☞
If there is a danger of the formation of
deposits
in the pump chamber (check inlet
and outlet of the pump) inspect the pump chamber regularly and clean if necessary.
The pumps are
not suitable
to pump
unstable substances
and substances which
react explosively under
impact
(mechanical stress) and/or when being exposed to
elevated temperatures
without air.
The pumps are
not suitable
to pump
self inflammable
substances, substances which
are inflammable without air and
explosive substances
.
The pumps are
not suitable
for pumping dust and have
no approval
for operation
below ground.
Ensure that the materials of the wetted parts are compatible with the pumped sub-
stances, see section “Technical data”.
☞
Adopt suitable measures to prevent the release of dangerous, explosive, corrosive
or polluting fluids.
☞
Use inert gas for gas ballast if necessary.
☞
The user must take suitable precautions to prevent any formation of explosive
mixtures in the pump. In case of a diaphragm crack, mechanically generated sparks,
hot surfaces or static electricity may ignite these mixtures.
☞
Take adequate precautions to protect people from the effects of dangerous sub-
stances, wear appropriate safety-clothing.
☞
Comply with applicable regulations when disposing of chemicals. Take into consid-
eration that chemicals may be polluted.
The motor is protected by a
temperature sensor at the circuit board:
Current limita-
tion if the temperature at the circuit board is higher than 70°C, switching off the pump
if the temperature is higher than 85°C.