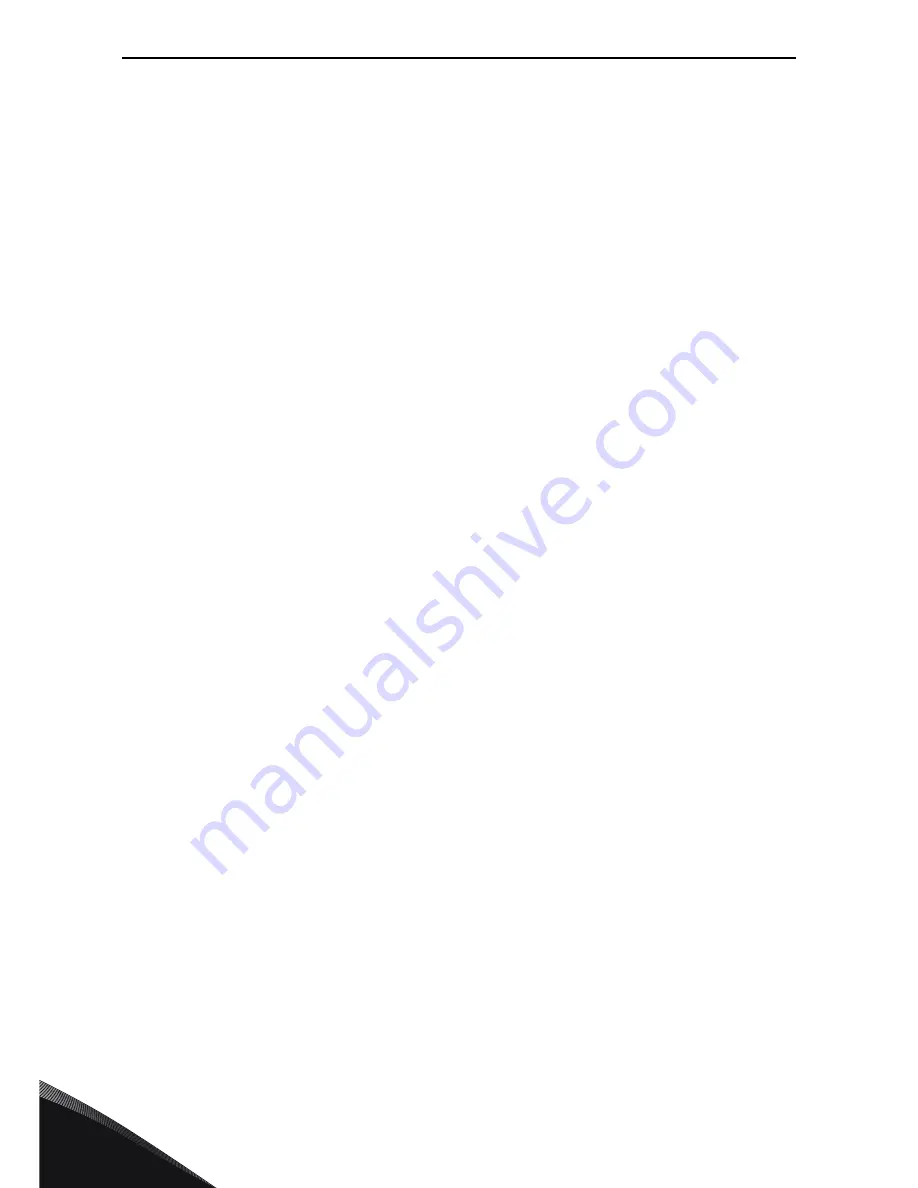
5
vacon • 52
Technical information
Tel. +358 (0) 201 2121 • Fax +358 (0)201 212 205
5.
T
ECHNICAL
INFORMATION
5.1
Control and interface
Speed and/or torque control functions are available in the drive. Speed and/or torque reference as
well as command word is generated by the overriding line control system and individually
transmitted to each drive either via fieldbus or hardwired signals. The drive transmits selected
actual values as well as status words back to the line control system.
5.1.1
Control without speed feedback (open loop)
•
Speed error in steady state typically <0.5%
•
Torque rise time <10 ms
•
Torque error in steady state typically <3%
•
Suitable also for multimotor configuration
5.1.2
Control with speed feedback (closed loop)
Full torque control at zero speed cannot be maintained without speed feedback. When a speed error
of less than 0.5% or full torque control at all speeds is required, motor control based on feedback
from an encoder is a necessity. This capability is incorporated into the NXP drive. In addition to the
current measurement system used, the NXP drive utilizes feedback values from the encoder to
determine the motor state. The enhanced microprocessor provided with the NXP drive is capable of
calculations every 150 microseconds. This control can be used for applications requiring high
precision, such as sectional drives.
•
Speed error in steady state typically <0.01% (pulse encoder type dependent)
•
Pulse encoder: 250-5000 ppr at 5, 12 or 24 V (option board dependent)
•
Torque rise time <10 ms
•
Torque error in steady state typically <3%
5.2
Load definitions
The drives are normally selected based on the load definition shown in the drive list, where:
•
n
min
= minimum speed [RPM], beginning of the continuous constant torque load speed
range
•
n
base
= base speed [RPM], end of the continuous constant torque load speed range (and
beginning of the continuous constant power load speed range)
•
n
max
= maximum speed [RPM], end of the continuous constant power load speed range (also
maximum allowed motor speed)
•
P
[
n
base
] = base power [kW], motor shaft power at the end of the continuous constant torque
load speed range (also motor shaft power of the continuous constant power load speed
range)
•
T
[
n
base
] = base torque [Nm], motor shaft torque of the continuous constant torque load
speed range (also motor shaft torque at the beginning of the continuous constant power
load speed range)
•
OL
= overload [%], short time maximum load, 1 min. / 10 min. (100% = no overload)
NOTE!
Load is defined based on the information received. VACON
®
Plc is not responsible for
verifying that the information is sufficient and accurate.
There are various possibilities to define the load curve. Below are some examples.
Содержание NXP
Страница 1: ...vacon nxp ac drives system drive hardware manual...
Страница 2: ......
Страница 77: ......