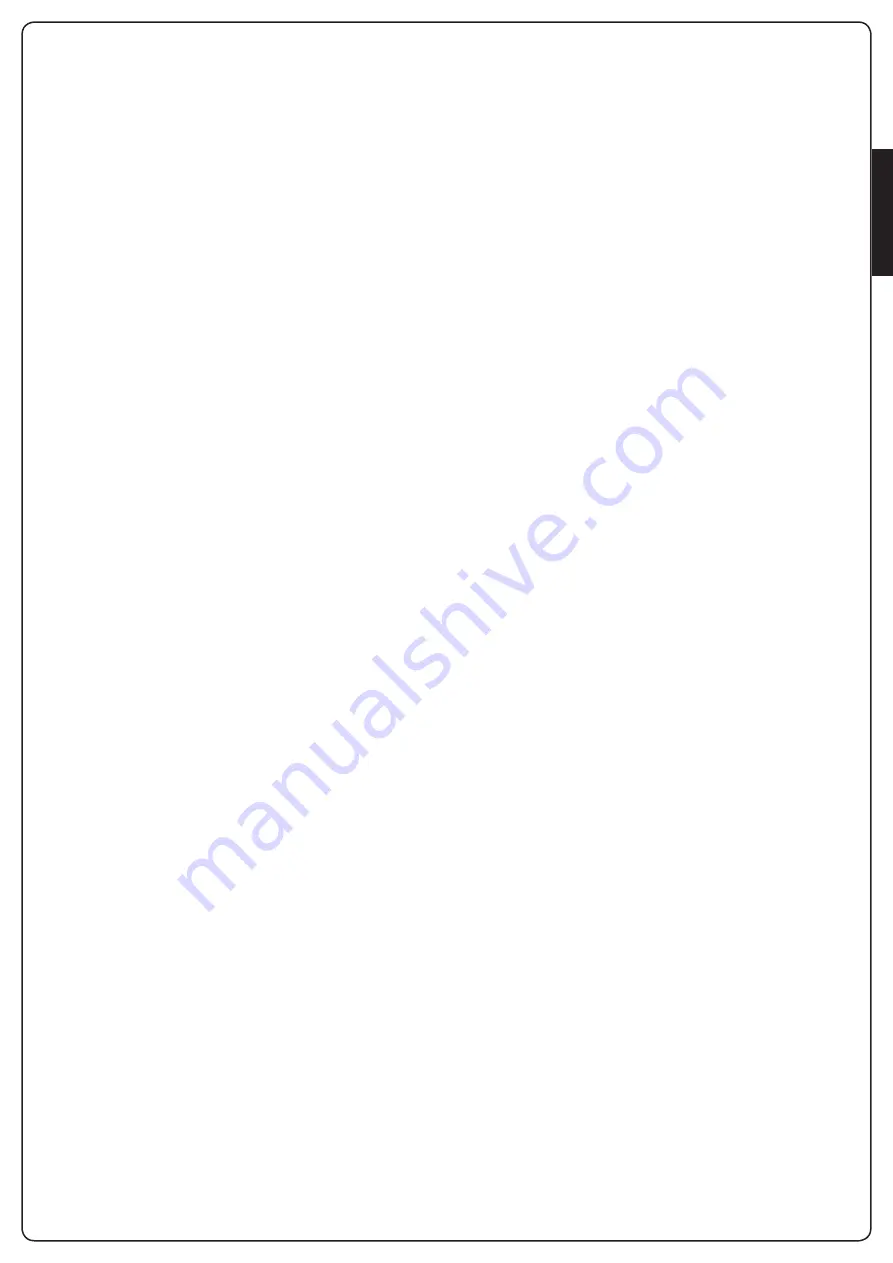
ENGLISH
- 53 -
13 - OPERATION DEFECTS
This paragraph shows some possible operation defects, along
with their cause and applicable remedy.
MAINS led does not switch on
It means that there is no voltage on PD14 control unit card.
1.
Before acting on the control unit, disconnect through the
disconnecting switch on the power line and remove the power
supply terminal.
2.
Be sure that there is no voltage break upstream the control
unit.
3.
Check whether the fuse is burnt-out, if so replace it with same
value.
OVERLOAD led is on
It means that there is an overload on accessory power supply.
1.
Remove the extractable part containing terminals J1 to J9.
OVERLOAD led will switch off.
2.
Remove the overload cause.
3.
Reinsert the terminal board extractable part and check that this
led is not on again.
Too long pre-blinking
When a Start command is given and the blinker switches on
immediately but the gate is late in opening, it means that the
setup cycle count down expired and the control unit shows that
service is required.
Slow movement of the gate while closing
This condition can occur when the motor encoder must be
realigned: the gate is closed at slow speed until the closed range
limit and after resumes normal operation.
This anomaly can occur due to power failure with the gate open
or due to other factors related to the malfunctioning of the gate.
Error 1
The following writing appears on display when you exit from
programming
Err1
It means that changed data could not be stored.
This kind of defect has no remedy and the control unit must be
sent to V2 S.p.A. for repair.
Error 2
When a Start command is given and the gate does not open and
the following writing appears on display
Err2
It means that MOSFET test failed.
Before sending the control unit to V2 S.p.A. for repair, be sure
that motors have been properly connected.
Error 3
When a Start command is given and the gate does not open and
the following writing appears on display
Err3
It means that the photocell test failed.
1.
Be sure that no obstacle interrupted the photocell beam when
the Start command was given.
2.
Be sure that photocells, as enabled by their relevant menus,
have been installed actually.
3.
If you have photocells 2, be sure that
Fot2
menu item is on
CF.Ch
.
4.
Be sure that photocells are powered and working; when you
interrupt their beam, you should hear the relay tripping.
Error 4
When a Start command is given and the gate does not open (or
does a partial opening) and the following writing appears on
display
Err4
This anomaly can occur when in one of the following conditions:
1.
If a START command is sent with the motor released.
2.
During the self-learning cycle if there are any problems with
the range limits.
Check the direction of the magnets, if they are backwards,
they should be removed and inverted.
If the magnets are installed correctly, it means that the limit
switch sensor is damaged or the cabling connecting the sensor
to the central control unit is broken/damaged.
Change the end of stroke sensor or the broken wiring.
3.
During normal operation. If the error persists send the control
unit to V2 S.p.A. for repair.
Error 5
Once given a start control, the gate does not open and the
display shows
Err5
It means that the test of the safety edges failed.
Check that the menu of the test of safety edges (
Co.tE
) have
been set correctly.
Check that the safety edges enabled from the menu are installed.
Error 7
When a Start command is given and the gate does not open (or
does a partial opening) and the display shows
Err7
This indicates an error in the encoders’ operation.
There are two possible causes:
1.
Once a START command is received: this means that the
encoders have not been initialized. For the encoders to operate
correctly, the self-learning procedure must be performed.
2.
A few seconds after movement begins: this means that the
encoder is NOT correctly operating. Encoder malfunction or
broken connection.
Error 8
When executing a self-learning function, one of the following
conditions occurs:
1.
the control is refused and the display shows
Err8
It means that the setting of the control unit is not compatible
with the requested function.
In order to carry out self-learning, the Start inputs must be
enabled in standard mode (
Strt
menu set to
StAn
) and the
ADI interface must be disabled (
i.Adi
menu set to
no
).
2.
The procedure stops and the displays shows
Err8
It means that a safety device has tripped.
Error 9
When you are trying to change the control unit setups and the
following writing appears on display
Err9
It means that programming was locked by means of the
programming lock key CL1+ (code 161213).
To change the settings it is necessary to insert in the connector of
the ADI interface the same key used to activate the programming
lock, and unlock the device.