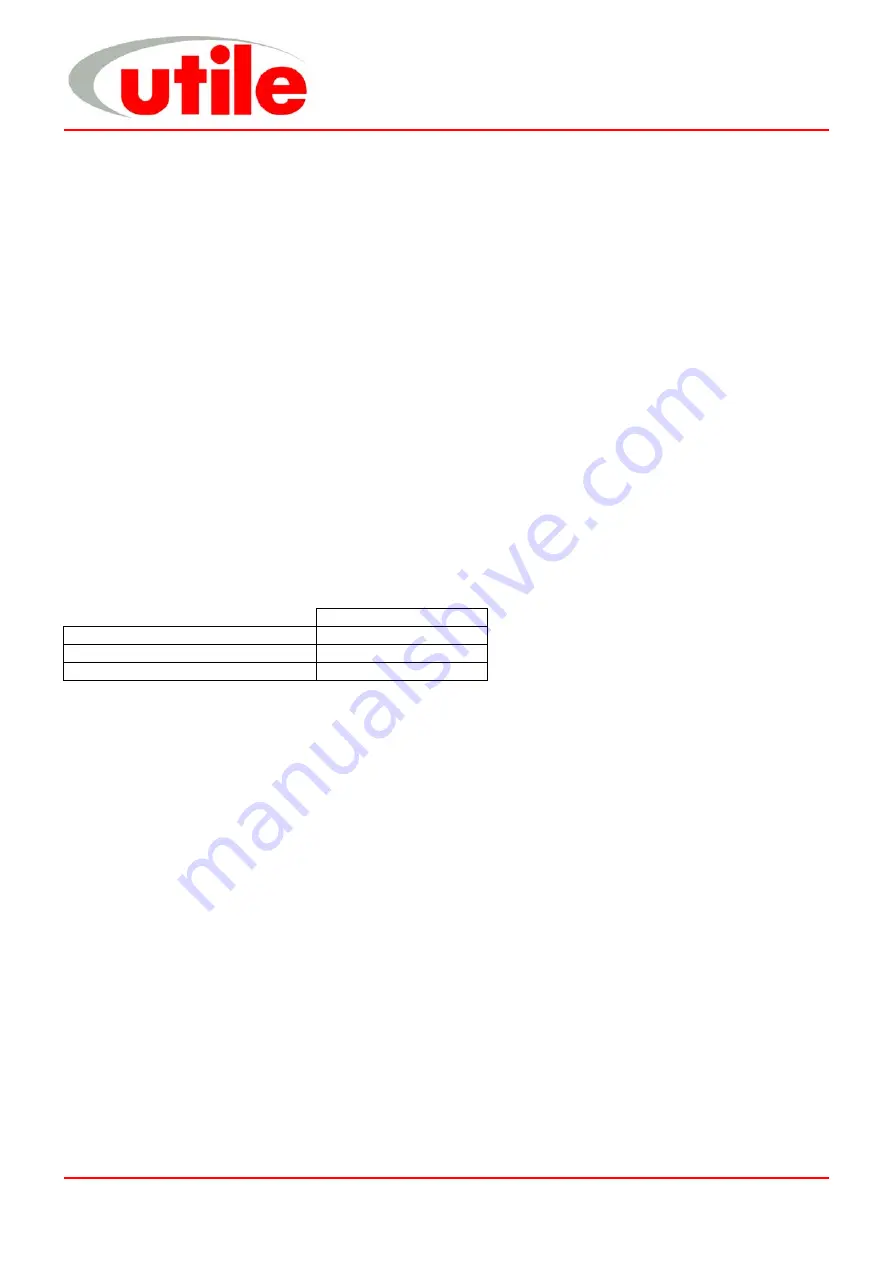
The Utile Engineering Co. Ltd.
12/10/05
Irthlingborough, Northamptonshire. England
Tel: +44 (0) 1933 650216
Fax: +44 (0) 1933 652738
13
IC191
5.4
Inspect the bearing, renew if it shows any signs of wear or pitting.
5.5
Examine the bearing seal (14) and renew if the wiping lip is worn or damaged.
5.6
The two oil pump seals (28) and felt seal (29) can be removed from the end cap for inspection.
With the drive end coverplate (2) already removed complete with rotor as described in 4 for cylinder renewal.
5.7
Undo four screws (20) and remove end cap (4) together with the mechanical seal seat. Do not loose the o-
ring (24) fitted between the endcap and coverplate.
5.8
Remove the mechanical seal (16) taking care not to damage the carbon face. The rubber bellows may
cause the seal to stick on the shaft, but by carefully prising between the spring locating ring and the locknut
(17) taking care not to scratch the shaft the complete seal can be removed for examination for wear.
5.9
Undo the locknut (17) and tab washer (18).
5.10
The coverplate (2) can be tapped off the shaft, taking the ball bearing (12), outer race of roller bearing (10)
and bearing seal (13) with it.
5.11
The bearing seal (13), roller bearing outer race (10) and ball bearing (12) can be pressed out of the
coverplate for inspection.
5.12
Using a two-leg pulley drawer the roller bearing inner race (10) can be removed from the shaft.
5.13
Inspect the bearing, renew if it shows any signs of wear or pitting.
5.14
Examine the bearing seal (13) and renew if the wiping lip is worn or damaged.
6.
Reassembly Procedure
This section only applies when using original bore size or replacement cylinder. Before commencing reassembly
ensure that all components are perfectly clean and oilways are clear. Lightly smear the shaft with oil to assist
assembly.
The correct clearances for these machines are: -
LGB32
Drive End Coverplate / Rotor
0.05mm / 0.08mm
Rear End Coverplate / Rotor
0.15mm / 0.18mm
Rotor / Cylinder
0.08mm / 0.10mm
Reassembly should start with the preparing of the rotor and shaft assembly by the fitting of the replacement seal
sleeve (if required) and the inner races of the both roller bearings.
6.1
The seal sleeve (8) are retained on the clean shaft using LOCTITE 648 adhesive or equivalent, and should
be pushed hard against the rotor face. It is essential that the width of the seal sleeve is identical to the one
it is replacing or internal clearances may be effected causing serious machine damage.
6.2
Both roller bearing inner races can now be fitted onto the shaft ensuring any shims fitted are fitted to the
correct ends.
Starting at the drive end
6.3
Position the bearing seal (13) into position in the coverplate (2) ensuring that the tension spring is facing
the rotor.
6.4
Press the outer race of roller bearing (10) into position in the coverplate (2).
6.5
Ease coverplate (2) onto the rotor/shaft.
6.6
Tap the ball bearing (12) into position using a soft hammer, the whole bearing assembly can be locked
onto the shaft with the locknut (17) and tab washer (18). Set clearance.
6.7
When fitting the mechanical seal (16), wipe over the shaft with soapy water to assist the assembly, the seal
can then be eased onto the shaft and pushed against the locknut. Replacement seal seats should be
lubricated for easier fitting in the end cap.
6.8
The end cap (4) can now be fitted with the o-ring (24) and any appropriate shims.
6.9
Press coverplate o-ring (23) in position.
6.10
Turn cylinder (1) upside down for ease of assembly.
6.11
Place drive coverplate assembly onto cylinder (1) via location dowels (22) and bolt with 6 screws (20) and
with coverplate o-ring (23) in place.
6.12
Check rotor / cylinder clearance.
Reassembly Procedure