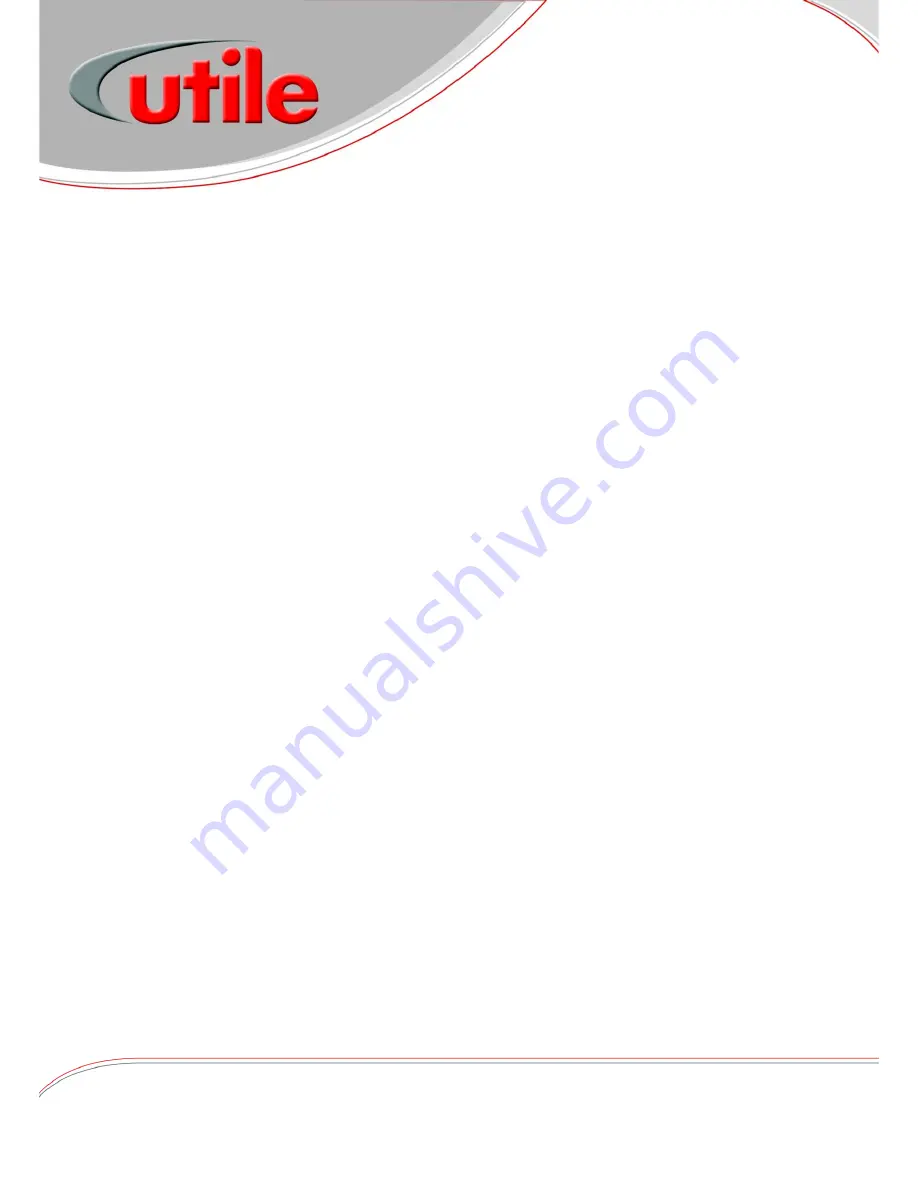
GAS COMPRESSORS / BOOSTERS
GAS & AIR MIXING SYSTEMS
AIR BLOWERS & VACUUM PUMPS
The Utile Engineering Co. Ltd.
Irthlingborough, Northamptonshire, NN9 5UG, ENGLAND
Telephone: + 44 (0) 1933 650216 Facsimile: + 44 (0) 1933 652738 Email: [email protected]
www.utileengineering.com
8
IC182
Pipework
The connecting pipework must be completely clean, dry and free from internal rust or scale.
When fitting the intake and discharge pipework it is essential that adequate supports be provided and that it is properly
aligned to prevent excessive strain being placed upon the machine, flexible pipe should be placed in the pipeline to
remove this strain.
During installation care must be taken to ensure that no foreign matter enters the machine or serious damage may
result.
An intake filter should be fitted into the intake side to prevent any particles from entering the machine.
Use P.T.F.E. tape only as a jointing medium since surplus from jointing compounds will damage the blades if drawn
into the machine.
When the machine is delivering into or exhausting from a receiver, or working with a system having a large storage
capacity, it is essential to fit a non-return valve in the pipework, preferably on the intake side to prevent the machine
from running in reverse on shutdown.
Arrange both the intake and discharge pipework so that any condensate flows away from the machine.
If user is installing their own protective switches and other devices these must be suitable for operation in the zone
classified.
All pipework and fittings must comply with IGEM/UP/2 or the national standard for the country of installation.
Pre Start-up Checks
Before starting the machine for the first time after installation, maintenance or after a long downtime, make the following
checks: -
Ensure all the anchor bolts for the machine, base and motor are securely fastened.
Check that the machine is free running by turning the shaft by hand through a few revolutions.
Flick start the motor to check that the direction of rotation agrees with the arrow on top of the machine cylinder. Note
this should be completed with the coupling/drive belts removed.
Recheck coupling/drive alignment and retension (see page 7).
Ensure all equipment is installed and earthed in accordance with current legislation.
Check all piping connections.
If the system is to be pressure tested, all gauges and pressure switches must be isolated or removed. Maximum purge
or pressure test is 1.50 times the working pressure.
Check all protective devices ensuring they are working correctly.
Ensure personnel are adequately protected from accidental contact with all dangerous equipment.
Fill the oil tank with Shell Turbo T68 oil or equivalent (see lubrication), prime the oil lines to the machine.
Instruct the operating personnel that the machine is operational.
Protective Devices
All pressure and temperature switches must be set and tested at the desired set point by simulating the set point in actual
operation.
With the machine running at the duty pressure after warming up, adjust the discharge temperature switch downwards to
actuate and stop the machine. Reset the switch at the cut out temperature plus 10
C - 15
C in order to avoid false tripping
from small and reasonable increases above normal levels.
Adjust the high pressure cut out switch in the same manner and reset at working pressure plus 10%.
After the first 50 running hours, remove the cone shaped mesh strainer from the inlet, clean and replace. If a large amount
of debris has been collected run for a further 50 hour period repeating the process until the filter remains clean.
Start-up
Proceed as follows: -
i.
When starting compressors the intake valves are fully open. Compressors can usually be started against normal
discharge pressure.
ii.
Some compressors are piped with a manual start-up bypass valve from discharge to intake, for pressure equalisation
during startup, This must be fully opened before startup.
iii.
Start the drive motor and bring the machine up to operating speed.
iv.
When full speed is reached slowly close the manual start-up bypass valve.
v.
Check and adjust the lubricator drip rate to that indicated in the lubrication section.
vi.
Check all protective devices and controls making sure they are working correctly.
Pre Start-up Checks
Protective Devices
Start-up