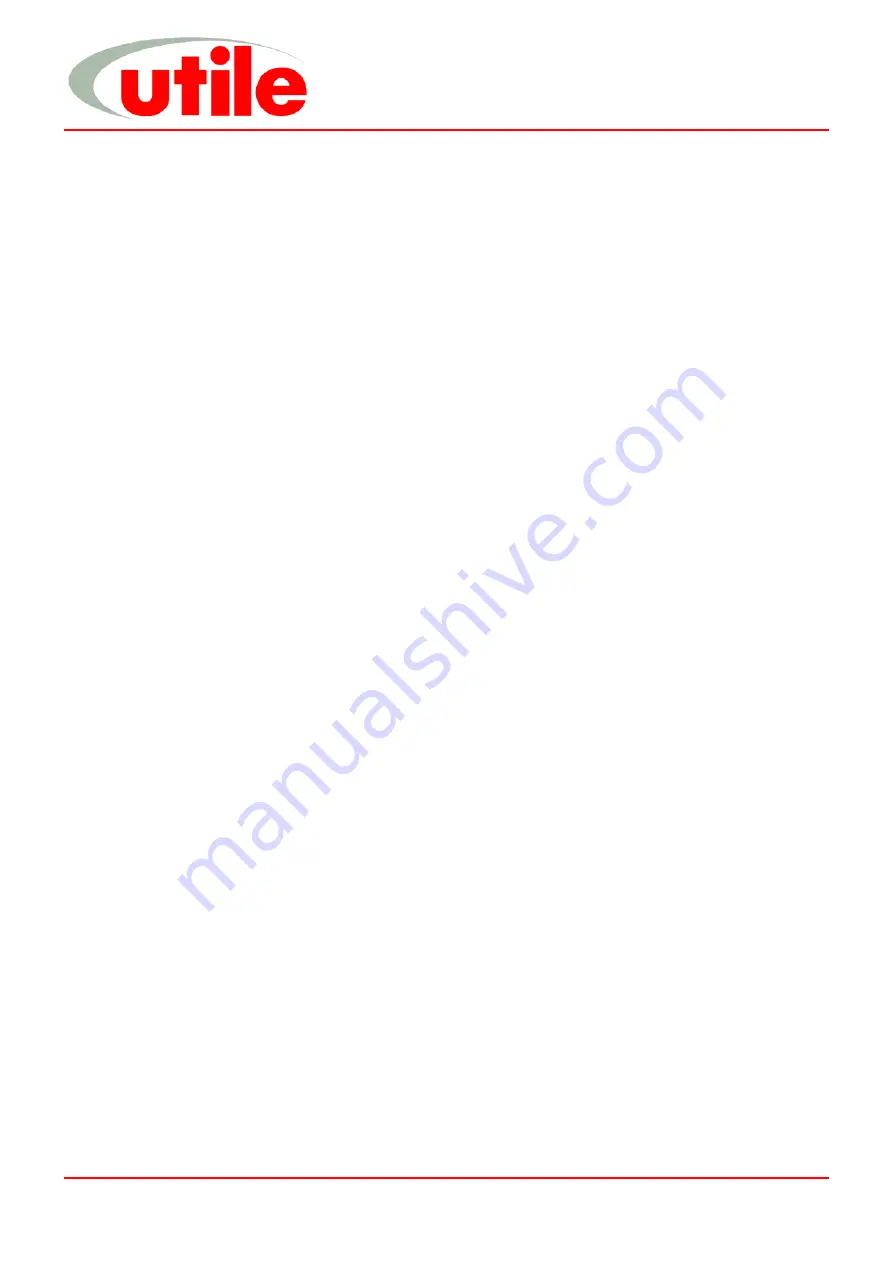
The Utile Engineering Co. Ltd.
15/08/06
Irthlingborough, Northamptonshire. England
Tel: +44 (0) 1933 650216
Fax: +44 (0) 1933 652738
7 IC183
Pipework
The connecting pipework must be completely clean, dry and free from internal rust or scale. When fitting the intake
and discharge pipework it is essential that adequate supports be provided and that it is properly aligned to prevent
excessive strain being placed upon the machine, flexible pipe should be placed in the pipeline to remove this strain.
During installation care must be taken to ensure that no foreign matter enters the machine or serious damage may
result. An intake filter should be fitted into the intake side to prevent any particles from entering the machine.
Use P.T.F.E. tape only as a jointing medium since surplus from jointing compounds will damage the blades if drawn
into the machine.
It is essential to fit a non-return valve in the pipework, preferably on the intake side to prevent the machine from
running in reverse on shutdown.
Arrange both the intake and discharge pipework so that any condensate flows away from the machine.
Vacuum pumps are normally supplied with exhaust silencers.
Earthing
It is important that the all items are suitably earthed by metallic earth continuity conductor, or by separate earth
bonding, but in all cases the installation must be made and tested and approved for this feature by a qualified
installer before the power supply is applied.
Pre Start-up Checks
Before starting the machine for the first time after installation, maintenance or after a long downtime, make the
following checks: -
9
Ensure all the anchor bolts for the machine, base and motor are securely fastened.
9
Flick start the motor to check that the direction of rotation agrees with the arrow on top of the machine cylinder.
Note this should be completed with the coupling/drive belts removed.
9
Recheck coupling/drive alignment and retension.
9
Check that the machine is free running by turning the shaft by hand through a few revolutions.
9
Check all piping connections.
9
Check all protective devices ensuring they are working correctly.
9
Flick start the motor to check that the direction of rotation agrees with the arrow on top of the cylinder.
9
Instruct the operating personnel that the machine is operational.
Start-up
Proceed as follows: -
i. When starting vacuum pumps the intake valve can be closed to reduce the starting power and then slowly
opened as the machine reaches operating speed.
ii. Start the drive motor and bring the machine up to operating speed.
iii. Check all protective devices and controls making sure they are working correctly.
Operating Notes
After the initial running in period, check the belt tension. Belt squeal denotes a loose belt that requires
tightening.
Inspect the filter fitted to the inlet, regularly clean and renew the element when necessary.
Excessive discharge temperature for normal operation as indicated by the rise in temperature shown in the
log book indicates inadequate cooling, or a dirty intake filter. The machine should be stopped and
inspected.
Check the machine internally for wear every 10,000 running hours. (see Inspection and Service)
The blade depth should be checked after the initial 2,000 running hours and thereafter every 5,000 running
hours for wear and renew if the rubbing tips have worn to a depth of 24mm. (See Check Blade Wear).
Condensate if allowed to enter the machine can cause severe blade wear.
Stopping Procedure
Proceed as follows: -
i. When stopping vacuum pumps the intake valve should be slowly closed.
ii. Trip out or Stop the drive motor.
Pre Start-up Checks
Start-up, Operating Notes
Stopping Procedure