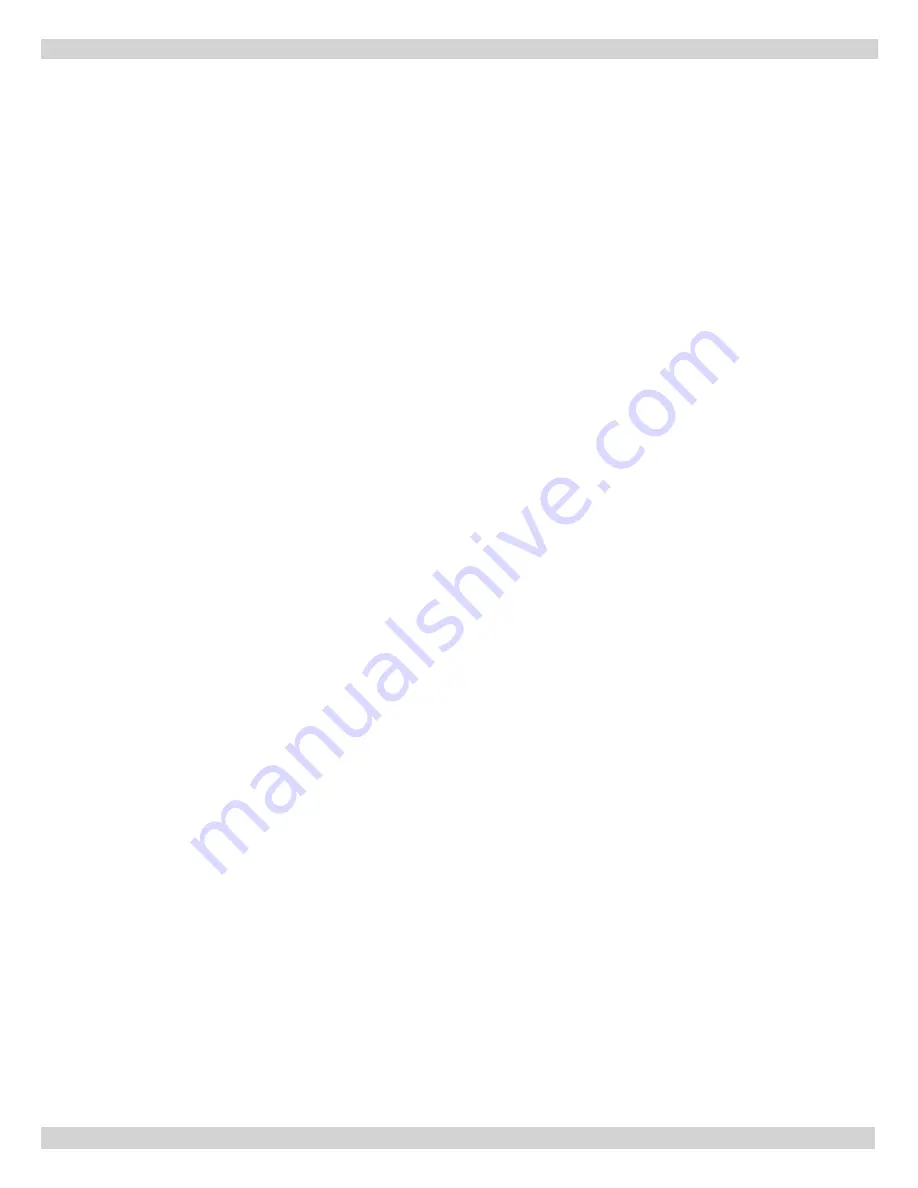
9
3.1 Installation and Operation
1.
Do not operate unit if any control, switch, components
or devices have been underwater or subject to water
damage.
2.
Before servicing, allow boiler to cool. Always shut off any
electricity and oil supply to boiler when working on it.
3.
Inspect oil line and connections for leaks.
4.
Verify oil burner nozzle is proper size. Over-firing could
result in early failure of boiler sections, and result in a
potentially dangerous situation.
5.
Never vent boiler into enclosed space. Always vent to
the outside. Never vent to another room or inside a
building.
6.
Verify adequate air supply for complete combustion.
7.
Relief valve automatically lifts open when system
pressure exceeds 30 psi. Before installing relief valve
read manufacturer’s instructions. Pipe relief valve to a
safe location. Check with authorities having jurisdiction.
8.
Consider system total water volume, temperature,
initial fill pressure and arrangement when sizing and
installing expansion tank. Improperly installed and
sized expansion tank may result in frequent lifting of
relief valve or other heating system problems. Follow
expansion tank manufacturer guidelines for installation,
and sizing.
9.
Boiler manufacturer recommends initial fill pressure of
10-12 psi. For higher fill pressures increase expansion
tank’s air charge to match fill pressure.
10.
Purging heating system of air and gases is critical for
proper circulation and quiet performance. Once the air
is purged, for boiler installations using float type vents,
air vents should be closed for normal operation. If air
is heard or noticed by loss of heat, purge system and
open vents for short period of time.
3.2 Prior To Installing The Boiler
•
Verify you have selected right size boiler with proper
capacity. AHRI rating of boiler selected should be greater
than or equal to calculated peak heating load (heat loss)
for building or area(s) served by boiler and associated
hot water heating systems. Use heat loss calculations
based on approved methods. See Table 1.
• Boiler must be supplied with proper oil supply and oil
piping, sufficient fresh combustion air, and suitable
electrical supply.
•
Connect boiler to suitable venting and piping systems
adequate to distribute heating load.
•
Installation is not complete unless pressure relief valve
is installed in 3/4” tapping located in supply piping.
• Thermostat must be properly located and installed
•
Failure to pipe boiler correctly may result in excessive
noise or other related problems.
Existing Water System Evaluation
A good system will prevent oxygen contamination of boiler
water.
1.
Causes of oxygen contamination may be:
A.
Addition of excessive make up water as a result of
leaks.
B.
Absorption through open tanks and fittings.
C. Oxygen permeable materials in the distribution
system.
2.
To insure long product life, oxygen sources must be
eliminated.
Take the following measures:
A. Repair system leaks.
B. Eliminate open tanks from the system.
C.
Eliminate and/or repair fittings which allow oxygen
absorption.
D. Use non-permeable materials in the heating system.
3 - BEFORE YOU START
PN 240013415 REV A [08/15/2021]