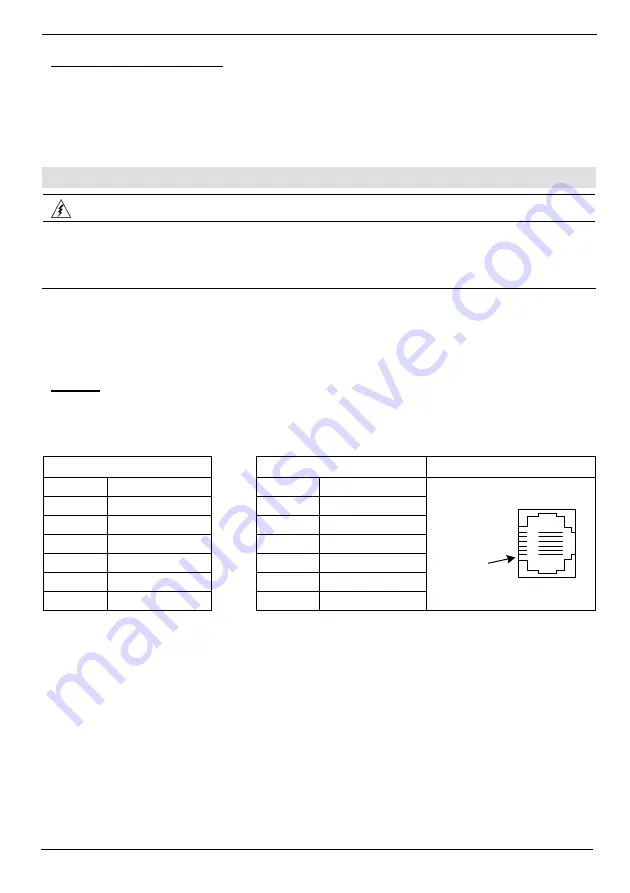
V350-35-TR34 Installation Guide
8
Unitronics
Earthing the Power Supply
To maximize system performance, avoid electromagnetic interference by:
Mounting the controller on a metal panel.
Earthing the controller’s power supply: connect one end of a 14 AWG wire to the chassis
signal; connect the other end to the panel.
Note: If possible, the wire used to earth the power supply should not exceed 10 cm in length.
However, it is recommended to earth the controller in all cases.
Communication Port
Turn off power before making communications connections.
Caution
Signals are related to the controller’s 0V; the same 0V is used by the power supply.
Always use the appropriate port adapters.
The serial port is not isolated. If the controller is used with a non-isolated external
device, avoid potential voltage that exceeds ± 10V.
Port 1 is type RJ-11 and may be set to either RS232 or RS485 via jumper as shown below.
By factory default, the port is set to RS232, termination ON.
Use RS232 to download programs from a PC, and to communicate with serial devices
and applications, such as SCADA.
Use RS485 to create a multi-drop network containing up to 32 devices.
Pinouts
The pinouts below show the PLC port signals.
To connect a PC to a port that is set to RS485, remove the RS485 connector, and connect the PC to
the PLC via the programming cable. Note that this is possible only if flow control signals are not used
(which is the standard case).
RS232
RS485**
Controller
Port
Pin #
Description
Pin #
Description
1* DTR
signal
1 A
signal
(+)
2
0V reference
2
(RS232 signal)
3
TXD signal
3
(RS232 signal)
4
RXD signal
4
(RS232 signal)
5
0V reference
5
(RS232 signal)
6* DSR
signal
6 B
signal
(-)
Pin #1
*Standard programming cables do not provide connection points for pins 1 and 6.
**When a port is adapted to RS485, Pin 1 (DTR) is used for signal A,
and Pin 6 (DSR) signal is used for signal B.