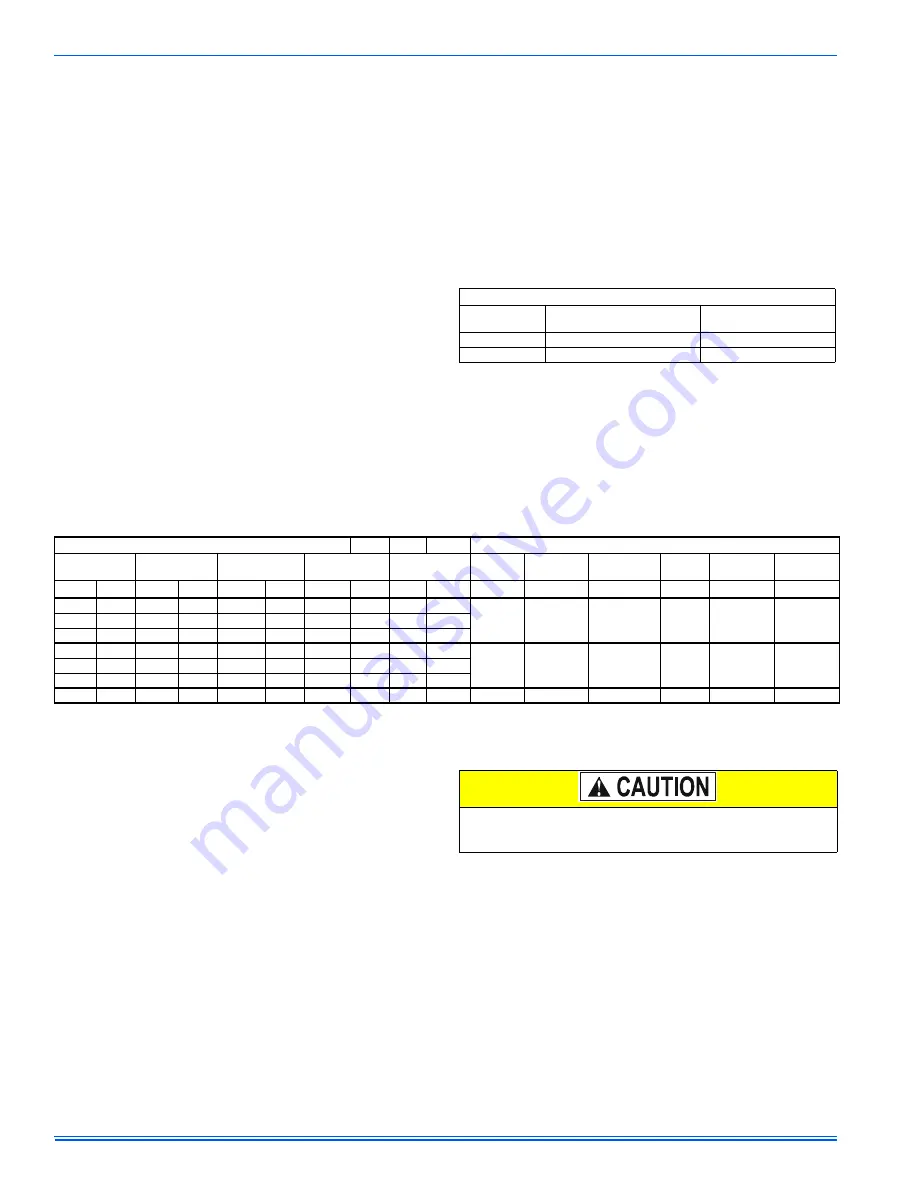
035-19624-001 Rev. A (0104)
10
Unitary Products Group
COMBUSTION AIR/VENT PIPE SIZING
Select the correct size from Table 9. The size will be determined by a
combination of furnace model, total length of run, and the number of
elbows required. The following rules must also be observed.
1.
Long radius (sweep) elbows are required for all units.
2.
Elbows are assumed to be 90 degrees. Two 45-degree elbows
count as one 90-degree elbow.
3.
Elbow count refers to combustion air piping and vent piping sepa-
rately. For example, if the table allows for 5 elbows, this will allow a
maximum of 5 elbows in the combustion air piping and a maximum
of 5 elbows in the vent piping.
4.
For Horizontal Applications the three vent terminal elbows (two for
vent pipe and one for air intake pipe) are already accounted for as
vent termination. Vertical vent applications does not require an
elbow for termination.
5.
Combustion air and vent piping must be of the same diameter.
6.
All combustion air/vent pipe and fittings must conform to American
National Standards Institute (ANSI) standards and American Soci-
ety for Testing and Materials (ASTM) standards D1785 (Schedule
40 PVC), D2665 (PVC-DWV), F891 (PVC-DWV Cellular Core).
D2241 (SDR-21 and SDR-26 PVC), D2261 (ABS-DWV), or F628
(Schedule 40 ABS. Pipe cement and primer must conform to
ASTM Standards D2564 (PVC) or D2235 (ABS).
7.
The use of flexible connectors or no hub connectors in the vent
system is not allowed. This type connection is allowed in the com-
bustion air pipe near the furnace for air conditioning coil accessibil-
ity.
8.
Sidewall horizontal vent terminals and roof mounted vertical termi-
nals may be field fabricated. Standard PVC/SRD fittings may be
used. Terminal configuration must comply as detailed in this sec-
tion.
9.
The minimum vent length is 5 ft. (1.524 m).
The maximum vent length is up to 75 ft. (22.86 m) on same mod-
els. Refer to Table 9 for maximum vent length's.
10. If the Outdoor Combustion Air and vent pipe configuration is
desired, the combustion air pipe and the vent pipe must terminate
together in the same atmospheric zone regardless whether a hori-
zontal (sidewall) or vertical (roof) termination is desired.
*. Vent pipe size must be increased to 3” diameter after connection to furnace on this model.
IMPORTANT:
Accessory concentric vent / intake termination kits
1CT0302 and 1CT0303 are available and approved for use with these
furnaces.
IMPORTANT:
Furnace vent pipe connections are sized for 2-in. pipe.
Any pipe size change must be made outside the furnace casing in a
vertical pipe section to allow proper drainage of condensate. An offset
using two 45º (degree) elbows will be required for plenum clearance
when the vent is increased to 3”.
*. Elbow count does not include the elbows required for the termination. See Step 4 under Combustion Air/Vent Pipe Sizing.
NOTE: If installing furnace at altitudes between 2000 - 4500 ft. (610 – 1372 m), intake and vent pipe length must be reduced by 10 ft. (3.05 m). If the installation requires the maximum allowable
intake and vent pipe length, the furnace must be converted for high altitude operation. Refer to SECTION IV “GAS PIPING” of these instructions and the proper high altitude application
instruction for details.
NOTE:
If installing furnace at altitudes between 2000 - 4500 ft., intake
and vent pipe length must be reduced by 10 ft. If the installation
requires the maximum allowable intake and vent pipe length, the
furnace must be converted for high altitude operation. Refer to
the proper high altitude application instruction for details.
COMBUSTION AIR AND VENT PIPING ASSEMBLY
The final assembly procedure for the combustion air and vent piping is
as follows:
1.
Cut piping to the proper length beginning at the furnace.
2.
Deburr the piping inside and outside.
3.
Chamfer (bevel) the outer edges of the piping.
4.
Dry-fit the vent piping assembly from the furnace to the outside ter-
mination checking for proper fit support and slope.
5.
Dry-fit the combustion air piping assembly checking for proper fit,
support and slope on the following systems:
A.
Sealed combustion air systems from the furnace to the out-
side termination.
B.
Ventilated combustion air systems from the furnace to the
attic or crawl space termination.
6.
Disassemble the combustion air and vent piping, apply cement
primer and the cement per the manufactures instructions. Primer
and cement must conform to ASTM D2564 for PVC, or ASTM
D2235 for ABS piping.
7.
All joints must provide a permanent airtight and watertight seal.
8.
Support the combustion air and vent piping such that it is angled a
minimum of 1/4” per foot (21 mm/m) so that condensate will flow
back towards the furnace. Piping should be supported with pipe
hangers to prevent sagging.
9.
Seal around the openings where the combustion air and / or vent
piping pass through the roof or sidewalls.
COMBUSTION AIR / VENT CLEARANCES
IMPORTANT:
The vent must be installed with the following minimum
clearances, and must comply with local codes and requirements.
TABLE 8:
Combustion Air Intake and Vent Connection Size at Furnace
(All Models)
FURNACE VENT CONNECTION SIZES
Furnace Input
60 - 100 MBH
(17.6-29.3 kW)
120 MBH
(35.17 kW)
Intake Pipe Size
2” (50.8 mm)
3" (76.2 mm)
Vent Pipe Size
2” (50.8 mm)
2"* (50.8 mm)
TABLE 9:
Combustion Air Supply and Vent Piping
MODELS
Max. Elbows vs. One Way Vent Length (Ft.) (m)*
Low Fire
Heating Input
Low Fire
Heating Output
High Fire
Heating Input
High Fire
Heating Output
Furnace
Airflow
Pipe Size
Pipe Size
5 - 40
45
50
75
BTU/H
kW
BTU/H
kW
BTU/H
kW
BTU/H
kW
CFM
m
3
/min
Inches
mm
(1.5 - 12.2 m)
(13.7 m)
(15.2 m)
(22.9 m)
39,000
11.43
36,000
10.55
60,000
17.58
55,000
16.12
1200
33.98
2
50.8
6
5
4
N/A
52,000
15.24
48,000
14.07
80,000
23.45
75,000
21.98
1600
45.31
65,000
19.05
60,000
17.58
100,000
29.31
95,000
27.84
2000
56.63
39,000
11.43
36,000
10.55
60,000
17.58
55,000
16.12
1200
33.98
3
76.2
8
7
6
5
52,000
15.24
48,000
14.07
80,000
23.45
75,000
21.98
1600
45.31
65,000
19.05
60,000
17.58
100,000
29.31
95,000
27.84
2000
56.63
78,000
22.86
72,000
21.10
120,000
22.86
112,000
32.82
2000
56.63
3" only
76 mm only
6
5
4
N/A
Solvent cements are flammable and must be used in well-ventilated
areas only. Keep them away from heat, sparks and open flames.
Do not breathe vapors and avoid contact with skin and eyes.