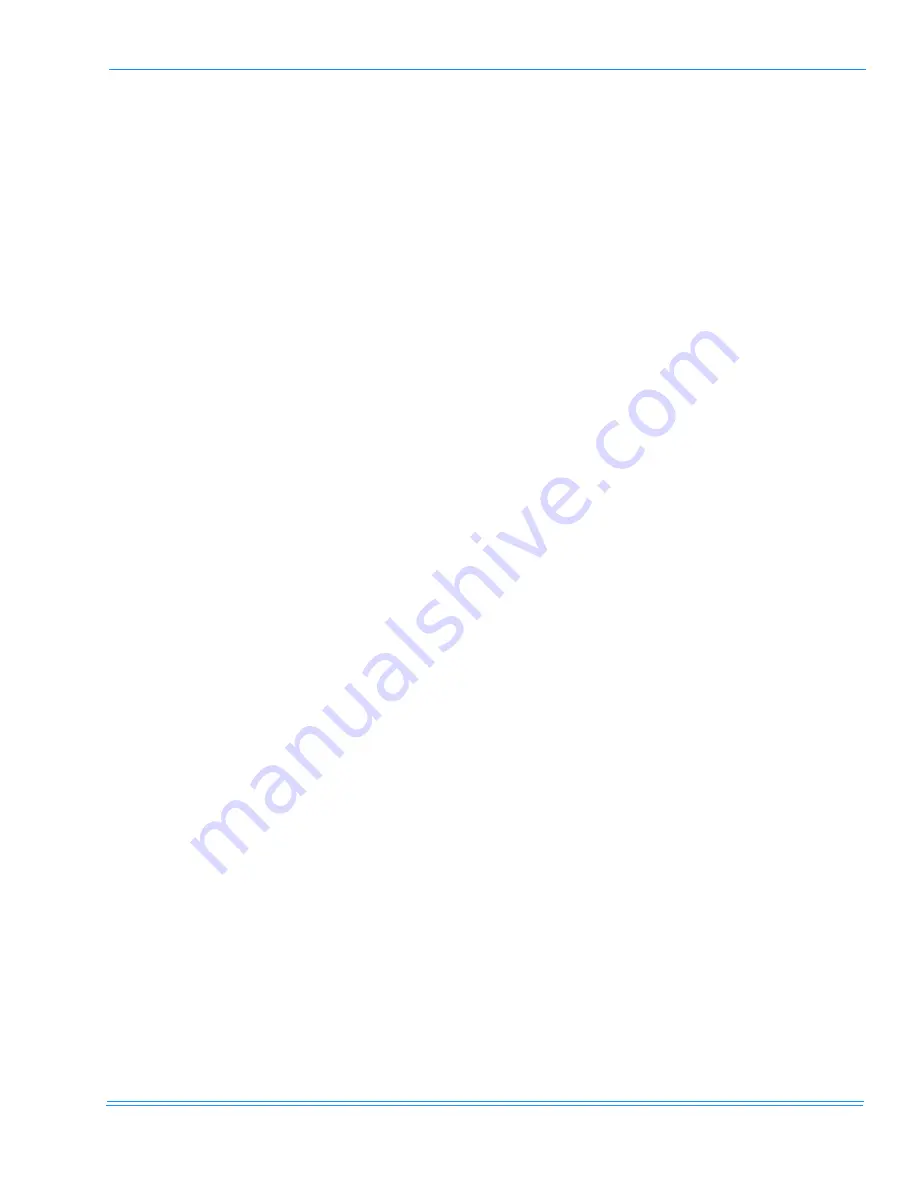
66399-YIM-C-0405
Unitary Products Group
75
of gas. Inspect the orifice for obstruction. If it is
clear, replace the main gas valve.
The ignitor sparks at the pilot burner but the pilot does
not ignite and a gas odor is detected at the draft motor
outlet.
1.
Adjust the pilot adjust screw on the gas valve as
described in “PILOT CHECKOUT” on page 69.
2.
Check the supply pressure as described in “POST
START CHECK LIST” on page 68. Make adjust-
ments as necessary.
3.
Check the pilot orifice and carryover tube for
obstruction as described in paragraph above.
Clean as needed but the problem should not be the
gas valve.
The pilot burner ignites but the ignitor continues to
spark and the main burners do not ignite.
1.
Make the same checks and adjustment as
described in “PILOT CHECKOUT” on page 69.
2.
Check the supply pressure as described in “POST
START CHECK LIST” on page 68. Make adjust-
ments as necessary.
3.
Make sure that the pilot burner is not bent or dam-
aged.
4.
Make sure that the ground connections at the pilot
burner, gas valve and ignitor control are intact.
Check the ignitor wire for good electrical connec-
tion. If all are intact, replace the ignitor module.
The pilot burner lights and the spark stops but the main
burners do not light.
1.
Check electrical connections between the ignitor
control and the gas valve. If intact, check for 24
volts across terminals “MV” and “GROUND” termi-
nals. If no voltage detected, replace ignitor control.
If voltage is present, replace gas valve.
Furnace lights with roll-out or one burner has delayed
ignition.
1.
Make sure that the carryover is aligned properly
with the flame sensor as described in “PILOT
CHECKOUT” on page 69.
Main burners light but exhibit erratic flame characteris-
tics.
1.
Adjust air shutters as described in “BURNER AIR
SHUTTER ADJUSTMENT” on page 69.
2.
Check the main burner orifices for obstruction and
alignment. Removal procedure is described in
BURNER INSTRUCTIONS on page 69. Clean or
replace burner orifices and burners as needed.
UNIT FLASH CODES
Various flash codes are utilized by the unit control
board (UCB) to aid in troubleshooting. Flash codes are
distinguished by the short on and off cycle used
(approximately 200ms on and 200ms off). To show
normal operation, the control board flashes a 1 second
on, 1 second off “heartbeat” during normal operation.
This is to verify that the UCB is functioning correctly.
Do not confuse this with an error flash code. To prevent
confusion, a 1-flash, flash code is not used.
Current alarms or active restrictions are flashed on the
UCB LED. Pressing and releasing the ALARMS button
on the UCB can check the alarm history. The UCB will
cycle through the last five (5) alarms, most recent to
oldest, separating each alarm flash code by approxi-
mately 2 seconds.
In some cases, it may be necessary to “zero” the
ASCD for the compressors in order to perform trouble-
shooting. To reset all ASCDs for one cycle, press and
release the UCB TEST button once.