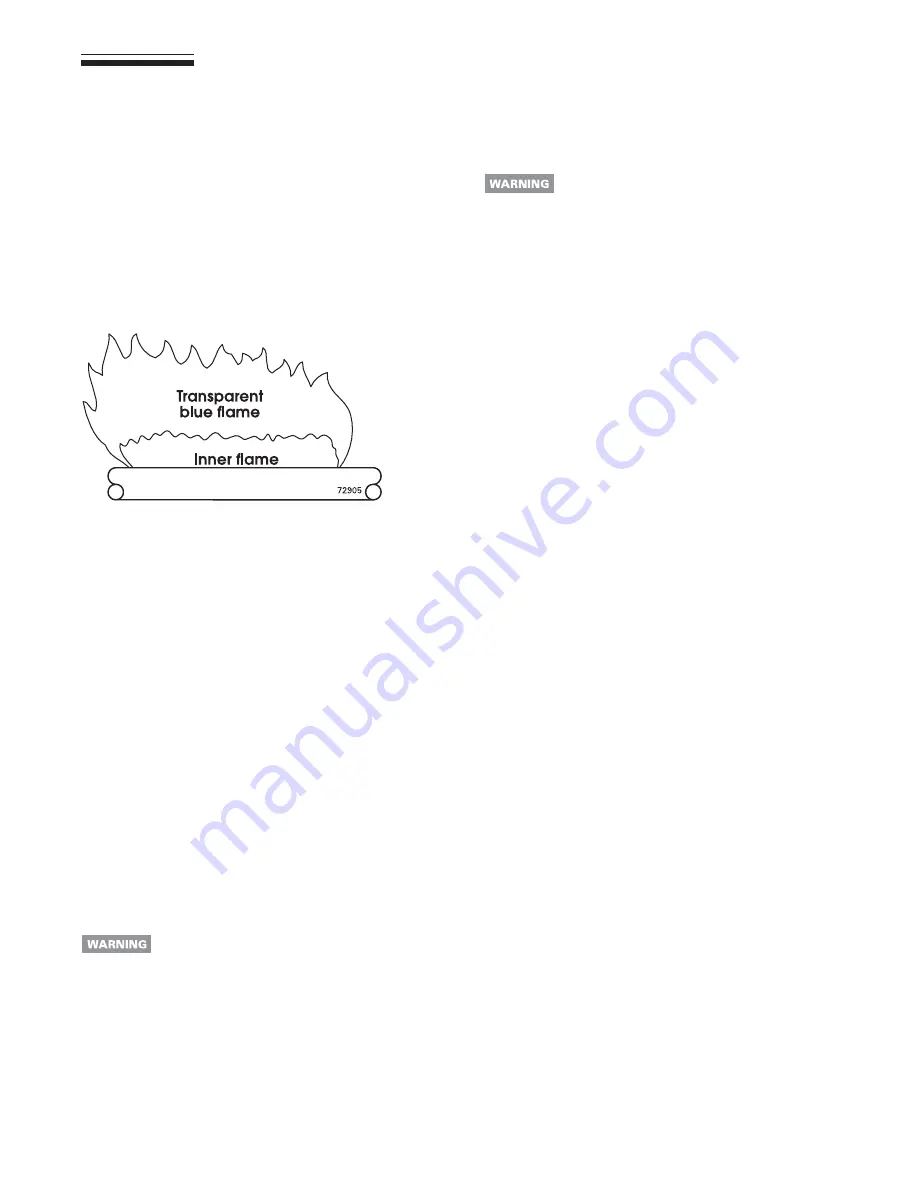
11
Part Number 550-110-726/0703
GWA/GWI/GWS
Gas-Fired Water Boilers –
User’s Information Manual
❏
Periodically
Operate boiler relief
To avoid water damage or scalding due to valve
operation, a metal discharge line must be connected
to relief valve outlet and run to a safe place of dis-
posal. This discharge line must be installed by a
qualified heating installer or service technician in
accordance with the instructions in the Boiler
Manual. The discharge line must be terminated so
as to eliminate possibility of severe burns should
the valve discharge.
1. Before proceeding, verify that the relief valve outlet has been
piped to a safe place of discharge, avoiding any possibility of
scalding from hot water.
2. Read the boiler pressure/temperature gauge to make sure
the system is pressurized.
3. Lift the relief valve top lever slightly, allowing water to relieve
through the valve and discharge piping.
4. If water flows freely, release the lever and allow the valve to
seat. Watch the end of the relief valve discharge pipe to ensure
that the valve does not weep after the line has had time to
drain. If the valve weeps, lift the seat again to attempt to clean
the valve seat. If the valve continues to weep afterwards,
contact your qualified service technician to inspect the valve
and system.
5. If water does not flow from the valve when you lift the lever
completely, the valve or discharge line may be blocked.
Immediately shutdown the boiler, following the instructions
on the inside jacket top "Lighting Instructions". Call your
qualified service technician to inspect the boiler and system.
Test low water cutoff (if installed)
1. If the boiler or system is fitted with a low water cutoff device,
test the device following the cutoff manufacturer’s instructions.
Oil inducer motor (GWI and GWS boilers)
1. Use only S.A.E. 20 motor oil. DO NOT use household
universal oils.
Use only S.A.E. 20 motor oil to lubricate the inducer
motor. Do not use common universal household oils.
2. Place a few drops of oil in each of the two oiler cups on the
inducer motor.
Clean vent termination & air intake screens —
GWS boilers only
1. Remove all lint and debris from both the boiler air intake screen
and the flue discharge screen.
The boiler control module will sense blockage of the air intake
or flue and lockout if the blockage is excessive. It will signal
the failure by flashing the appropriate indicator lights on the
control board.
2. If removing the debris does not allow the boiler to operate
correctly afterwards, contact your qualified service technician
to inspect the boiler and vent/air systems.
Main burner flame
Proper main burner flame (see below):
1. Yellow-orange streaks may appear (caused by dust).
Improper main burner flame:
1. Overfired — Large flames.
2. Underfired — Small flames.
3. Lack of primary air — Yellow tipping on flames (sooting will
occur).
❏
Check monthly
❏
Every 6 months
1. Follow “TO TURN OFF GAS TO APPLIANCE” on the
"Lighting
or Operating Instructions"
on the inside of the jacket panel.
You will also find these instructions on pages 4 through 8 of
this manual.
Use the "Lighting or Operating Instructions" for the gas valve
model installed on the boiler.
2. Do not drain system unless exposure to freezing temperatures
will occur.
3. Do not drain the system if it is filled with an antifreeze solution.
4. Do not shut down boilers used for domestic water heating.
They must operate year-round.
❏
End of season shutdown
1. See page 12.
❏
Troubleshooting