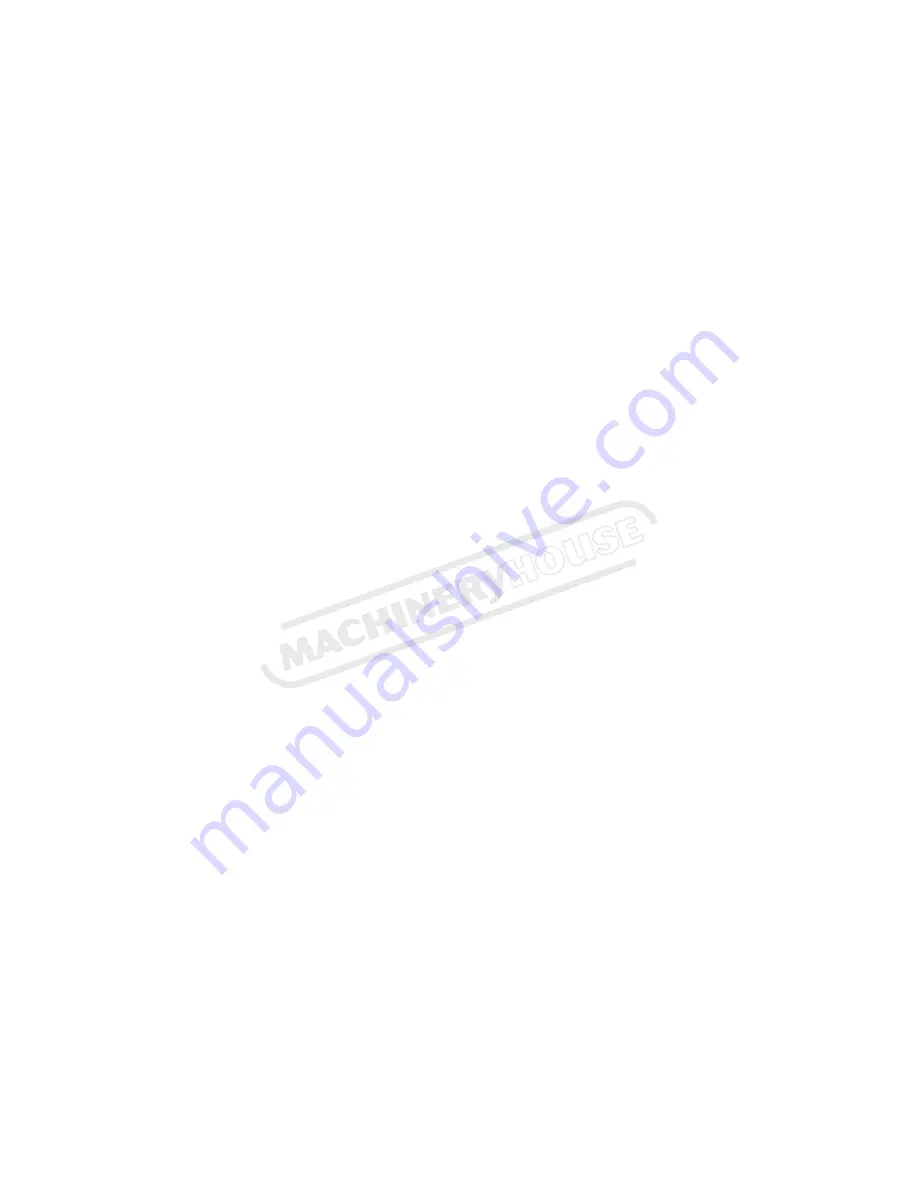
• Latest IGBT Inverter Technology
• Mig/Mag Function
• MMA (Stick electrode) (DC+ / DC-) function
• Stepless Voltage & Wire Feed Controls at Wire Feeder
• Variable Inductance & Burn Back Controls
• Adjustable Crater Current Control
• Gas Purge / Inch Wire • 2T/4T Trigger Function
• Separate Wire Feeder with geared 4 roller drive
• LED Volt/AMP Meter Digital Display
• Scratch start DC TIG welding
• 10m Interconnecting Cables
• Trolley with pull out tool storageMIG250/350/500SWF
MACHINE FEATURES
Page 4
Instruction Manual for MIG-TIG-MMA-500SWF (L591)
16/12/2014