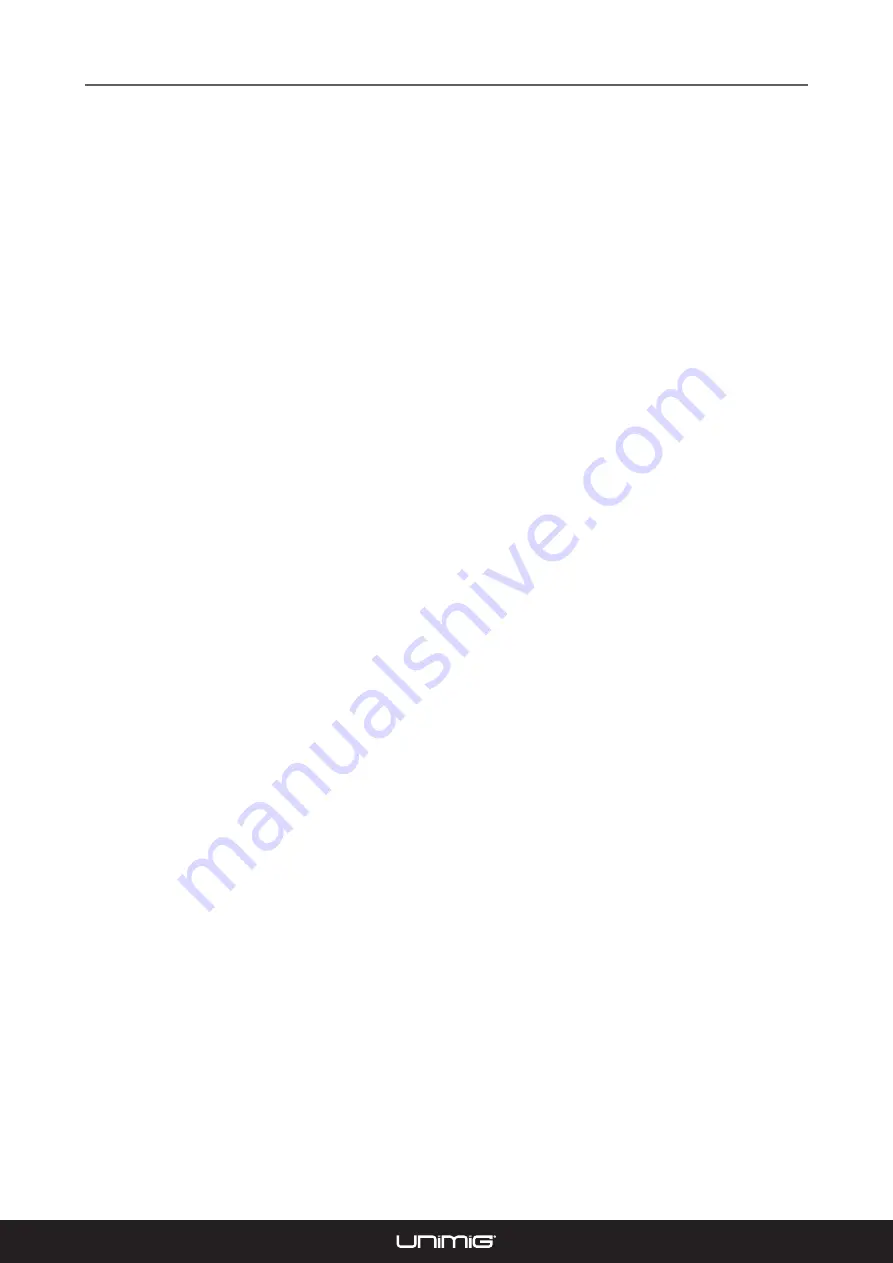
CAUTION
1. Working Environment.
i.
The environment in which this welding/cutting equipment is installed must be free of grinding dust,
corrosive chemicals, flammable gas or materials etc., and at no more than a maximum of 80% humidity.
ii.
When using the machine outdoors, protect the machine from direct sunlight, rainwater and snow, etc.;
the temperature of the working environment should be maintained within -10°C to +40°C.
iii.
Keep this equipment 30cm distant from the wall.
iv.
Ensure the working environment is well ventilated.
2. Safety Tips.
i. Ventilation:
This equipment is small-sized, compact in structure, and of excellent performance in
amperage output. The fan is used to dissipate heat generated by this equipment during the welding/
cutting operation. Important: Maintain good ventilation of the louvres of this equipment. The minimum
distance between this equipment and any other objects in or near the working area should be 30 cm.
Good ventilation is of critical importance for the normal performance and service life of this equipment.
ii. Thermal Overload Protection:
Should the machine be used to an excessive level, or in a high-
temperature environment, poorly ventilated area or if the fan malfunctions the Thermal Overload Switch
will be activated, and the machine will cease to operate. Under this circumstance, leave the machine
switched on to keep the built-in fan working to bring down the temperature inside the equipment. The
machine will be ready for use again when the internal temperature reaches a safe level.
iii. Over-Voltage Supply:
Regarding the power supply voltage range of the machine, please refer to the
“Main parameter” table. This equipment is of automatic voltage compensation, which enables the
maintaining of the voltage range within the given range. In case that the voltage of input power supply
amperage exceeds the stipulated value, it is possible to cause damage to the components of this
equipment. Please ensure your primary power supply is correct.
iv.
Do not come into contact with the output terminals while the machine is in operation. An electric shock
may occur.
MAINTENANCE
Exposure to extremely dusty, damp, or corrosive air is damaging to the welding/cutting machine. To prevent
any possible failure or fault of this welding/cutting equipment, clean the dust at regular intervals with clean
and dry compressed air of required pressure.
Please note that:
lack of maintenance can result in the cancellation of the guarantee; the guarantee of this
welding/cutting equipment will be void if the machine has been modified, attempt to take apart the machine
or open the factory-made sealing of the machine without the consent of an authorized representative of the
manufacturer.
TROUBLESHOOTING
Caution:
Only qualified technicians are authorized to undertake the repair of this welding/cutting equipment.
For your safety and to avoid Electrical Shock, please observe all safety notes and precautions detailed in
this manual.
SAFETY
6
Содержание RAZOR CUT 40 AIR
Страница 1: ...RAZOR CUT 40 AIR U14001K Operating Manual...
Страница 2: ...2...
Страница 25: ...NOTES 25...
Страница 26: ...NOTES 26...
Страница 27: ...NOTES 27...