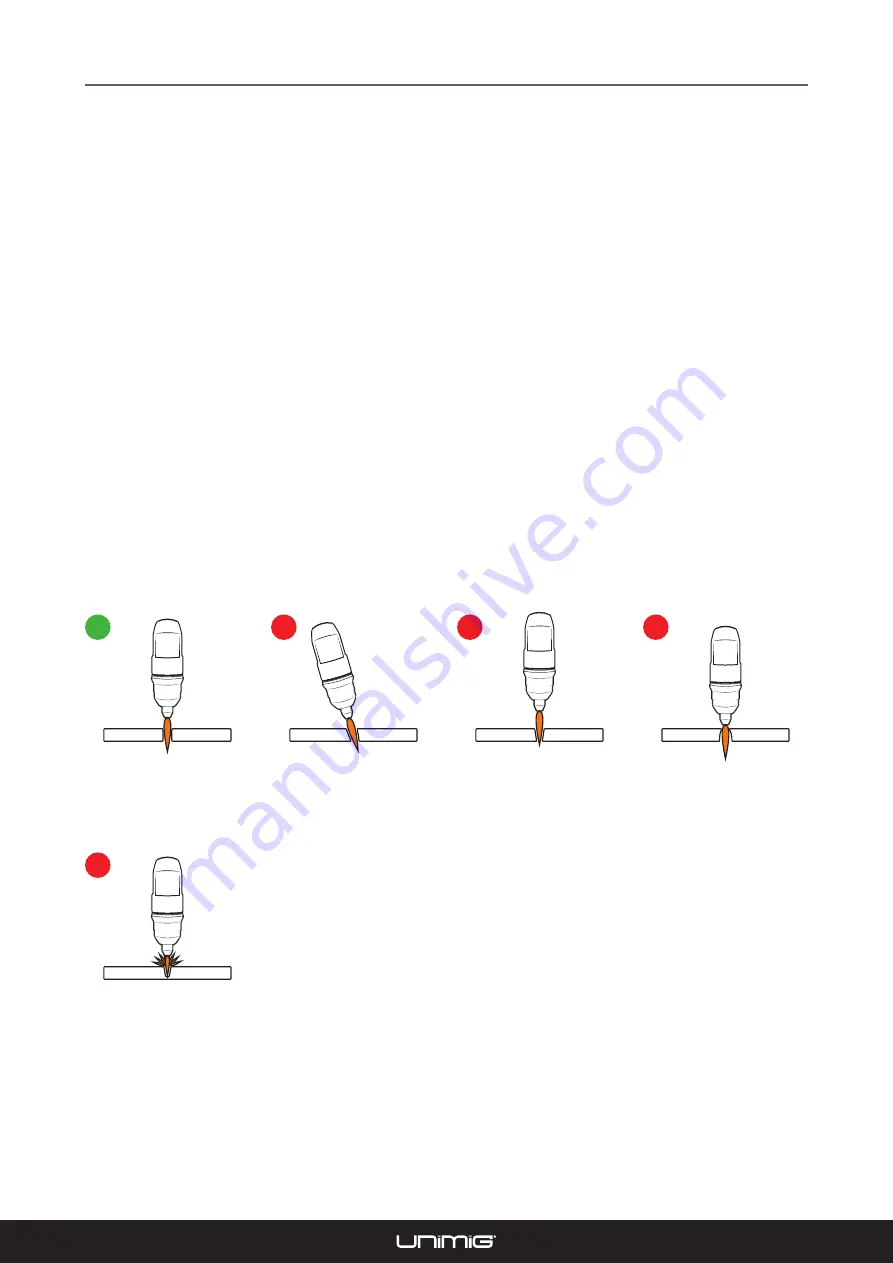
check
times
times
times
times
Amperage
The standard rule of thumb is the thicker the material, the more amperage required. On thick material, set the
machine to full output and vary your travel speed. On thinner material, you need to turn down the amperage
and change to a lower-amperage tip to maintain a narrow kerf. The kerf is the width of the cut material that is
removed during cutting.
Speed
Amperage and speed are critical to producing a good quality cut. The faster you move (especially on
aluminium), the cleaner your cut will be. To determine if you’re going too fast or too slow, visually follow
the arc that is coming from the bottom of the cut. The arc should exit the material at a slight angle away
from the direction of travel. If it’s going straight down, that means you’re going too slow, and you’ll have an
unnecessary build-up of dross or slag. If you go too fast, it will start spraying back onto the surface of the
material without cutting all the way through. Because the arc trails at an angle, at the end of a cut, slow your
cutting speed and angle the torch in to cut through the last bit of metal.
Direction
It is easier to pull the torch towards you than push it. The plasma stream swirls as it exits the tip, biting one
side and finishing off on the other, leaving a bevelled edge and a straight edge. The bevel cut effect is more
noticeable on thicker material and needs to be taken into consideration before starting your cut as you want
the straight side of the cut to be on the finished piece you keep.
Torch tip height & position
The distance and position of the plasma torch cutting tip affect the quality of the cut and the extent of the
bevel of the cut. The easiest way to reduce bevel is by cutting at the proper speed and height for the material
and amperage that is being cut.
Tip size and condition
The tip orifices focus the plasma stream to the workpiece. It is essential to use the correct size tip for the
amperage being used, for example, a tip with a 1.0mm orifice is suitable for 0-40 amps whereas a 1.3mm
orifice is better for 40-80 amps. The low-amp tip has a smaller orifice which maintains a narrow plasma stream
at lower settings for use on thin-gauge material. Using a 25 amp tip at a 60 amp setting will blow out and
distort the tip orifice and require replacement. Conversely, using an 80-amp tip on the lower settings will not
allow you to focus the plasma stream as well and creates a wide kerf. The condition of the tip orifice is critical
to the quality of the cut result, a worn or damaged tip orifice will produce a distorted plasma stream resulting
in poor cut quality.
Correct torch height and
square to the material.
Minimum bevel & equal bevel
Longest consumable life.
If sparks are spraying up from
the work piece, you are moving
the torch too fast, or you don’t
have enough amps set.
Torch angled to the material.
Unequal bevel, one side may
be excessively bevelled.
Torch height too high.
Excessive bevel, plasma
stream may not cut all the way
through the material.
Torch height too low. Reverse
bevel. The tip may contact the
work and short out or damage
the tip.
PLASMA CUTTING TIPS & TECHNIQUES
20
Содержание RAZOR CUT 40 AIR
Страница 1: ...RAZOR CUT 40 AIR U14001K Operating Manual...
Страница 2: ...2...
Страница 25: ...NOTES 25...
Страница 26: ...NOTES 26...
Страница 27: ...NOTES 27...