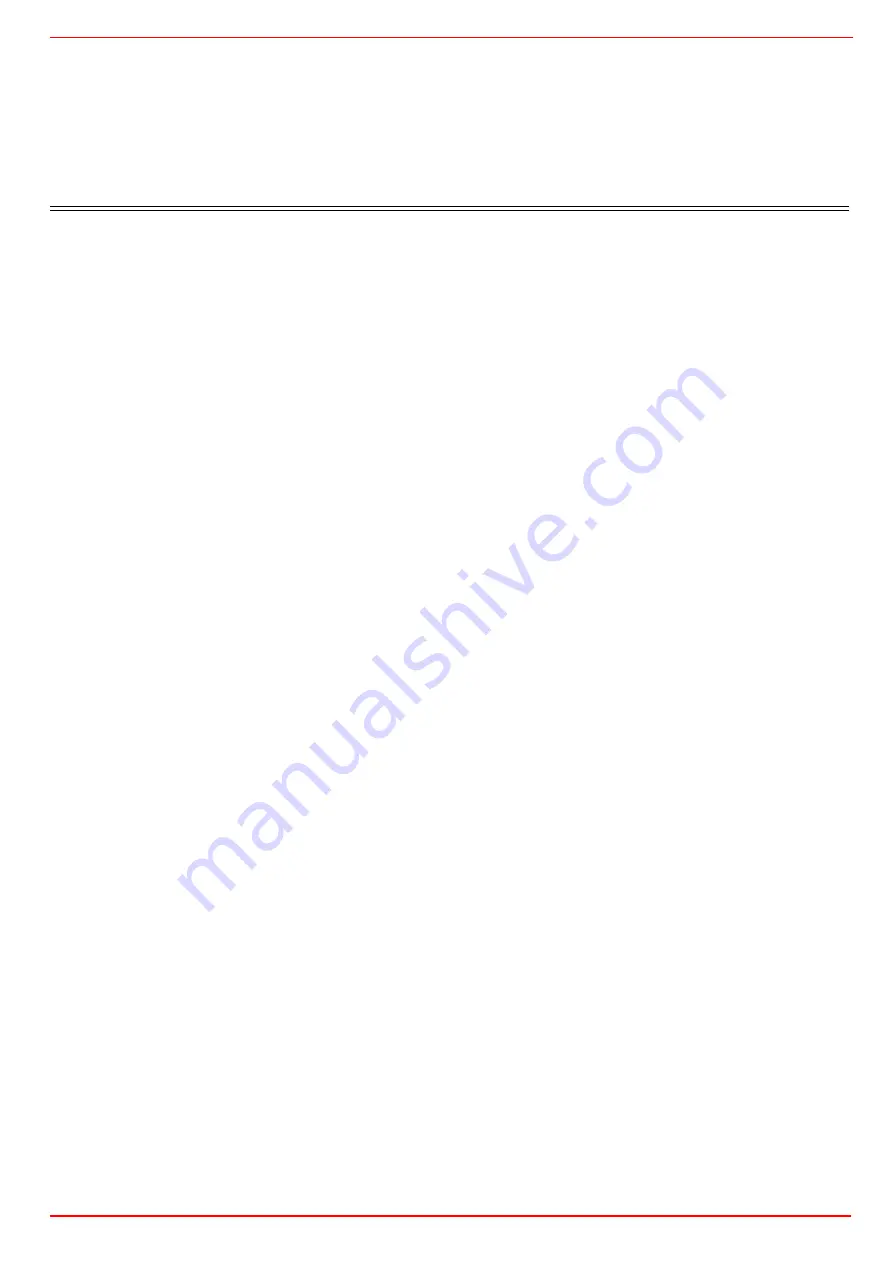
2
DANGERS, WARNINGS AND NOTES OF CAUTION
THIS MANUAL IS SUPPLIED AS AN INTEGRAL AND ESSENTIAL PART OF THE PRODUCT AND MUST BE DELIVERED TO THE
USER.
INFORMATION INCLUDED IN THIS SECTION ARE DEDICATED BOTH TO THE USER AND TO PERSONNEL FOLLOWING
PRODUCT INSTALLATION AND MAINTENANCE.
THE USER WILL FIND FURTHER INFORMATION ABOUT OPERATING AND USE RESTRICTIONS, IN THE SECOND SECTION
OF THIS MANUAL. WE HIGHLY RECOMMEND TO READ IT.
CAREFULLY KEEP THIS MANUAL FOR FUTURE REFERENCE.
1) GENERAL INTRODUCTION
The equipment must be installed in compliance with the regulations in
force, following the manufacturer’s instructions, by qualified personnel.
Qualified personnel means those having technical knowledge in the
field of components for civil or industrial heating systems, sanitary hot
water generation and particularly service centres authorised by the
manufacturer.
Improper installation may cause injury to people and animals, or
damage to property, for which the manufacturer cannot be held liable.
Remove all packaging material and inspect the equipment for integrity.
In case of any doubt, do not use the unit - contact the supplier.
The packaging materials (wooden crate, nails, fastening devices, plastic
bags, foamed polystyrene, etc), should not be left within the reach of chil-
dren, as they may prove harmful.
Before any cleaning or servicing operation, disconnect the unit from
the mains by turning the master switch OFF, and/or through the cut-
out devices that are provided.
Make sure that inlet or exhaust grilles are unobstructed.
In case of breakdown and/or defective unit operation, disconnect the
unit. Make no attempt to repair the unit or take any direct action.
Contact qualified personnel only.
Units shall be repaired exclusively by a servicing centre, duly authorised
by the manufacturer, with original spare parts and accessories.
Failure to comply with the above instructions is likely to impair the unit’s
safety.
To ensure equipment efficiency and proper operation, it is essential that
maintenance operations are performed by qualified personnel at regular
intervals, following the manufacturer’s instructions.
When a decision is made to discontinue the use of the equipment,
those parts likely to constitute sources of danger shall be made harm-
less.
In case the equipment is to be sold or transferred to another user, or in
case the original user should move and leave the unit behind, make
sure that these instructions accompany the equipment at all times so
that they can be consulted by the new owner and/or the installer.
This unit shall be employed exclusively for the use for which it is
meant. Any other use shall be considered as improper and, therefore,
dangerous.
The manufacturer shall not be held liable, by agreement or otherwise, for
damages resulting from improper installation, use and failure to comply
with the instructions supplied by the manufacturer.The occurrence of any
of the following circustances may cause explosions, polluting unburnt
gases (example: carbon monoxide CO), burns, serious harm to people,
animals and things:
- Failure to comply with one of the WARNINGS in this chapter
- Incorrect handling, installation, adjustment or maintenance of the burner
- Incorrect use of the burner or incorrect use of its parts or optional supply
2) SPECIAL INSTRUCTIONS FOR BURNERS
The burner should be installed in a suitable room, with ventilation ope-
nings complying with the requirements of the regulations in force, and
sufficient for good combustion.
Only burners designed according to the regulations in force should be
used.
This burner should be employed exclusively for the use for which it
was designed.
Before connecting the burner, make sure that the unit rating is the
same as delivery mains (electricity, gas oil, or other fuel).
Observe caution with hot burner components. These are, usually, near
to the flame and the fuel pre-heating system, they become hot during
the unit operation and will remain hot for some time after the burner
has stopped.
When the decision is made to discontinue the use of the burner, the user
shall have qualified personnel carry out the following operations:
a Remove the power supply by disconnecting the power cord from the
mains.
b Disconnect the fuel supply by means of the hand-operated shut-off
valve and remove the control handwheels from their spindles.
Special warnings
Make sure that the burner has, on installation, been firmly secured to
the appliance, so that the flame is generated inside the appliance fire-
box.
Before the burner is started and, thereafter, at least once a year, have
qualified personnel perform the following operations:
a set the burner fuel flow rate depending on the heat input of the
appliance;
b set the flow rate of the combustion-supporting air to obtain a combu-
stion efficiency level at least equal to the lower level required by the
regulations in force;
c check the unit operation for proper combustion, to avoid any harmful or
polluting unburnt gases in excess of the limits permitted by the regula-
tions in force;
d make sure that control and safety devices are operating properly;
e make sure that exhaust ducts intended to discharge the products of
combustion are operating properly;
f
on completion of setting and adjustment operations, make sure that all
mechanical locking devices of controls have been duly tightened;
g make sure that a copy of the burner use and maintenance instructions
is available in the boiler room.
In case of a burner shut-down, reser the control box by means of the
RESET pushbutton. If a second shut-down takes place, call the Tech-
nical Service,
without trying to RESET further
.
The unit shall be operated and serviced by qualified personnel only, in
compliance with the regulations in force.
3) GENERAL INSTRUCTIONS DEPENDING ON FUEL USED
3a) ELECTRICAL CONNECTION
For safety reasons the unit must be efficiently earthed and installed as
required by current safety regulations.
It is vital that all saftey requirements are met. In case of any doubt, ask
for an accurate inspection of electrics by qualified personnel, since the
manufacturer cannot be held liable for damages that may be caused
by failure to correctly earth the equipment.
Qualified personnel must inspect the system to make sure that it is
adequate to take the maximum power used by the equipment shown
on the equipment rating plate. In particular, make sure that the system
cable cross section is adequate for the power absorbed by the unit.
No adaptors, multiple outlet sockets and/or extension cables are per-
mitted to connect the unit to the electric mains.
An omnipolar switch shall be provided for connection to mains, as
required by the current safety regulations.
The use of any power-operated component implies observance of a
few basic rules, for example:
-
do not touch the unit with wet or damp parts of the body and/or with
bare feet;
-
do not pull electric cables;
-
do not leave the equipment exposed to weather (rain, sun, etc.)
unless expressly required to do so;
-
do not allow children or inexperienced persons to use equipment;
The unit input cable shall not be replaced by the user.
In case of damage to the cable, switch off the unit and contact quali-
fied personnel to replace.
When the unit is out of use for some time the electric switch supplying
all the power-driven components in the system (i.e. pumps, burner,
etc.) should be switched off.
Содержание TP90A-TP91A
Страница 39: ...PART III MAINTENANCE 39...
Страница 41: ...LME73 000Ax PME73 831AxBC LME73 831AxBC Service instruction manual M12921CB Rel 1 2 02 2016...
Страница 63: ...23...
Страница 64: ...Note Specifications and data subject to change Errors and omissions excepted...