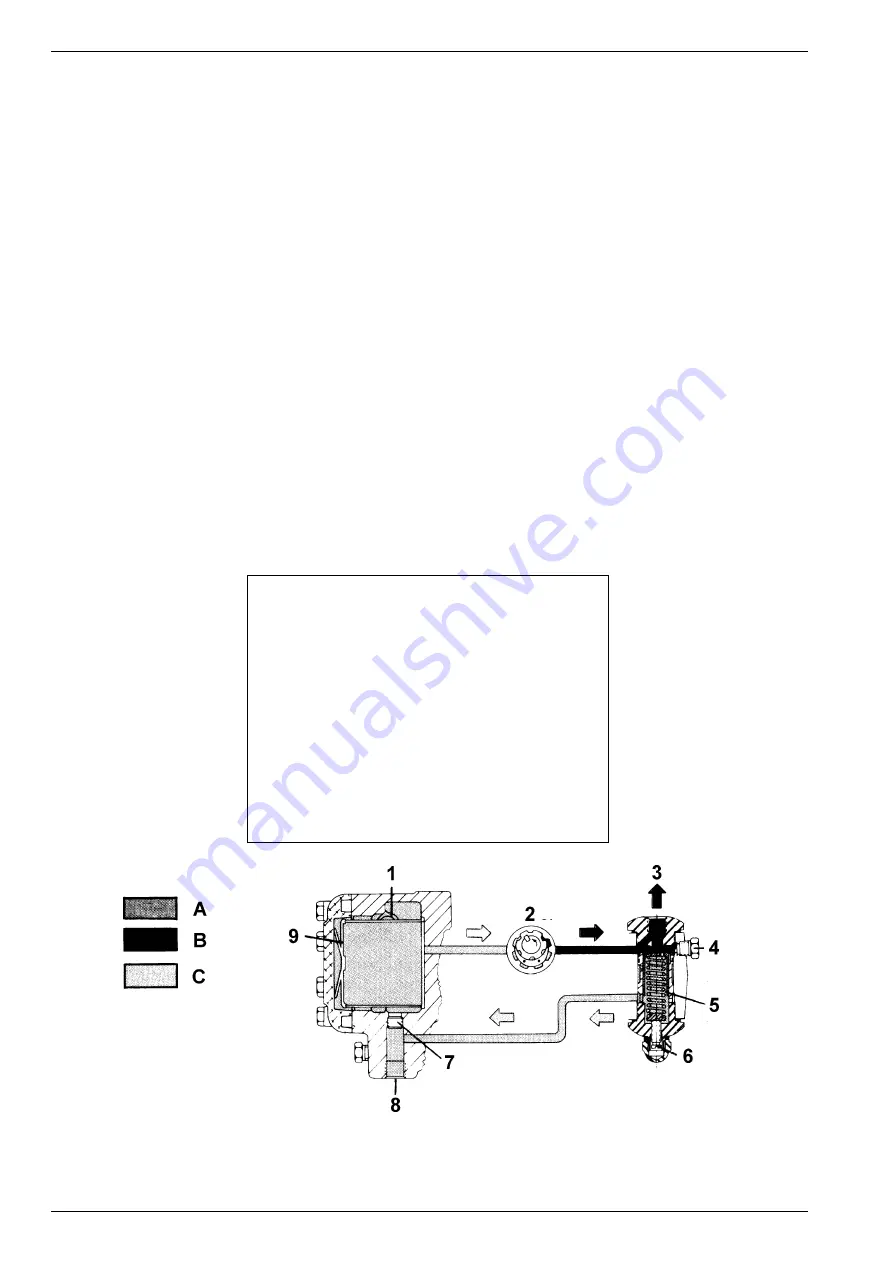
HEAVY OIL PUMP SUNTEC E4NC
The “Suntec E Serie” pump, is fitted with a pressure regulation
valve with cut-off function.
This pump is suitable for the use with high-densiti oils.
Operation
The gear set sucks heavy oil from from the tank, through the
filter and drive it under pressure to the valve, which regulates
the pressure in the nozzle line.
The oil in excess that doesn’t flow through the nozzle line is
drained, through the valve, to the return pipe or to the tank or,
in the single pipe installation, to the gear set input in the
suction-side.
The regulation valve has also a cut-off function as follows.
The drain function is obtained by means of a groove in the
piston. During the time of start-up, when the speed increases,
the oil flows completely through the groove and drains on the
return. The valve is closed until the motor resches such speed
in which the quantity of oil feeded by the gear set is higher then
the one that can flow trhough the drain groove of the piston.
The pressure into the valve increases rapidly until it
overcomes the opposition of the spring and tha valve opens.
During the stopping phase, the gear set speed decreases and
the valve shuts-off when the flow rate of the gear set is lower
than the flow rate in the drain groove. The shut-off speed and
the opening speed depend by the gear set dimensions and by
the pressure choosen.
TECHNICAL DATA
Mounting on flange (DIN 24220)
Rounded-headed in accordance with ISO R228, NFE 03005
- DIN 259
Supply and return
G 1/2”
Delivery to tthe nozzle
G 1/4”
Pressurepoint
G 1/8”
Vacuum point
G 1/2”
Valve function
pressure regulation and cut-off
Filter surface
45 cm
2
, N= 550μ, C= 170μ
Shaft
11mm according with DIN 24220
By-pass plug
inserted for twin pipe installation;
remove in case of single pipe operation
Weight
4 Kg
Rotation and delivery position, wiewing from shaft side
A - clockwise / right
B - clockwise / left
C - counterclockwise / left
D - counterclockwise / right
Pressure range
14 to 30 bar to the nozzle, adjusted at
the factory to 20 bar
Viscosity range
from 2,8 to 800 cSt
Key
1
Input from tank
2
Gear set
3
To nozzle
4
Pressure point
5
Pressure regulation valve
6
Regulation screw
7
By-pass plug
8
Return
9
Filter
A
Oil under suction
B
Oil under pressure
C
By-passed oil returned to tank or to suction
APPENDIX
Содержание N18
Страница 12: ......
Страница 13: ...Z Z Z _ _ Z Z Z _...
Страница 14: ......
Страница 15: ..._ Z Z Z _ _ Z Z Z _...
Страница 23: ......
Страница 24: ......