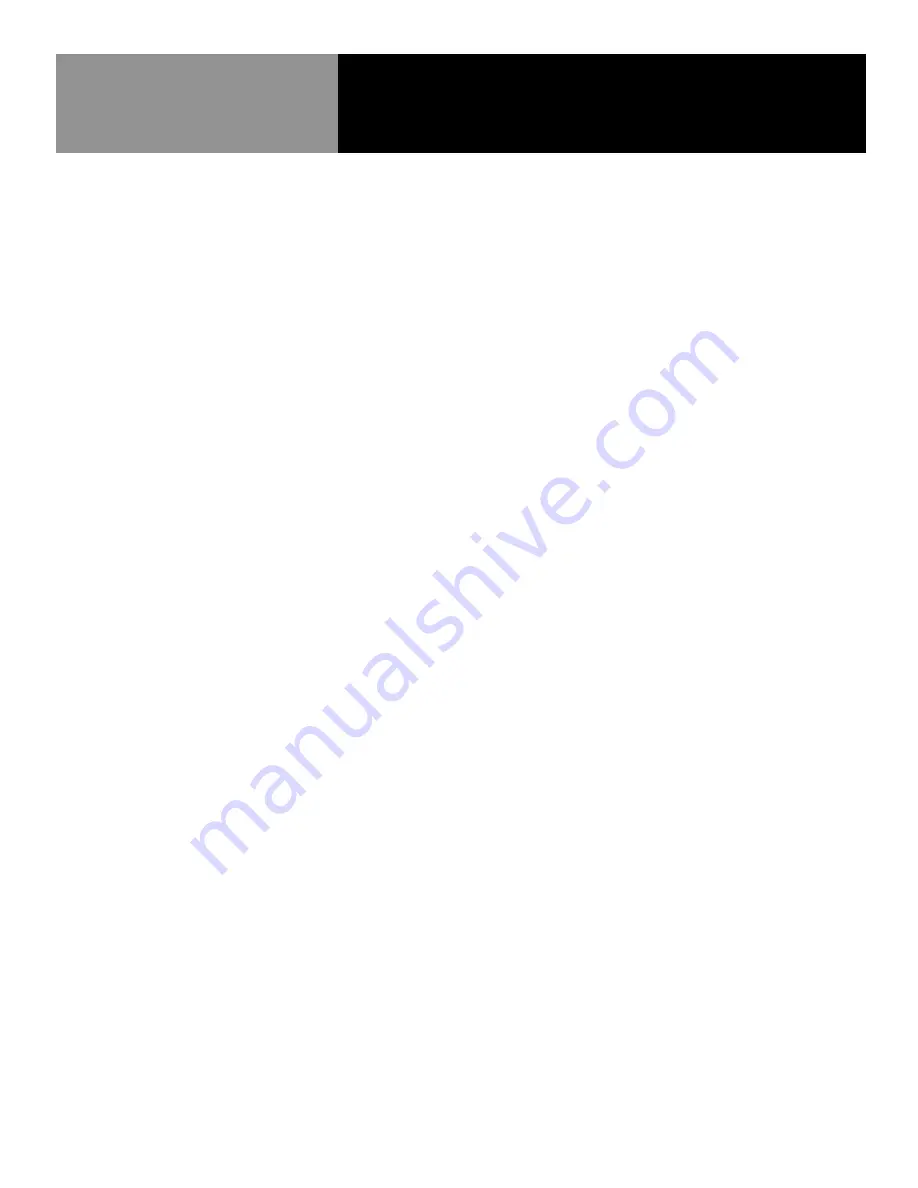
OM-DEEP WELL REFRIGERATOR SERIES 17
Congratulations on your purchase of a Unified Brands Brand piece of equipment. Unified Brands believes strongly in the products it
builds and backs them with the best warranty in the industry. Standard with every unit is the peace of mind that this unit has been
thoroughly engineered, properly tested and manufactured to excruciating tolerances, by a manufacturer with over 30 years of industry
presence. On top of that front end commitment, Unified Brands has a dedicated staff of certified technicians that monitor our own
technical service hotline at
1-888-994-7636
to assist you with any questions or concerns that may arise after delivery of your new
Unified Brands equipment.
PARTS WARRANTY
1. One year parts replacement of any and all parts that are found defective in material or workmanship. Unified Brands warrants all
component parts of manufactured new equipment to be free of defects in material or workmanship, and that the equipment meets
or exceeds reasonable industry standards of performance for a period of one year from the date of shipment from any Unified
Brands factory, assembly plant or warehouse facility.
NOTE
: warranties are effective from date of shipment, with a thirty day window to allow for shipment, installation and set-up. In
the event equipment was shipped to a site other than the final installation site, Unified Brands will warranty for a period of three
months following installation, with proof of starting date, up to a maximum of fifteen months from the date of purchase.
2. Free ground freight of customer specified location for all in warranty parts within continental U.S. Component part warranty does
not cover glass breakage or gasket replacement. Unified Brands covers all shipping cost related to component part warranty sent
at regular ground rates (UPS, USPS).
Freight or postage incurred for any express or specialty methods of shipping are the
responsibility of the customer.
LABOR COVERAGE
In the unlikely event a Unified Brands manufactured unit fails due to defects in materials or workmanship within the first ninety days,
Unified Brands agrees to pay the contracted labor rate performed by an Authorized Service Agent (ASA). Any work performed by a
non-ASA will not be honored by Unified Brands. Please consult Unified Brands Technical Support (888-994-7636) for a complete listing
of ASAs or visit the service page of our website: www.unifiedbrands.net. Warranties are effective from date of shipment, with a thirty
day window to allow for shipment, installation and setup. Where equipment is shipped to any site other than final installation, Unified
Brands will honor the labor warranty for a period of ninety days following installation with proof of starting date, up to a maximum of
six months from date of purchase.
Temperature adjustments are not covered under warranty, due to the wide range of ambient conditions.
To request a warranty approval number, call our Field Service Department at: 1-888-994-7636
WHEN OPTIONAL 5 YEAR COMPRESSOR WARRANTY APPLIES
1. Provide reimbursement to an ASA for the cost of locally obtained replacement compressor in exchange for the return of the defective
compressor sent back freight prepaid. NOTE: Unified Brands does limit amount of reimbursement allowed and does require bill
from local supply house where compressor was obtained (customer should not pay servicing agent up front for compressor).
2. Provide repair at the manufacturing facility by requiring that the defective unit be sent back to Unified Brands freight prepaid.
Perform repair at the expense of Unified Brands and ship the item back to the customer freight collect.
3. Furnish a replacement compressor freight collect in exchange for the return of the defective compressor sent back freight prepaid.
4. Furnish complete condensing unit freight collect in exchange for the return of the defective condensing unit sent back freight
prepaid. (Decisions on whether or not to send complete condensing units will be made by Unified Brands in-house service
technician).
Warranty Policies