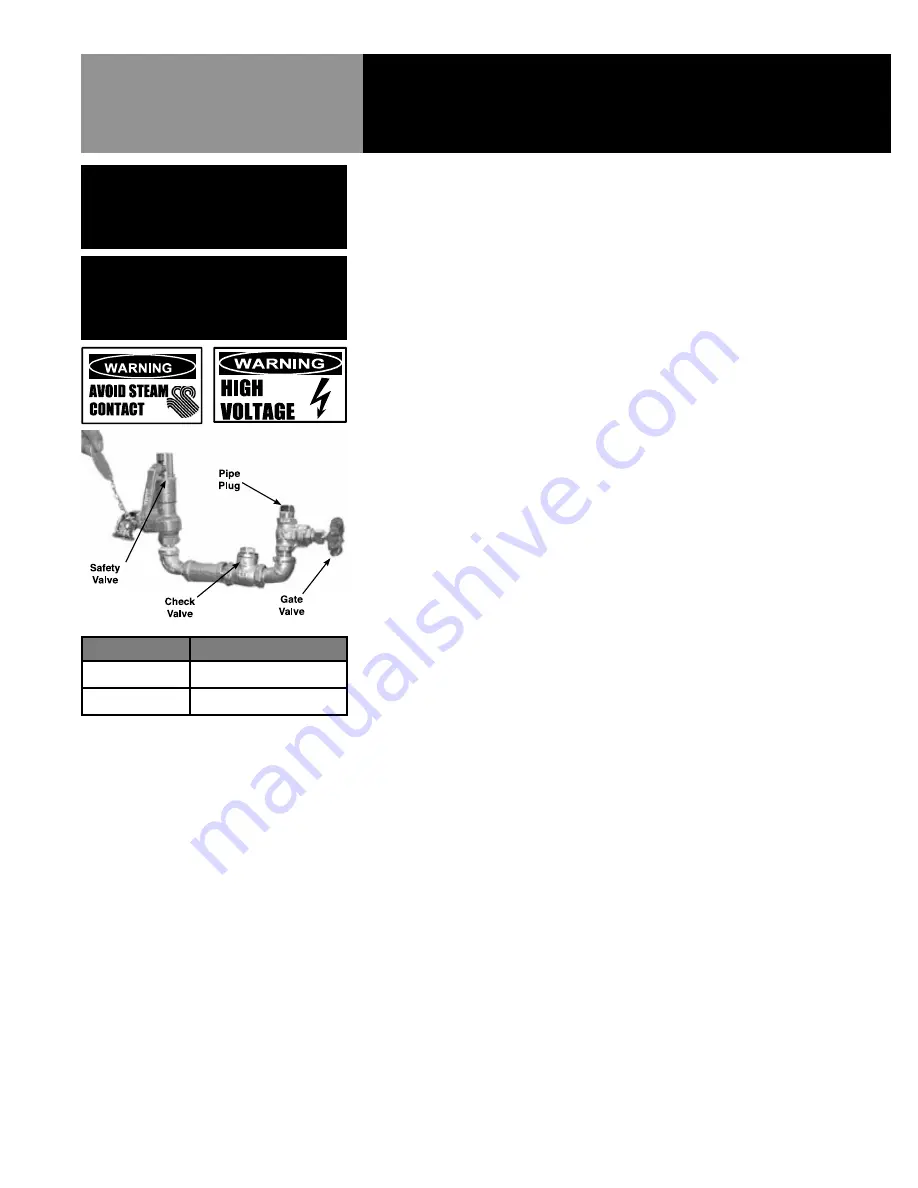
OM/SM-EE-CE 15
Maintenance
WARNING
STAY AWAY FROM THE STEAM THAT IS
BLOWING OUT OF THE SAFETY VALVE.
THE STEAM CAN CAUSE A SEVERE BURN.
WARNING
TO AVOID INJURY, READ AND FOLLOW ALL
PRECAUTIONS STATED ON THE LABEL OF
THE WATER TREATMENT COMPOUND.
3.
Jacket Filling and Water Treatment
The jacket was charged at the factory with the proper amount of treated water. You
may need to restore this water because it was lost as steam during venting or by
draining.
a. If you are replacing water lost as steam, use distilled water. If you are replacing
treated water that ran out of the jacket, prepare more treated water as directed
in step 4, “Water Treatment Procedure.” Do not use tap water.
b. Allow the kettle to cool Remove the pipe plug from the jacket fill assembly.
c. Open the gate valve and pour in the distilled or treated water.
d. Hold the safety valve open to allow air to escape from the jacket while you pour
in the water. Continue to pour until the water level rises to a point between the
marks on the gauge glass.
e. Any air introduced into the jacket during filling must be removed to obtain
efficient heating. See “Jacket Vacuum” on page14.
4.
Water Treatment Procedure
a. Obtain water treatment compound and a pH test kit from your Groen distributor.
b. Fill a mixing container with the measured amount of water required. (See table
at left). Use distilled water only.
c. Hang a strip of pH test paper on the rim of the container, with about 1 inch
(25mm) of the strip below the surface of the water.
d. Measure the water treatment compound (One way to do this is to add the
compound from a measuring cup.)
e. Stir the water continuously, while you slowly add water treatment compound,
until the water reaches a pH between 10.5 and 11.5. Judge the pH by
frequently comparing the test strip color with the chart provided in the pH test
kit. If you are color blind read the test strip color level.
f. Record the exact amounts of water and treatment compound used. These
amounts may be used again, if the same water sources and compound are
used in the future. However, it is best to check the pH each time treated water
is prepared.
Model
Jacket Capacity
EE-20
3-1/4 Gallons
EE-40
4-1/2 Gallons
Содержание Groen EE CE Series
Страница 23: ...OM SM EE CE 23 Wiring Diagram EE 20 208 VOLT 3PH...
Страница 24: ...24 OM SM EE CE Wiring Diagram EE 20 400 VOLT 3 PH...
Страница 25: ...OM SM EE CE 25 Wiring Diagram EE 40 208 VOLT 3PH...
Страница 26: ...26 OM SM EE CE Wiring Diagram EE 40 400 VOLT 3PH...