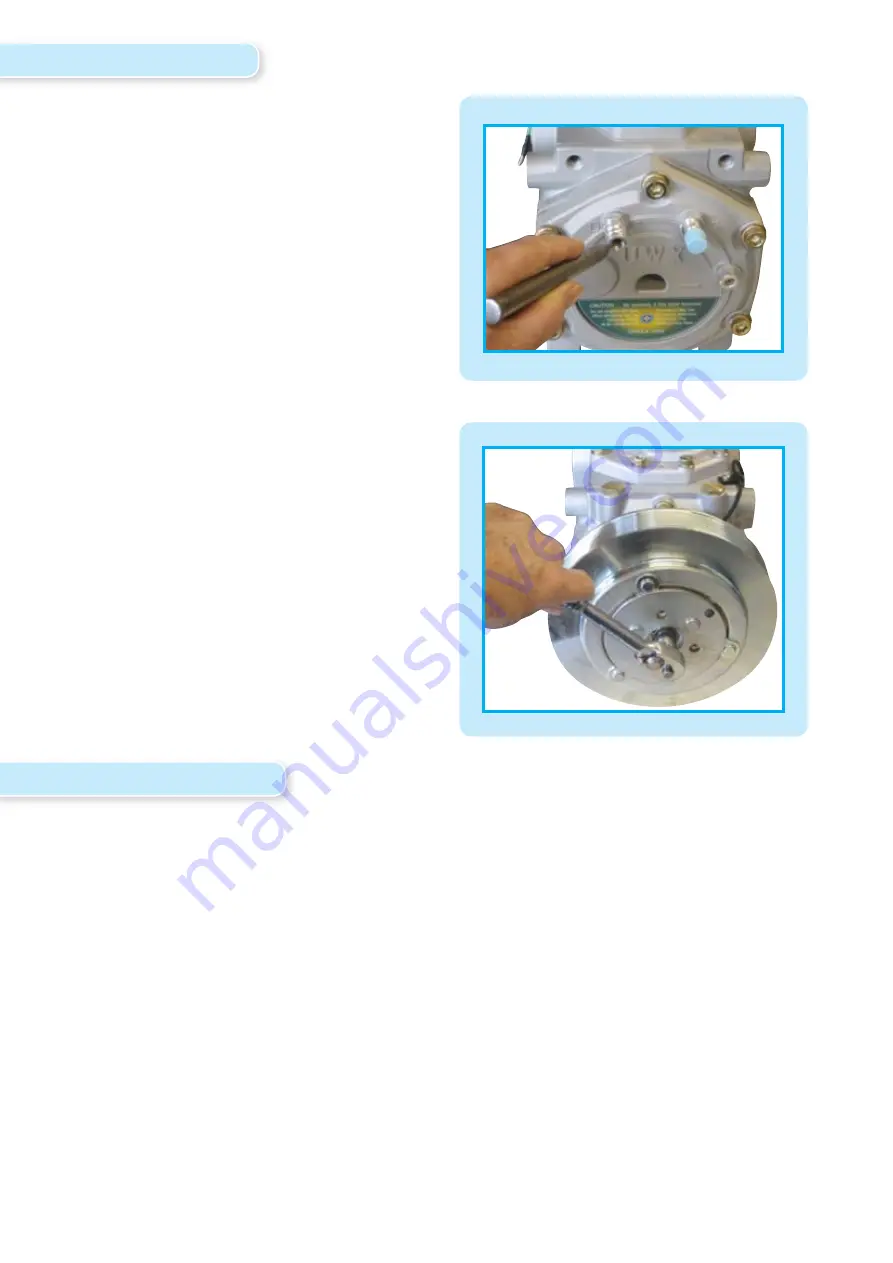
1. Initial Handling
a) Removing transit gas
Before mounting and when handling
a new Unicla UWX compressor for the
first time, remove the dust cap from the
discharge service valve and gently release
the N2 gas as follows.
Take care to not let oil escape.
b) Initial lubrication
Rotate the compressor armature manually
for 4-5 revolutions to ensure proper
lubrication to the working assembly
components. This will avoid damage
during initial start up.
2. System Cleanliness
a) Contamination
The system must be free of both solid particle and chemical contamination before compressor
fitting. Solid particle contamination will cause direct compressor damage and starvation due
to blocked system filters and screens (see section 10). Chemical contamination can reduce
solubility/miscibility of refrigerants and oils, reduce oil viscosity, and cause acid etching and
sludge formation.
b) Flushing
Contaminated systems must be flushed before fitting the new compressor. Individual
component flushing is strongly recommended in systems where solid particle contamination
has occurred during the system assembly process. The compressor, TX valve, pressure control
valves, receiver driers/accumulators and mufflers/pulsation dampers
must not be flushed.
2.
Содержание UWX440
Страница 1: ...UWX550 and UWX440 Installation Guidelines...
Страница 13: ...Notes...