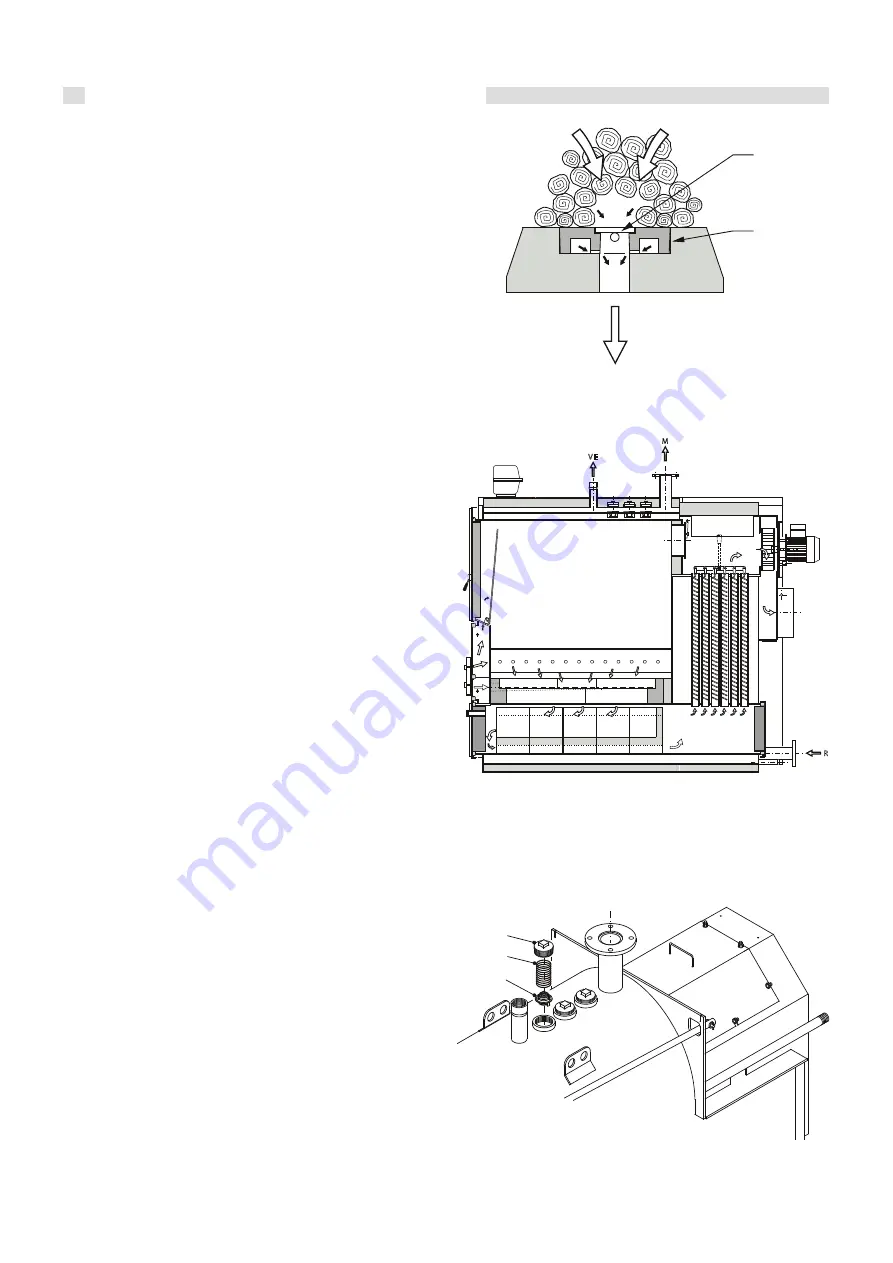
10
Technical features and dimensions
fig. 5
1. Refractory steel grate
2. Refractory cast-iron fire bars
REFRACTORY BURNER (4)
The burner is made up of refractory stone (fig. 3, pos. 4).
This stone has a rectangular central opening through which the
flame passes.
The embers lie directly on the stone which divides the fire wood
storage from the lower combustion chamber.
Furthermore the main refractory stone has a rectangular seat in
which the opportunely grooved cast iron fire bars are placed (fig.
5, pos. 2), which receive the secondary air from a front distributor.
The embers are prevented from falling by a refractory steel grate.
The combustion gases, poor in oxygen and still rich in carbon
not yet combined, travel across the embers and enter the opening
in the centre of the main stone.
Inside this pre-combustion chamber, the gases combine with
the pre-heated secondary air coming through the grooves of
the two cast iron fire bars.
The flame comes out from the lower opening and invades the
combustion chamber.
Due to the high temperatures the refractory burner will become
a bright red colour.
COMBUSTION CHAMBER (5)
Combustion is optimised by increasing the flame temperature
and producing a strong turbulence in the bottom chamber.
For this reason the flame, in addition to not touching cold walls
irrigated by water, bounces and is divided on a semicircular
cradle which rests on the lower exchange surfaces, which, aside
from delimiting the smoke passages, also has the task of
collecting the ashes and possible embers.
The flames, after having bounced off the walls of the bottom
area and the refractory ones, direct themselves with a whirling
motion towards the front part of the combustion chamber and
enter the flue ducts. Combustion will be complete and clean and
the dominant colour will be that of the ashes: white.
M = Hot water flow
R = System return
VE = Expansion vessel
P = Primary air
S = Secondary air
F = Flue gas
fig. 6
THERMOSTATIC VALVES (9)
As is well known, wood normally has a high moisture content
when compared with other types of fuels. The first operation
which occurs inside the fire wood storage is therefore the drying
phase.
The high moisture content can then cause considerable
condensation in the boiler and also in the chimney.
To limit the problem in the boiler it is necessary to maintain high
working temperatures.
For this reason the boiler is equipped with a patented
thermostatic system (fig. 7) which permits the boiler temperature
to be kept constantly high, in particular in the fire wood storage,
where condensation is more likely to occur.
In order to reduce the consequences of condensate formation
(tar dripping, corrosion, etc.) it is advantageous to dimension,
time by time, the wood load to the actual needs, so as to prevent
long stop overs with the wood storage completely full of humid
wood.
Nevertheless all these expedients do not impede the formation
of condensate in the chimney. Therefore we suggest, when bu-
ilding the chimney, to use air-tight components, to prevent the
condensate from damaging the building structure.
fig. 7
1
2
F
F
P
P
S
P
P
P
S
S
F
F
F
F
F
R
M
VE
T1
1
2
3