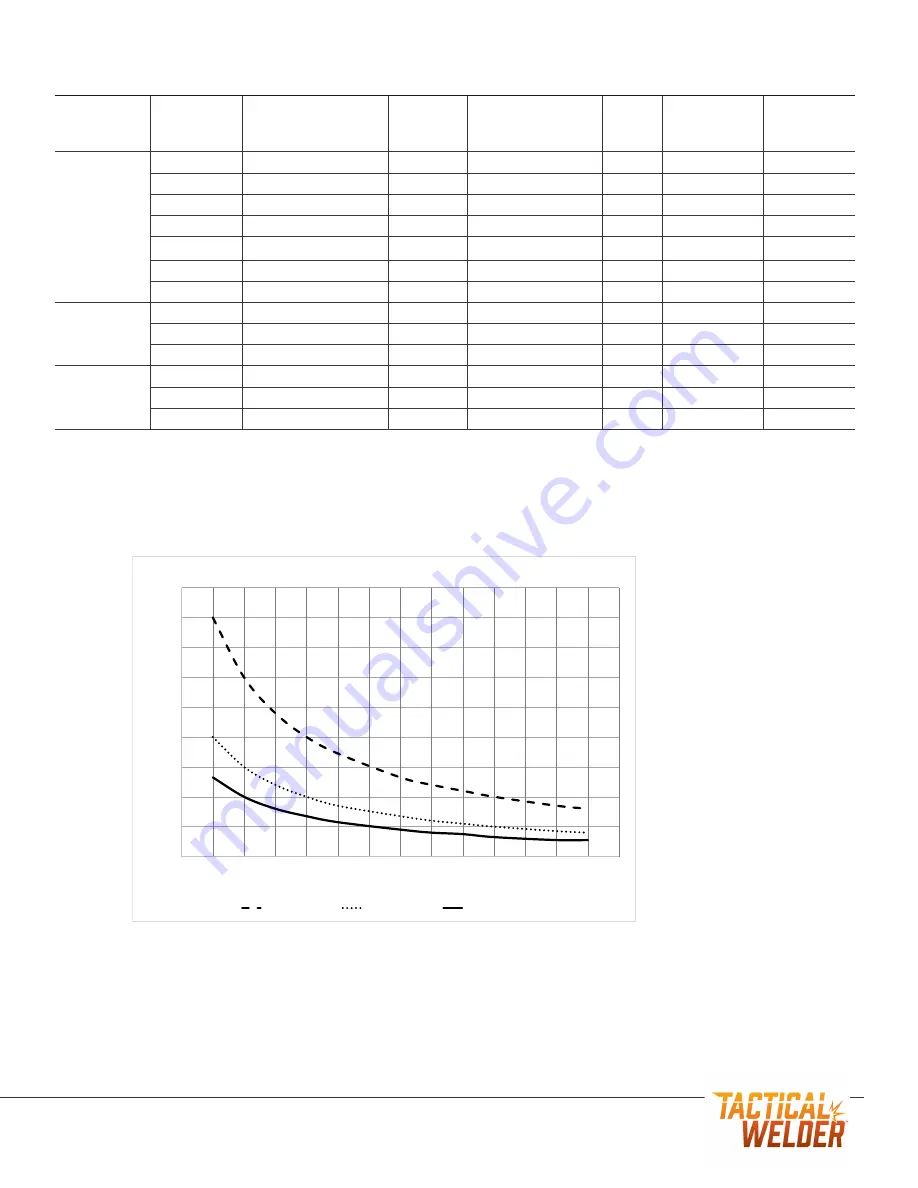
13
Metal Type
Thickness of
Material Being
Welded
Wire Type/ Size
Tweco
#2 Tip Size Shield Gas
Gas
Flow
Rate
Polarity/
Connection to
Tactical Welder
Wire Speed
Control
Setting
Steel
24 – 18 GA
Solid Steel .023”
.023”
75% Argon/ 25% CO2 15-30
DCEP
Stitch
18 GA – 3/16”
Solid Steel .030”
.030”
75% Argon/ 25% CO2 15-30
DCEP
Stitch - 1
1/8” Plus
Solid Steel .035”
.035”
75% Argon/ 25% CO2 15-30
DCEP
Stitch – 2
1/4” Plus
Solid Steel .040”
.040”
75% Argon/ 25% CO2 15-30
DCEP
1 – 4
22 – 14 GA
Flux-Core Steel .030”
.030”
None
None
DCEN
Stitch – 1
1/8” – 3/8”
Flux-Core Steel .035”
.035”
None
None
DCEN
Stitch – 3
1/4” – 1/2” Plus Flux-Core Steel .040”
.040”
None
None
DCEN
3-6
Aluminum
.060”- 1/8”
Aluminum .023”
.030”
100% Argon
10-20
DCEP
1 – 2
1/8” – 1/2”
Aluminum .035”
.040”
100% Argon
15-30
DCEP
2 – 6
1/2” Plus
Aluminum .040”
.045”
100% Argon
20-50
DCEP
4 – 9
Stainless Steel
.080”- 1/8”
Solid Stainless .030”
.030”
Tri-Mix*
20-40
DCEP
Stitch – 1
1/8” Plus
Solid Stainless .035”
.035”
Tri-Mix*
20-40
DCEP
1 – 6
1/8” Plus
Flux-Core Stainless .035” .035”
None
None
DCEN
1 – 6
Application Table
Weld Time per Charge
*Tri-Mix: The specific mix of gases and their respective proportions will be determined by 1. The alloy and thickness of the
stainless steel being welded, and 2. The alloy and thickness of the stainless welding feed wire being used. Please consult
your welding gas distributor or an appropriate reference manual to determine the proper mixture for your application.
General Guidelines
1.
Stitch Mode Welding: When welding metal thinner than 1/8” with batteries as a power source, it is often necessary to use a stitch mode welding
procedure to avoid melting the metal being welded. Start by lowering the wire feed speed control to its lowest setting where the wire just begins to
feed. When you begin welding, a small bead will form and then the wire will melt back just enough to break the arc. The process will weld a series of
small beads with short breaks of time between them. This prevents heat from building up and melting through, known as globular transfer.
2.
Aluminum Welding: We recommend using a contact tip which is .005” bigger than the aluminum feed wire itself and pulling the nozzle about 3/8”
farther out to reduce burn-back.
0
20
40
60
80
100
120
140
160
180
40
60
80
100
120
140
160
180
200
220
240
260
280
300
320
W
el
d
Ti
m
e i
n
Mi
nu
tes
Weld Current (Amps)
Weld Times Per Charge
10% Duty Cycle
20% Duty Cycle
33% Duty Cycle
Содержание Tactical Welder 4800
Страница 9: ...9...
Страница 15: ...15 Tactical Welder Circuit Diagram...