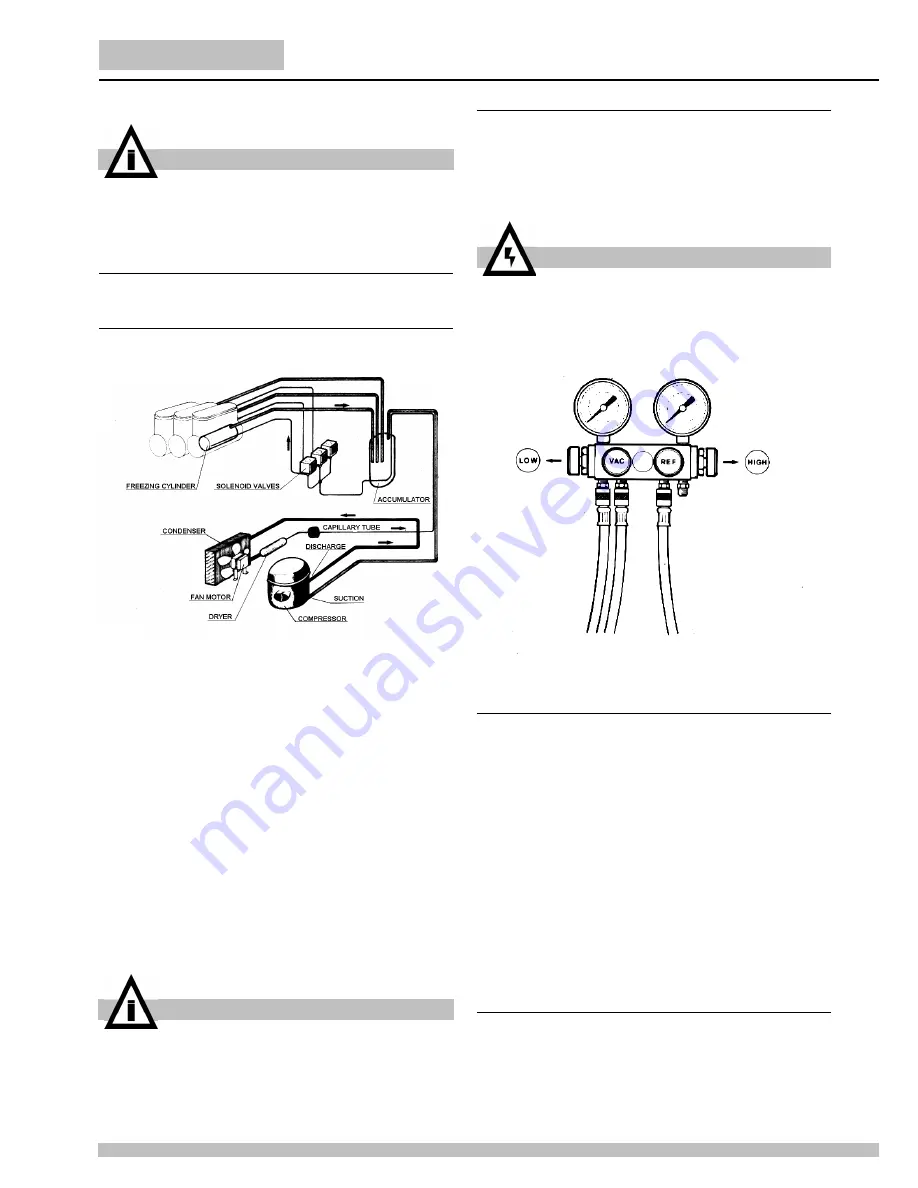
18
MT GL/GLS/UL
polycarbonate.
13. 2 REFRIGERANT CIRCUIT SERVICE
13. 2. 1 CHECKING FOR REFRIGERANT LEAKS
The following procedure is the recommended approach to
systematically inspect the entire system for refrigerant leaks.
figure 13
NOTE
: when using refrigerant leak detector, follow along the
bottom side of the copper tubing. The refrigerant gas is heavier
than air. Where copper tubing is protected by an insulating
jacket, check for leaks at both ends of each jacket section.
Referring to figure 4, perform the following steps:
1
Start inspection at the high pressure line of the compressor.
Check around the soldered connection.
2
Follow the copper tubing to the condenser and check
around the soldered connections at the top and bottom of the
condenser.
3
Check also along the copper curves on both sides of
condenser.
4
Follow the copper tubing to the evaporators, checking
around the soldered connections of dryer and solenoid valves.
5
Remove mixer motors and check the inlet (capillary) and
outlet (suction) tubing.
6
Check the copper tubing all the way back to the
compressor.
7
Check around the low side connections of the compressor
suction and process tubes.
If a leak has been detected, seal it and make a new refrigerant
charge as per instructions in the following paragraphs.
13. 2. 2 DISCHARGING
1
Remove the dispenser panels.
2
Remove the screw cap from the compressor process tube.
3
Connect the process tube to the LOW part of the gauge set.
4
Connect the VAC port of the gauge set to an adequate
approved gas recovery system.
5
Open the LOW and VAC valves and recover the refrigerant.
6
Once the recovery operation is completed, close the LOW
and VAC valves and disconnect the recovery system.
figure 14
13. 2. 3 EVACUATING
Always install a brand new liquid line filter dryer before
evacuating.
1
Connect the REF port of the gauge set to the charging unit.
2
Connect the VAC port of the gauge set to the vacuum pump
and open the VAC valve.
3
Open the line valve of the charging unit and, for a while,
also the REF valve so as to purge air from the REF hose.
4
In multiple bowl models, disconnect the dispenser internal
wiring from all solenoid valves and energize them directly
through an external power source. This way the valves are
opened and the entire system is ready to be evacuated.
5
Open the LOW valve of the gauge set and turn on the
vacuum pump for a minimum of half an hour.
6
While the pump is running, close the VAC valve once a
vacuum has been established.
7
Turn off the vacuum pump.
8
Disconnect the solenoid valves from the external power
source and restore the internal wiring.
13. 2. 4 CHARGING
In the figure 4, the gauge set is shown with four ports (and four
valves) which is the easiest option to be found in the market
since it allows the charging through both low and high side of the
system. Our refrigeration systems are manufactured so as to be
chargeable through the compressor process tube only (low
side): thus, the HI port is never mentioned nor used in the
IMPORTANT
The electric diagram of the dispenser is located in the
inner part of the dispensing side panel.
IMPORTANT
To check for a leak in the low side of the system, it is
advisable to have the evaporators at least at ambient
temperature.
ATTENTION
The refrigerant gas could be highly acid and toxic.
Содержание MT GL
Страница 1: ...MANUALE DI SERVIZIO SERVICE MANUAL MT GL GLS UL...
Страница 2: ...2 MT GL GLS UL...
Страница 12: ...12 MT GL GLS UL 7 SCHEMI ELETTRICI PER MACCHINE PRODOTTE FINO A MARZO 2002 7 1 VERSIONE GLS 7 2 VERSIONE GL UL...
Страница 13: ...13 8 SCHEMI ELETTRICI PER MACCHINE PRODOTTE DOPO APRILE 2002 8 1 VERSIONE GLS 8 2 VERSIONE GL UL...
Страница 23: ...23 16 WIRING DIAGRAMS MACHINES MANUFACTURED AFTER JANUARY 2002 16 1 GLS VERSION 16 2 GL UL...