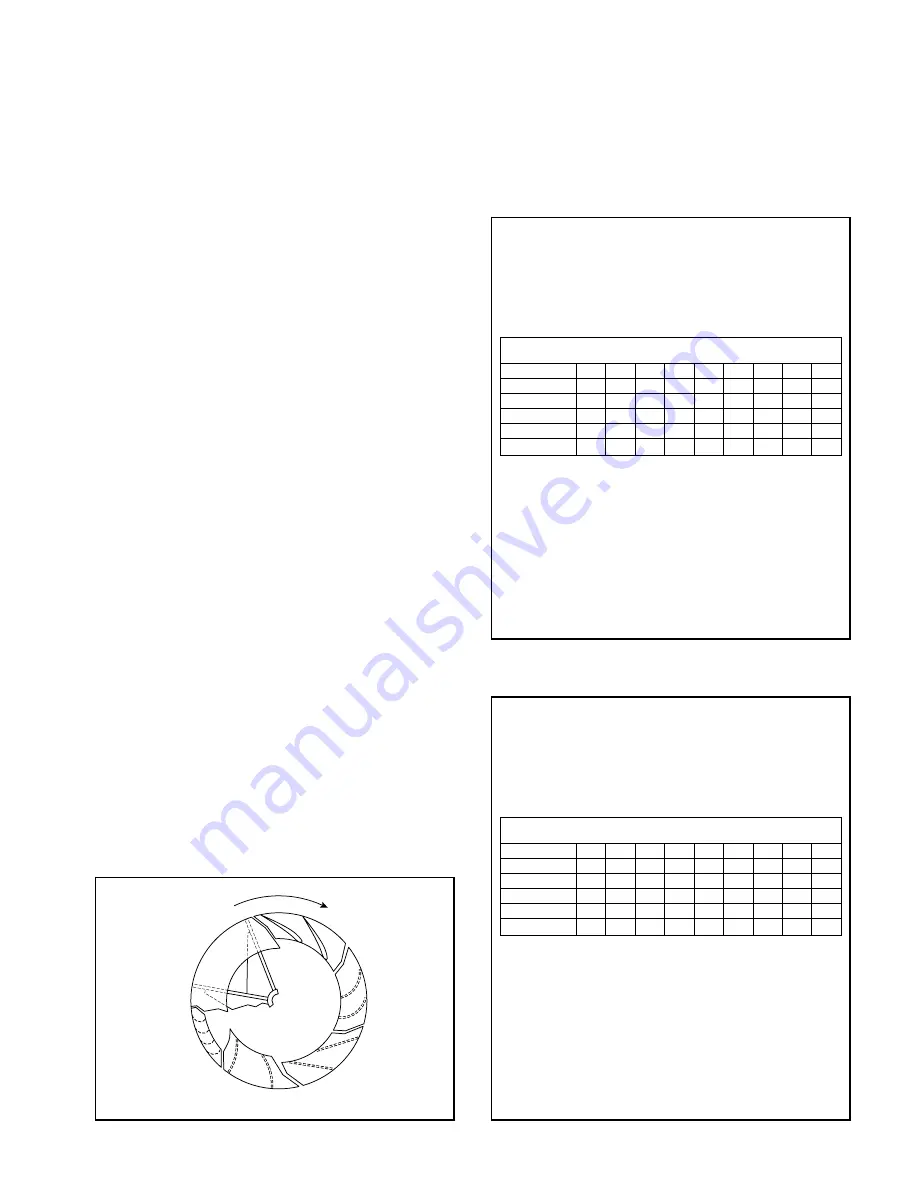
TCF&B ES-52
5
BAF Wheels
HIB, BCS
& BCN
Wheels
BC, RBA &
TBA Wheels
HRT & RTF
Wheels
FC & NFC
Wheels
RBO, RBW, RBR
MBO, MBR &
TBR Wheels
Rota
t
ion
Figure 7. Proper Wheel Rotation
WARNING
1. This equipment must not be operated without proper guarding of all
moving parts. While performing maintenance be sure remote power
switches are locked off. See AMCA Publication 410 for recommended
safety practices.
2. Before starting: Check all setscrews for tightness, and rotate wheel by
hand to make sure it has not moved in transit.
*Suggested initial greasing interval: Relubricate while running, if safety per-
mits, until some purging occurs at seals. Adjust lubrication frequency
depending on condition of purged grease. Hours of operation, tempera-
ture, and surrounding conditions will affect the relubrication frequency
required.
1. Lubricate with a multipurpose roller bearing NLGI No. 2 having rust
inhibitors and antioxidant additives, and a minimum oil viscosity of 500
SSU at 100ºF. Some greases having these properties are:
Shell - Alvania No. 2
Mobil - Mobilith AW2/Mobilith SHC100
Texaco - Premium RB2
American - Rykon Premium 2
2. Lubricate bearings prior to extended shutdown or storage and rotate
shaft monthly to aid corrosion protection.
WARNING
1. This equipment must not be operated without proper guarding of all
moving parts. While performing maintenance be sure remote power
switches are locked off. See AMCA Publication 410 for recommended
safety practices.
2. Before starting: Check all setscrews for tightness, and rotate wheel by
hand to make sure it has not moved in transit.
*Suggested initial greasing interval: Reubricate while running, if safety per-
mits, until some purging occurs at seals. Adjust lubrication frequency
depending on condition of purged grease. Hours of operation, tempera-
ture, and surrounding conditions will affect the relubrication frequency
required.
1. Lubricate with a high quality NLGI No. 2 or No. 3 multipurpose ball
bearing grease having rust inhibitors and antioxidant additives. Some
greases having these properties are:
Shell - Alvania No. 2
Mobil - Mobilith AW2/Mobilith SHC100
Gulf - Gulfcrown No. 2
American - Rykon Premium 2
2. Lubricate bearings prior to extended shutdown or storage and rotate
shaft monthly to aid corrosion protection.
Relubrication Schedule (Months)*
Spherical Roller Bearing - Solid Pillow Blocks
Speed (RPM)
500
1000
1500
2000
2500
3000
3500
4000
4500
Shaft DIA
1
3
⁄
16
" thru 1
7
⁄
16
"
6
4
4
2
1
1
1
1
1
⁄
2
1
11
⁄
16
" thru 2
3
⁄
16
"
4
2
1
1
⁄
2
1
1
⁄
2
1
⁄
2
1
⁄
2
1
⁄
2
1
⁄
2
2
7
⁄
16
" thru 3
7
⁄
16
"
3
1
1
⁄
2
1
1
⁄
2
1
⁄
2
1
⁄
4
1
⁄
4
3
15
⁄
16
" thru 4
15
⁄
16
"
2
1
⁄
2
1
1
⁄
2
1
⁄
4
Figure 8. Safety & Lubrication Instructions for Fans
with Ball Bearings
Figure 9. Safety & Lubrication Instructions for Fans
with Unit Roller Bearings
Relubrication Schedule (Months)*
Ball Bearing Pillow Blocks
Speed (RPM)
500
1000
1500
2000
2500
3000
3500
4000
4500
Shaft DIA
1
⁄
2
" thru 1
11
⁄
16
"
6
6
5
3
3
2
2
2
1
1
15
⁄
16
" thru 2
7
⁄
16
"
6
5
4
2
2
1
1
1
1
2
11
⁄
16
" thru 2
15
⁄
16
"
5
4
3
2
1
1
1
3
7
⁄
16
" thru 3
15
⁄
16
"
4
3
2
1
1
1
Lubrication
Proper lubrication of bearings helps assure maximum bear-
ing life. All fans are equipped with decals indicating relubri-
cation intervals for normal operating conditions. However,
every installation is different and the frequency of lubrication
should be established accordingly.
nance schedule given below.
Motors should be kept dry to avoid electrical short cir-
cuits. Motors kept in storage for long periods of time can
have moisture condense on the windings. Be certain the
motor is dry before using.
Some smaller motors are lubricated for life. Motor bear-
ing lubrication, if required, must follow a rigorous schedule.
Motors less than 10 hp running about eight hours a day in a
clean environment should be lubricated once every five
years; motors 15 to 50 hp, every 3 years; and motors 50 to
150 hp, yearly. For motors in a dusty or dirty environment or
running 24 hours a day, divide the service interval by 2. If the
environment is very dirty or high temperatures exist, divide
the service interval by 4. Lubrication requirements are nor-
mally attached to the motor. Do not overlubricate.
Drive Maintenance
V-belt drives need periodic inspection and occasional belt
replacement. When inspecting drives, look for dirt buildup,
burrs or obstructions which can cause premature belt or
drive replacement. If burrs are found, use fine emery cloth or
a stone to remove the burr. Be careful that dust does not
enter the bearings.
Check the sheaves for wear. Excessive slippage of belts
on sheaves can cause wear and vibration. Replace worn
sheaves with new ones. Carefully align sheaves to avoid
premature sheave failure.
Observe belts for wear. If fraying or other wear is
observed to be mostly on one side of the belts, the drives
may be misaligned. Reinstall the drives according to instruc-
tions given for Fan Installation of Disassembled Units, part
9. Never use belt dressing on any belts.
When replacing belts, replace the entire set. After initial
replacement and tensioning, recheck belt tension after a few
days to adjust belt tension again. (New belts require a break
in period of operation.)
Bearing Maintenance
For instructions covering special lubrication intervals, bear-
ing assembly or disassembly, or installation details, see
attached documents. Any bearing which is disassembled
should be kept separate from other bearing parts as com-
ponents may not be interchangeable. Maintain cleanliness
of components and bearings to prevent bearing contamina-
tion.
Bearing failure can occur from many causes. See
Troubleshooting section for details.
Note: All speeds shown do not apply to all shaft sizes in that
group. Consult the factory if in doubt of maximum speed for
a particular bearing.