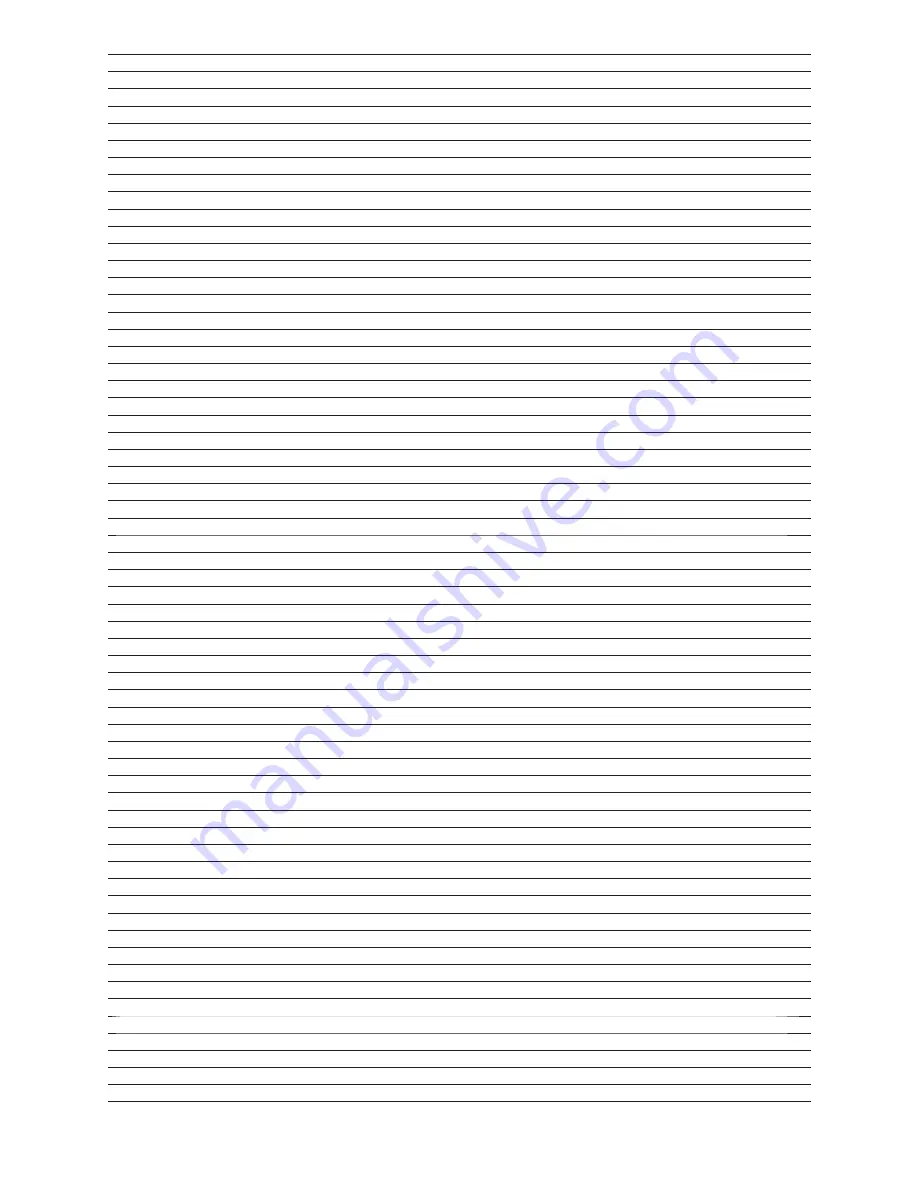
2
TABLE OF CONTENTS
SECTION
PAGE
1. INTRODUCTION
3
1.1 APPLICABLE DOCUMENTATION
3
1.2 SCOPE OF MANUAL
3
2. CONVENTIONS AND DATA PLATE
3
2.1 GRAPHIC CONVENTIONS IN THIS MANUAL
3
2.2 DATA PLATE
4
3. LIFTING
5
4. DESCRIPTION
5
4.1 FLOW BY DIRECTION
6
4.2 SPECIFICATIONS
7
5. INSTALLATION
8
5.1 GENERAL
8
5.1.1 LOCATION
10
5.1.2 BLOWER AIR INTAKE
10
5.1.3 SOFT FOOT
11
5.2 SAFETY
11
5.3 LUBRICATION
12
5.3.1 FILLING PROCEDURE
13
5.3.2 FREQUENTLY ASKED QUESTIONS REGARDING LUBRICATION
13
5.3.3 HAZARDS ASSOCIATED WITH BREAKDOWN OR IGNITION OF LUBRICATION
14
5.4 PIPING CONNECTIONS
14
5.4.1 BLOCKAGE OR RESTRICTION
14
5.5 COOLING COILS (OPTIONAL)
15
5.6 COOLING WATER CONNECTIONS AND SPECIFICATIONS — COOLING COILS (OPTIONAL)
15
5.7 MOTOR DRIVES
16
5.7.1 DIRECT COUPLED
16
5.7.2 V-BELTS
16
5.7.3 SETTING V-BELT TENSION
17
5.7.4 V-BELT TROUBLESHOOTING
18
5.8 SPECIAL INSTRUCTIONS FOR BLOWERS WITH EXTERNAL LUBRICATION SYSTEMS
18
5.9 MOTOR AND ELECTRICAL CONNECTIONS
19
6. OPERATION
20
6.1 GENERAL
20
6.2 START-UP CHECKLIST
21
6.3 OPERATING
21
6.4 STOPPING
22
6.5 METHANE GAS APPLICATIONS
22
6.6 WATER INJECTED BLOWERS
22
6.6.1 OPERATION
23
6.6.2 SHUTDOWN
23
6.7 RECOMMENDED SHUTDOWN PROCEDURE TO MINIMIZE RISK OF FREEZING OR CORROSION
23
7. MAINTENANCE
24
7.1 GENERAL
24
7.2 REGULAR MAINTENANCE
25
7.3 SPARE PARTS
25
7.4 FACTORY SERVICE & REPAIR
26
7.5 LONG TERM STORAGE
26
8. MODEL 4000 AND 5500 DISASSEMBLY AND REASSEMBLY
27
8.1 DISASSEMBLY OF BLOWER
27
8.2 ASSEMBLY OF BLOWER
28
9. TROUBLESHOOTING
33
10. ASSEMBLY CLEARANCES
34
11. TORQUE CHART
34
12. RECOMMENDED LUBRICANTS
35
13. SPECIAL TOOL DRAWINGS
36
14. PARTS LISTS AND ASSEMBLY DRAWINGS
37
15. DECLARATION OF INCORPORATION
61
16. WARRANTY — BLOWER PRODUCTS
62
17. OPERATING DATA FORM / PRODUCT REGISTRATION
63