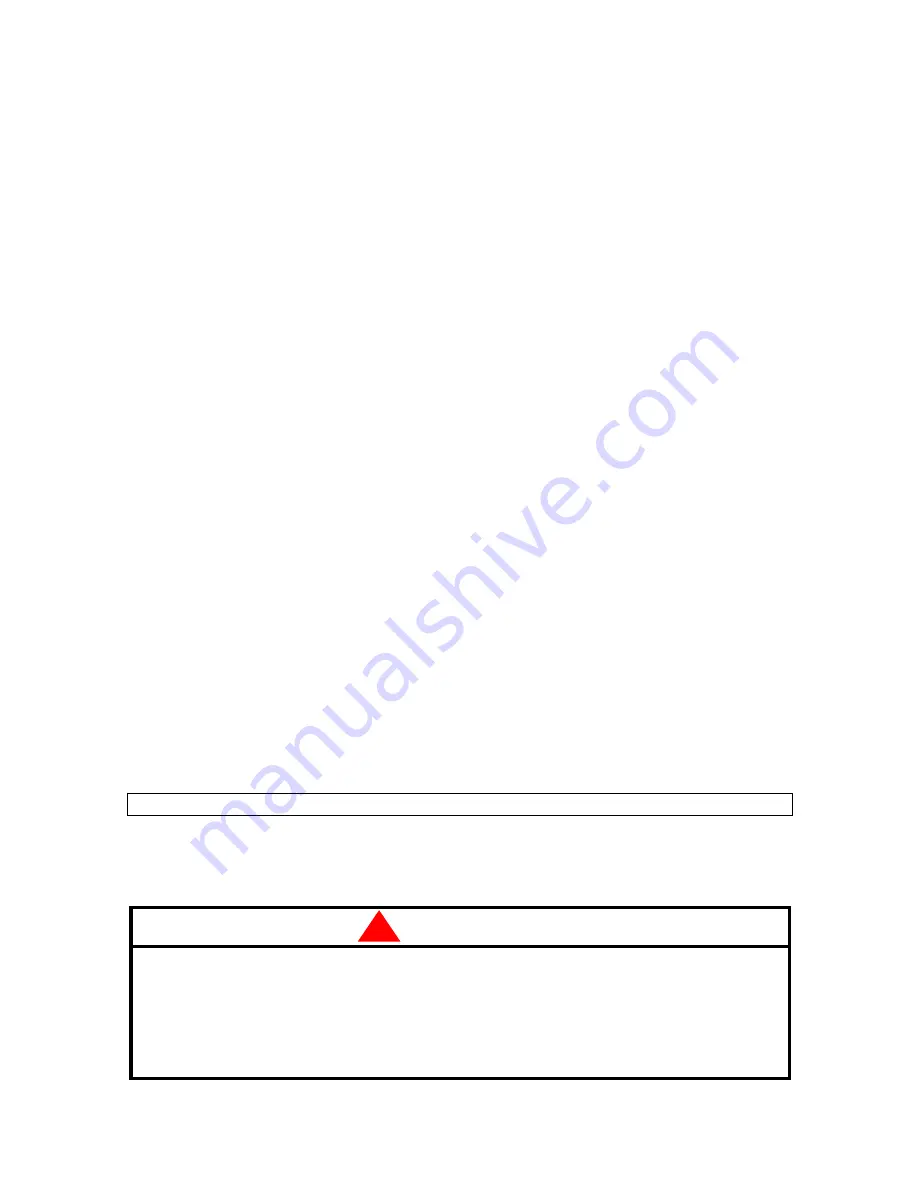
Service Manual # 67
Page 6 of 36
Under no conditions should the pump be used to support external piping loads. Piping and other
equipment should be independently supported.
The discharge line must be designed with the maximum pressure rating of the pump in mind.
Excessive pressure could cause damage to your motor and/or pump. If a pressure relief valve has
not been supplied with the pump, some other means of pressure protection must be utilized. This
could include in-line safety valves, pressure shutdown switches or other similar devices.
Every pump installation should have a good foundation. Its structure should be sufficiently strong to
hold the pump rigid and to absorb any strain or shock that may be encountered. The installation
should be leveled, checked for proper piping alignment, and then fastened securely.
Pumps should be filled with fluid at installation and should never be allowed to run dry.
6000, 7000 & 8000 Series pumps have internal venting which makes them directional. The direction
of rotation is specified from the shaft end of the pump. Unless otherwise specified, rotation is
assumed to be clockwise (CW), which places the suction port on the right side of the pump when
viewed from the shaft end. Operation of the pump in a direction other than specified can cause
damage to both the pump and magnets.
Consult Tuthill personnel whenever unusual conditions of speed, pressure, vacuum or viscosity are
encountered.
The Tuthill pump is a positive displacement pump. As the pump rotates, liquid is positively
delivered to the discharge side of the pump. If the discharge line is closed off, pressure will
increase until the magnets de-couple, the drive equipment stalls and/or fails, the pump breaks or
ruptures, or the piping bursts. This could result in serious bodily injury or death. To prevent this
from happening, the use of a pressure relief valve is required. A relief valve that directs the flow back
to the supply tank is recommended.
Pumps shipped from the factory with relief valves are assembled for clockwise or counterclockwise
rotation as originally specified. The adjusting screw must always point toward the suction line. If
you want to change rotation, the relief valve assembly must be removed and turned 180°, and the
bracket must be rotated 180°.
Section 4: Pressure Limitations
Standard models have pressure ratings as shown in Table 1. Standard canisters are designed to
withstand the maximum rated discharge pressure of the pump. The internal venting arrangement
will normally result in a pressure in the canister that is less than the discharge pressure.
!
WARNING
Exceeding the maximum canister pressure may cause a canister failure resulting in the release of
the fluid being pumped. Refer to the Optional Equipment section for options available for safely
addressing this concern.
Consult the factory regarding any applications where the canister pressure is in question.
Содержание 6000
Страница 28: ...Service Manual 67 Page 28 of 36 Figure 3 Typical 6110 Series Pump ...
Страница 29: ...Service Manual 67 Page 29 of 36 Figure 4 Typical 7110 Series Pump ...
Страница 30: ...Service Manual 67 Page 30 of 36 Figure 5 Typical 6200 Series Pump ...
Страница 31: ...Service Manual 67 Page 31 of 36 Figure 6 Typical 6210 Series Pump ...
Страница 32: ...Service Manual 67 Page 32 of 36 Figure 7 Typical 6300 7200 8200 Series Pump ...
Страница 33: ...Service Manual 67 Page 33 of 36 Figure 8 Typical 6310 7210 8210 Series Pump ...
Страница 36: ...Service Manual 67 Page 36 of 36 Notes 7 00 ...