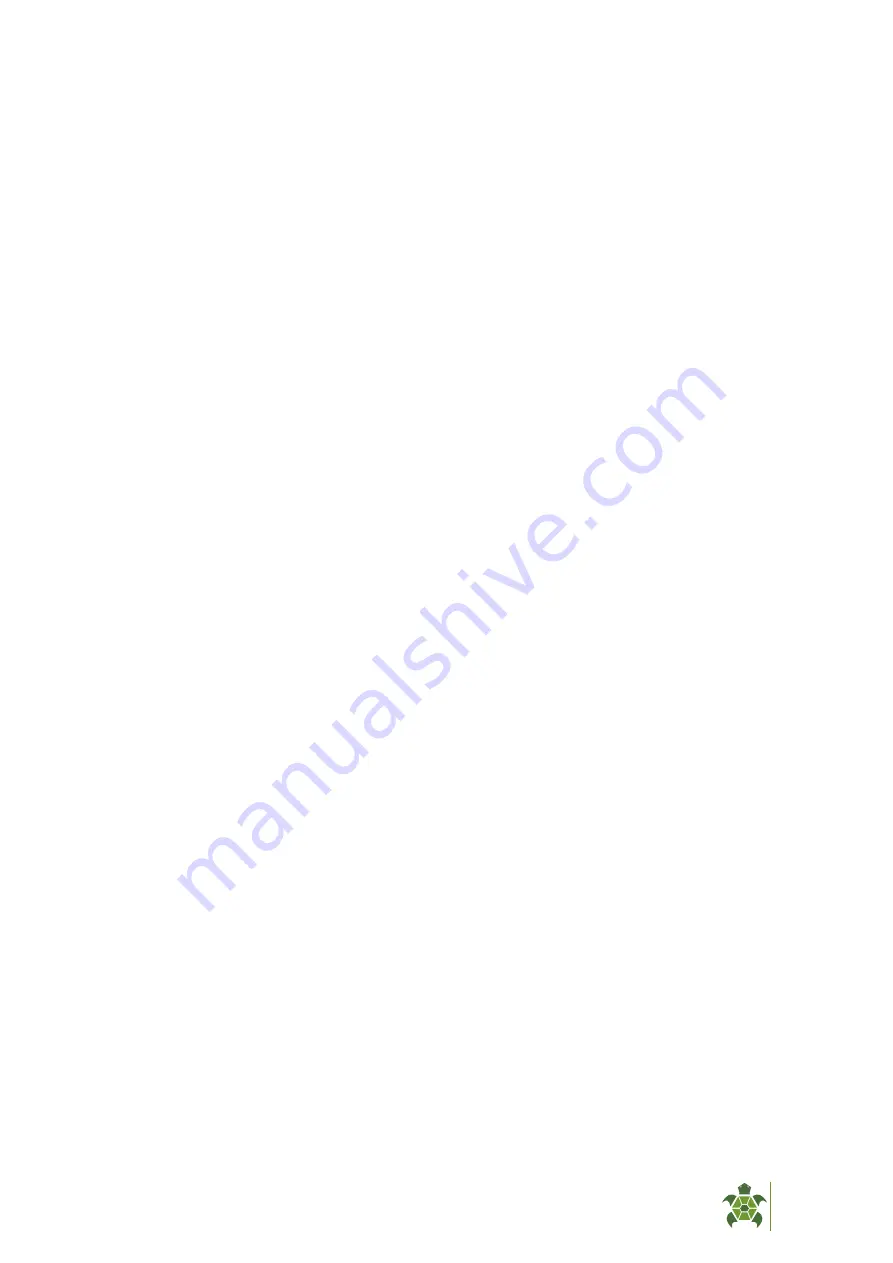
TURTLE
TOUGH
®
23
How Do I Determine The Calibration Frequency?
It is important to note that you can never rely on our guideline as to the basis for your calibration requirement.
Every chemical process is unique and the accuracy required can only be determined by your site requirements and
expert process control personnel. Each user will need to establish a drift profile on their application before
deciding on an appropriate calibration interval. Cleaning and calibration intervals can vary significantly across
individual applications. To determine the drift characteristics you will need to periodically test the sensor against
a known buffer or accurate grab sample to determine the rate of drift (ie. the difference between the displayed
value and the standardised solution). Test frequently at the half-life of your expected calibration frequency to
determine how far the sensor has deviated from the standard solution. Once the sensor reaches the threshold
of your accuracy requirement, that is a good indicator for establishing your calibration regime. It is recommended
that a sensor is properly cleaned each time it is removed for calibration. Even if it does not appear dirty, you
should following the cleaning process to remove microscopic contamination that will affect the performance of
the sensor.
Conditioning For Calibration
After the sensor has been cleaned, it must be thoroughly rinsed with deionized water to remove any residual
cleaning reagents. The sensor can then be soaked in pH 4 buffer to recondition the pH and reference elements.
Some sensors will also require conditioning in saturated potassium chloride if the reference junction has been
depleted of the ions in the solid-state conductive polymer (typical for clean water applications). Condition the
sensor in saturated potassium chloride and/or pH 4 buffer for whatever period is required to achieve optimal
calibration results.
Sensor Selection For Individual Process Lines
No sensor should be used beyond the indicated temperature and pressure limitations for that given sensor.
Sensors should only be used for the application(s) that an authorised TurtleTough representative has recommended.
If you are unsure that your sensor is recommended for a particular application, please contact Turtle Tough.
Avoiding Thermal Shock
For high-temperature applications where process liquid exceeds 70°C, you will prolong the life of the sensor by
avoiding thermal shock. Thermal shock occurs when you rapidly change the temperature of the sensor from hot
to cold or vice versa. This rapid expansion/contraction of sensor components can damage internal elements and
cause micro-cracking that will accelerate the rate of deterioration. In extreme cases, it will crack the sensing ele-
ment causing a total failure. To avoid this the sensor should be heated or cooled slowly during removal/insertion
and cleaning and calibration processes.
TIPS:
Always allow sensors to air cool back to ambient before inserting into a cold liquid (i.e. such as buffer
or cleaning solution). When heating up the sensor, wherever possible, gradually heat the sensor. If this is not
possible in the process, heat the sensor in 2 stages prior to inserting the sensor in the process. One such method
is placing the sensor in hot tap water (i.e. at 50-60 deg C) first and allowing it to get up to temperature, prior to
inserting it into a hot process. This will greatly reduce the thermal shock and extend the life of the sensor.