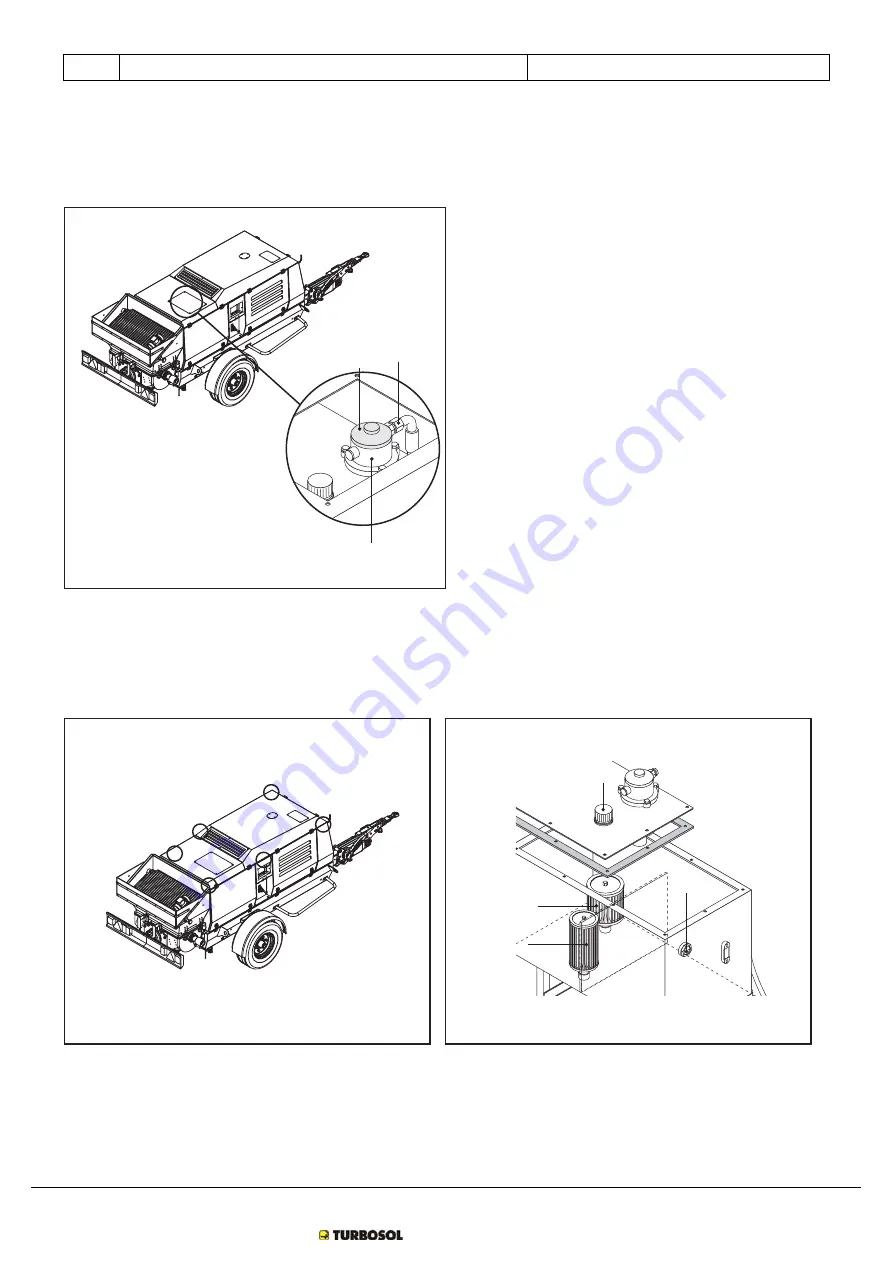
EN
BM 30
IS13/02 - 561291
8 - MAINTENANCE
8
-
Pag. 10/15
THIS MANUAL IS PROPERTY OF
-
ANY TOTAL OR PARTIAL REPRODUCTION IS STRICTLY FORBIDDEN
Cap.
There are 3 litres in the hydraulic tank: one on the lid to be replaced every 500 hours and 2 inside the tank to be replaced every
1,000 hours.
- Loosen the four screws from the oil filter inspection carter located on the fixed bodywork, to replace the filter (FIG.56-REF.1).
- Loosen the filter cap (FIG.56-REF.2), remove and replace the filter cartridge.
- Tighten the cap again (FIG.56-REF.2) and close the inspection carter using the screws.
3
1
2
FIG.56
8.7
II OIL FILTER REPLACEMENT
- Remove the fixed bodywork by loosening the screws on the its supports and brackets blocking it to the hydraulic tank
(FIG.57).
2
3
4
5
FIG.57 FIG.58
- Opening the cock located underneath the oil tank, drain it ensuring to place an adequate container for oil collection.
- Disconnect the hydraulic duct (FIG.56-REF.3).
- Loosen and replace the internal filters (FIG.58-REF.2/3), close the tank checking the gasket's state (replace if required).
- Open the cap (FIG.58-REF.4) and fill with 75 litres of TOTAL AZOLLA HZS 46 oil.
- Always check the level on the sight glass (FIG.58-REF.5).