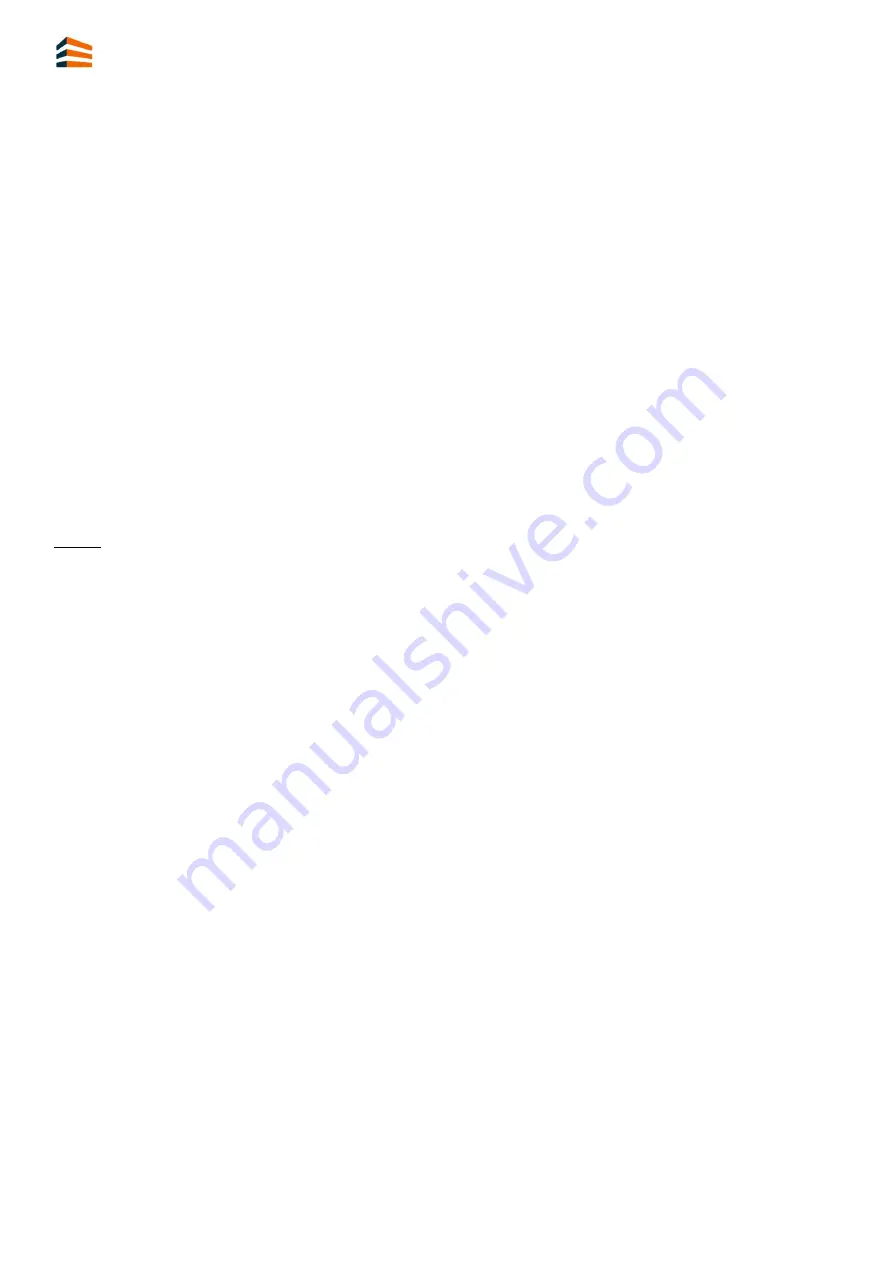
28
3T
After use at each site, ensure that the mobile tower is cleaned with a clean cloth.
Inspect parts before each assembly, particularly:
- Castor wheels tyres and brakes.
- Safety devices.
- Working platform hooks and fasteners.
- The plywood on the working platforms.
- The stabiliser mounting brackets.
All parts with the following defects:
- Permanent deformation.
- Perforations.
- Score marks (as a result of grinding, for example...)
- Severe oxidation
... should be discarded!
If in doubt, change the part.
When the part is being changed, it must be replaced with a genuine part.
Keep parts clean, and safety devices in good working order.
Replace or clean all the panels or stickers with operating and safety instructions.
Checks:
This product should be checked periodically and the results of these checks should be recorded (see the manufacturer check
sheet FV-02408-1XX).
Regulatory checks (provided for in the French decree of 21
st
December 2004) are outlined as follows:
A check prior to use at each installation site:
- when the mobile tower is used for the first time,
- when the mobile access and working tower is dismantled and then re-assembled.
- following changes in usage conditions, or atmospheric or environmental conditions which may affect the safe use of the mobile
access and working tower,
- when the tower has not been used for at least a month.
This check should include a suitability assessment, an assembly and installation assessment, as well as an assessment of its
condition. This check will be recorded in the establishment’s safety records for traceability.
A daily check
This is a condition assessment.
This check will be recorded on a sheet attached to the access hatch for traceability.
A quarterly check
For the mobile access and working tower, the scope of this check is comparable to the daily check. It will be carried out at least
once every 3 months, and will be recorded in the establishment’s safety records for traceability.
Nota bene
: These checks can only be carried out by personnel holding a certificate of competence entitled “Checker
and User”
which has been issued by company management.
For more information and details regarding checklists, please refer to RECO R.457, annex 3, 3bis, 4, 5, 6.