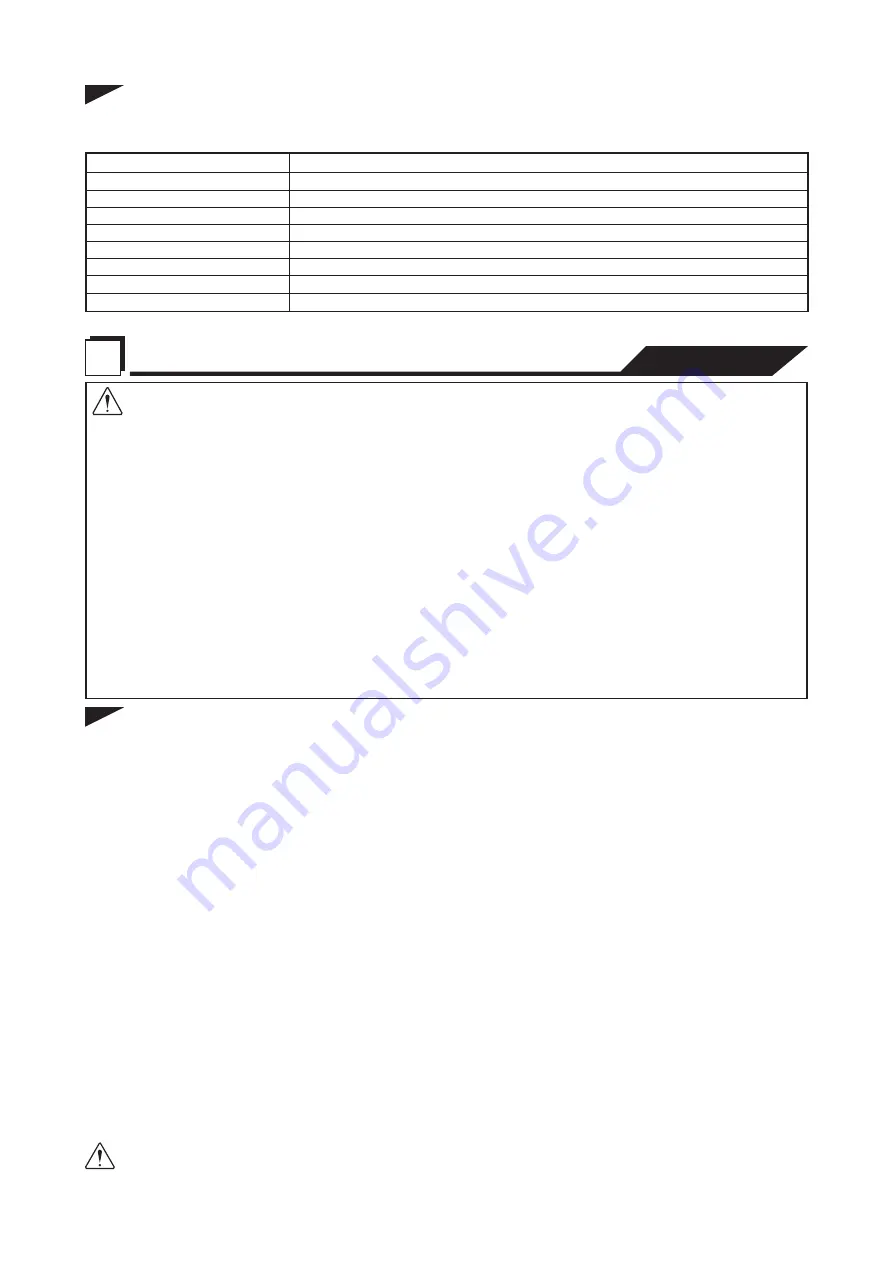
-13-
LH6110/8110 Disassembly
Before disassembly, drain the oil from the pump.
(1) Remove the strainer stand.
Remove the hex. nuts at the bottom of pump, then remove the strainer stand from the pump.
(2) Remove the lower pump casing.
Remove the hex. nuts and spring washers, then remove the lower pump casing from the pump.
(3) Remove the impeller.
With a box spanner or other tool, remove the hex. double nuts and plain washers, then remove the
impeller, impeller adjusting washer and lower shaft sleeve from the shaft.
(4) Remove the upper pump casing.
Remove the hex. nuts and spring washers to remove the upper pump casing.
(5) The upper shaft sleeve can be removed easily once the upper pump casing is removed.
(6) When absolutely necessary, the mechanical seal can be removed by first removing the oil casing.
See also the manual that comes with the replacement mechanical seal.
Note:
Note:
• Before disassembling the pump, first detach the cabtyre cable from the receptacle or terminals,
after making certain the power supply (circuit breaker, etc.) is turned off. To avoid electrical
shock, do not work with wet hands. Never check the operation of any parts (impeller rotation,
etc.) by turning on the power while the unit is partially assembled. Failure to observe these
precautions may result in serious accident.
• Do not disassemble or repair any parts other than those designated here. If repairs are
necessary in any other than the designated parts, consult with your nearest dealer or Tsurumi
representative. Improper repairs can result in electrical leakage, electrical shock, fire, or water
leaks.
• After reassembly, always perform a test operation before resuming use of the pump. Improper
assembly will cause the pump to malfunction, resulting in electrical shock or water leaks.
The procedure for disassembly and reassembly is shown here to the extent necessary for impeller
replacement. A specialized environment and facilites are necessary for work on the mechanical seal
and the motor parts. Contact your nearest dealer or Tsurumi representative in the event such repairs are
necessary.
WARNING
8 DISASSEMBLY AND REASSEMBLY
Remove the hex. bolts and spring washers, then detach the oil casing from the pump, being careful not to
damage the sliding surface of the mechanical seal. Remove the mechanical seal on the rotating end from the
shaft, then remove the mechanical seal on the upper fixed end.
A worn impeller can have sharp edges; be careful to avoid injury.
CAUTION
Replacement Parts
The table lists the parts that need to be replaced periodically. Replace these using the recommended
frequency as a guideline.
Mechanical Seal
Oil (Turbine Oil VG 32 )
Bearing Grease
Part
Recommended Frequency
Packing, O-Ring
Oil Seal
When oil in oil compartment becomes milky.
Every 6,000 hours of 12 months, whichever comes first.
At overhaul
Each time pump is disassembled or inspected
When the lip is worn, and each time pump is disassembled or inspected
Labyrinth Ring
Shaft Sleeve
Cathodic Protection Plate
When it becomes worn.
When it becomes worn.
When it becomes corroded.