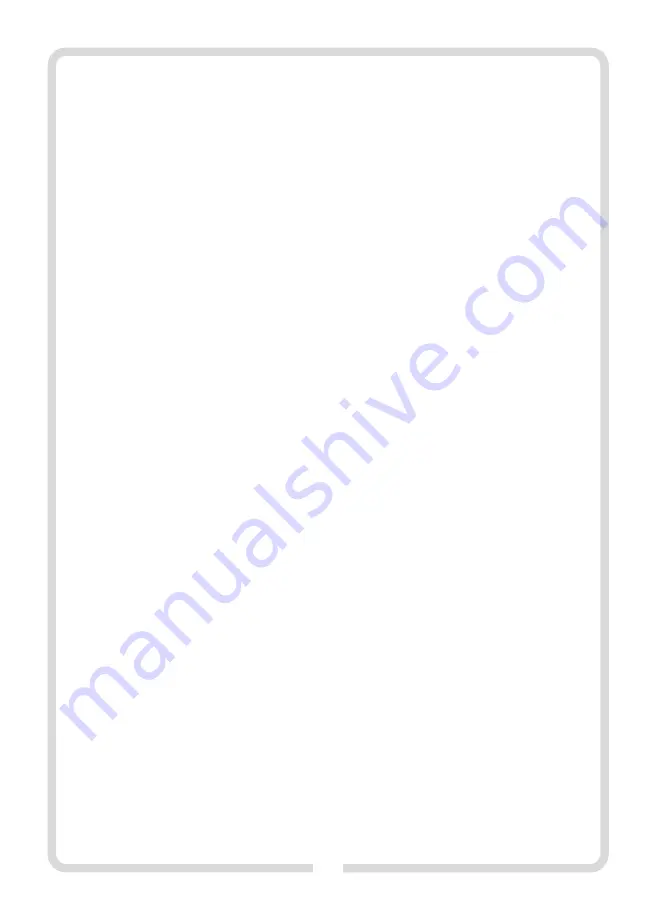
6
S
2 30 min – interrupted operation, rated operation time 30 min.
NOTE:
After completing the replacement, the grinding wheel should run for
at least 1 minute with no load.
NOTE!
After 30 minutes of constant load operation stop using the machine
and allow it to cool down completely.
BEFORE YOU START OPERATION:
PREPARING FOR OPERATION:
1. Make sure the power source parameters match the grinder
After unpacking the product check whether all components are present
parameters provided on its nameplate.
and install all parts supplied separately by following the assembly
2. Make sure its switch (
1
) is in off position.
instructions.
3. When using an extension cord make sure its parameters and cable
NOTE:
Before you start any installation or maintenance/adjustment
cross-section meet the grinder power requirements. Extension cords
always make sure that the machine is disconnected from the mains.
should be as short as possible. When in use extension cords must be
fully uncoiled.
n
Positioning the machine
4. Before you start operation check whether grinder fixing is secure,
To ensure operation safety, fix the grinding machine to a flat and stable
making sure the grinding wheels move without any obstacles.
working surface (e.g. a workbench).
Place the grinder on a stable horizontal surface (table, bench) in an area
OPERATION:
providing free access and safe operation. Using the base mounting holes
n
Turning on/off
(
7
) install the machine on the bench securely with four fixing bolts. Bolts
To turn the tool on set the switch (
1
) in position
I
.
length depends on the bench top thickness.
To turn the tool off set the switch (
1
) in position
0
.
n
Installing the machined object supports
NOTE:
After changing or when starting operation, the grinding wheel
Machined object supports (
3
) should be installed as shown in Fig.
A1
.
should run for at least 1 minute with no load.
The gap between grinding wheel (
4
) and the machined object support
n
Grinding
(
3
) cannot exceed 2 mm and must be adjusted on a regular basis
Place the object to be ground on the machined object support (
3
) and
(see: Fig.
B
).
press it against the grinding wheel (
4
). For optimum grinding effect keep
NOTE:
Adjustments can be made only when the grinding wheel is stopped.
moving the object slightly from one side to the other. This is the best way
If the grinding wheel is worn so much that it is not possible to adjust the
both to provide optimum performance and uniform grinding wheel
support gap as required, replace the grinding wheel.
wear. Please note that objects being ground heat up intensely.
n
Installing the anti-spark guards
Considering this, it is recommended to cool down the object machined
Anti-spark guards (
5
) should be installed as shown in Fig.
A2
.
from time to time.
The gap between grinding wheel (
4
) and an anti-spark guard (
6
) cannot
During operation the grinding wheel loses its process properties i.e.
exceed 2 mm and must be adjusted on a regular basis (see: Fig.
B
).
pores get clogged due to material penetrating inside and it loses its
NOTE:
Adjustments can be made only when the grinding wheel is stopped.
circular shape. To open the pores it is recommended to use diamond or
n
Replacing grinding wheels
other dressers.
NOTE:
Protect the grinding wheel against falls, impacts and greasy
WARNING:
Dusts of certain materials, for example, lead containing
contamination.
It is prohibited to use the machine with grinding wheels
paint coats, some wood types, minerals and some metals can be harmful.
damaged or non-compliant to specifications. Always check the grinding
Direct physical exposure to dusts or inhaling them can result in allergic
wheel for any damage before installation.
reactions and/or respiratory system diseases in operator and persons
Check grinding wheel using the so-called
«
sound
»
method. After placing
staying in the working area. Some dusts, e.g. oak wood or beech wood
your grinding wheel on a wooden bar turn and tap it with a mallet; the
dust are considered to be carcinogenic, especially when combined with
check should cover both sides of the grinding wheel and different
wood treatment chemicals (chromates, wood impregnates). Asbestos
distances from the hole:
containing materials can be machined by specially trained personnel
a)
pure metal sound:
the grinding wheel is not damaged – it can be used.
only.
b)
rattling and quick stopping sound: the grinding wheel is cracked – it is
– Always keep the workplace well ventilated.
not allowed to use it as using it can be dangerous to the user.
– Dust masks are recommended
.
To replace a grinding wheel (
4
) use a Ph2 screwdriver and an M8 flat
Observe all valid national and local regulations on handing materials to
wrench to undo 3 fixing screws (
8
) and remove the side guard (
9
)
be machined.
(see: Fig.
C
). Loosen the fixing nut (
10
) with an M19 flat wrench holding
MAINTENANCE AND STORAGE:
the nut fixing the pressure flange from the other side.
This power tool does not require any special maintenance. Store the
NOTE:
The left grinding wheel is fixed with a left-hand thread, the right
machine in a place away from children, keep it clean and protect from
cutting wheel is fixed with a right-hand thread
.
humidity and dust. Storage conditions should exclude any mechanical
Then, remove pressure flange (
11
), paper washer (
12
) and the grinding
damage and weathering.
wheel off the spindle (
13
). Now you can replace the grinding wheel. To
This device meets the requirements of both national and European
install a new grinding wheel perform the above steps in opposite
direction. Pressure flanges should be pointed with their concave sides
standards and safety guidelines. Any repair should be carried out only by
towards the grinding wheel.
qualified personnel using original spare parts.
Содержание TS121501
Страница 2: ...2 A 5 6 4 3 5 B 2 1 7 3 4 3 4 2 2 5 6 19 C 10 11 11 12 8 9 13 14...
Страница 13: ...13 TS121501 TS152501 TS203501 RCD 30 RCD...
Страница 14: ...14 a a PROFIX...
Страница 15: ...15 a a a 1 2...
Страница 18: ...18 34 03 228 n PROFIX...