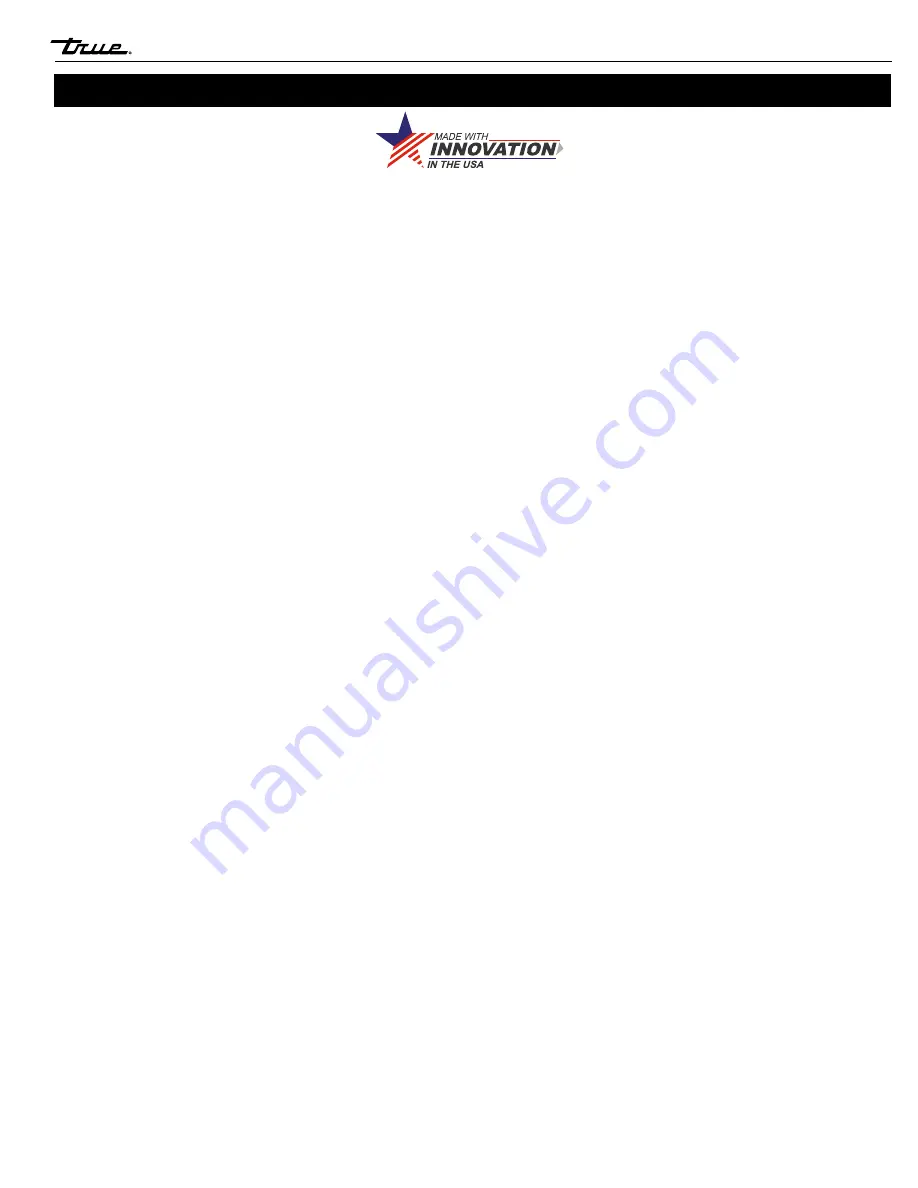
TEC_TM_098 REV. A
10/12/2020
Page 31 of 32
truemfg.com
S C I E N T I F I C S E R I E S
This warranty only applies to units installed after January 1, 2020 for USA Foodservice & Retail and after July 1, 2020 for Canada.
THREE-YEAR PARTS & LABOR WARRANTY
ADDITIONAL TWO-YEAR HFC COMPRESSOR WARRANTY AND ADDITIONAL FOUR-YEAR HYDROCARBON COMPRESSOR WARRANTY
404A/134A/HYDROCARBON COMPRESSOR WARRANTY
WARRANTY CLAIMS
WHAT IS NOT COVERED BY THIS WARRANTY
ENVIRONMENTAL ATTRIBUTES
TRUE warrants to the original purchaser of every new TRUE refrigerated unit, the cabinet and all parts thereof, to be free from defects in material or workmanship, under normal
and proper use and maintenance service as specified by TRUE and upon proper installation and start-up in accordance with the instruction packet supplied with each TRUE unit. TRUE’s
obligation under this warranty is limited to a period of three (3) years from the date of original installation or 39 months after shipment date from TRUE, whichever occurs first.
Any part covered under this warranty that is determined by TRUE to have been defective within three (3) years of original installation or thirty-nine (39) months after shipment date
from manufacturer, whichever occurs first, is limited to the repair or replacement, including labor charges, of defective parts or assemblies. The labor warranty shall include standard
straight time labor charges only and reasonable travel time, as determined by TRUE.
Warranty does not cover standard wear parts which include door gaskets, incandescent bulbs or fluorescent bulbs. Warranty also does not cover issues caused by improper
installation or lack of basic preventative maintenance, which includes regular cleaning of condenser coils.
In addition to the Three (3) year warranty stated above, TRUE warrants its hermetically and semi-hermetically sealed HFC compressor to be free from defects in both material
and workmanship under normal and proper use and maintenance service for a period of two (2) additional years and for Hydrocarbon Units, an additional four (4) years from the date of
original installation but not to exceed five (5) years and three (3) months for HFC compressors and not to exceed seven (7) years and three (3) months for HC compressors after shipment
from the manufacturer.
Compressors determined by TRUE to have been defective within this extended time period will, at TRUE’s option, be either repaired or replaced with a compressor or compressor
parts of similar design and capacity.
The two (2) year extended HFC or four (4) year HC extended compressor warranty applies only to hermetically and semi-hermetically sealed parts of the compressor and does
not apply to any other parts or components, including, but not limited to: cabinet, paint finish, temperature control, refrigerant, metering device, driers, motor starting equipment, fan
assembly or any other electrical component, etcetera.
The two (2) year HFC compressor and four (4) year HC compressor warranty detailed above will be voided if the following procedure is not carefully adhered to:
1. This system contains R404A, R134A, or R290 refrigerant and polyol ester lubricant. The polyol ester lubricant has rapid moisture absorbing qualities. If long exposure to the ambient
conditions occur, the lubricant must be removed and replaced with new. For oil amounts and specifications please call TRUE technical service department (855-372-1368). Failure to
comply with recommended lubricant specification will void the compressor warranty.
2. Drier replacement is very important and must be changed when a system is opened for servicing. An OEM exact replacement should be used. The new drier must also be the same
capacity as the drier being replaced.
3. Micron level vacuums must be achieved to ensure low moisture levels in the system. 500 microns or lower must be obtained.
All claims for labor or parts must be made directly through TRUE. All claims should include: model number of the unit, the serial number of the cabinet, proof of purchase, date of
installation, and all pertinent information supporting the existence of the alleged defect.
In case of warranty compressor, a picture of the compressor model tag must be returned to TRUE along with above listed information. For warranty claim information, visit www.
truemfg.com/Support/Warranty-Support. Any action for breach of these warranty provisions must be commenced within six (6) months of the defect giving rise to the breach.
True reserves the right to request any failed part covered under warranty to be returned.
TRUE’s sole obligation under this warranty is limited to either repair or replacement of parts, subject to the additional limitations below. This warranty neither assumes nor authorizes any
person to assume obligations other than those expressly covered by this warranty.
NO CONSEQUENTIAL DAMAGES. TRUE IS NOT RESPONSIBLE FOR ECONOMIC LOSS; PROFIT LOSS; OR SPECIAL, INDIRECT, OR CONSEQUENTIAL DAMAGES, INCLUDING WITHOUT LIMITATION,
LOSSES OR DAMAGES ARISING FROM FOOD OR PRODUCT SPOILAGE CLAIMS WHETHER OR NOT ON ACCOUNT OF REFRIGERATION FAILURE.
WARRANTY IS NOT TRANSFERABLE. This warranty is not assignable and applies only in favor of the original purchaser/user to whom delivered. ANY SUCH ASSIGNMENT OR TRANSFER
SHALL VOID THE WARRANTIES HEREIN MADE AND SHALL VOID ALL WARRANTIES, EXPRESS OR IMPLIED, INCLUDING ANY WARRANTY OF MERCHANTABILITY OR FITNESS FOR A PARTICULAR PURPOSE.
IMPROPER USAGE. TRUE ASSUMES NO LIABILITY FOR PARTS OR LABOR COVERAGE FOR COMPONENT FAILURE OR OTHER DAMAGES RESULTING FROM IMPROPER USAGE OR INSTALLATION OR
FAILURE TO CLEAN AND/OR MAINTAIN PRODUCT AS SET FORTH IN THE WARRANTY PACKET PROVIDED WITH THE UNIT.
RELOCATION OF CABINET FOR REPAIR. True is not responsible for the cost to move a cabinet for any reason from its position of operation on the customer’s premises to make a warranty repair.
NON OEM PARTS. Use of non OEM parts without manufacturer’s approval will void cabinet warranty.
ALTERATION, NEGLECT, ABUSE, MISUSE, ACCIDENT, DAMAGE DURING TRANSIT OR INSTALLATION, FIRE, FLOOD, ACTS OF GOD. TRUE is not responsible for the repair or replacement of any
parts that TRUE determines have been subjected after the date of manufacture to alteration, neglect, abuse, misuse, accident, damage during transit or installation, fire, flood, or act of God.
IMPROPER ELECTRICAL CONNECTIONS. TRUE IS NOT RESPONSIBLE FOR THE REPAIR OR REPLACEMENT OF FAILED OR DAMAGED COMPONENTS RESULTING FROM INCORRECT SUPPLY VOLTAGE,
THE USE OF EXTENSION CORDS, LOW VOLTAGE, OR UNSTABLE SUPPLY VOLTAGE.
NO IMPLIED WARRANTY OF MERCHANTABILITY OR FITNESS FOR A PARTICULAR PURPOSE: THERE ARE NO OTHER WARRANTIES, EXPRESSED, IMPLIED OR STATUTORY, EXCEPT THE THREE
(3) YEAR PARTS & LABOR WARRANTY AND THE ADDITIONAL TWO (2) YEAR HFC COMPRESSOR AND THE ADDITIONAL FOUR (4) YEAR HC COMPRESSOR WARRANTY AS DESCRIBED ABOVE. THESE
WARRANTIES ARE EXCLUSIVE AND IN LIEU OF ALL OTHER WARRANTIES, INCLUDING IMPLIED WARRANTY AND MERCHANTABILITY OR FITNESS FOR A PARTICULAR PURPOSE. THERE ARE NO
WARRANTIES WHICH EXTEND BEYOND THE DESCRIPTION ON THE FACE HEREOF.
OUTSIDE U.S. AND CANADA: This warranty does not apply to, and TRUE is not responsible for, any warranty claims made on products sold or used outside the United States and Canada.
This warranty only applies to units shipped from True’s manufacturing facilities after October 1, 2019 for US Foodservice & Retail and after July 1, 2020 for Canada.
Any and all environmental attributes, including environmental offset credit rights, with respect to TRUE® refrigeration units manufactured after September 1, 2015, shall remain the property
of True Manufacturing Co., Inc. and are not transferred.
MS • 8/20
Warranty Information (USA & Canada Only)
Содержание TSCI Series
Страница 2: ...truemfg com TEC_TM_098 REV A 10 12 2020 Page 2 of 32 S C I E N T I F I C S E R I E S Notes ...
Страница 28: ...truemfg com TEC_TM_098 REV A 10 12 2020 Page 28 of 32 S C I E N T I F I C S E R I E S Notes ...
Страница 29: ...TEC_TM_098 REV A 10 12 2020 Page 29 of 32 truemfg com S C I E N T I F I C S E R I E S Notes ...
Страница 30: ...truemfg com TEC_TM_098 REV A 10 12 2020 Page 30 of 32 S C I E N T I F I C S E R I E S Notes ...
Страница 32: ...TEC_TM_098 REV A 10 12 2020 Page 32 of 32 www truemfg com EA BP_MISC_2268_10 2020 ...