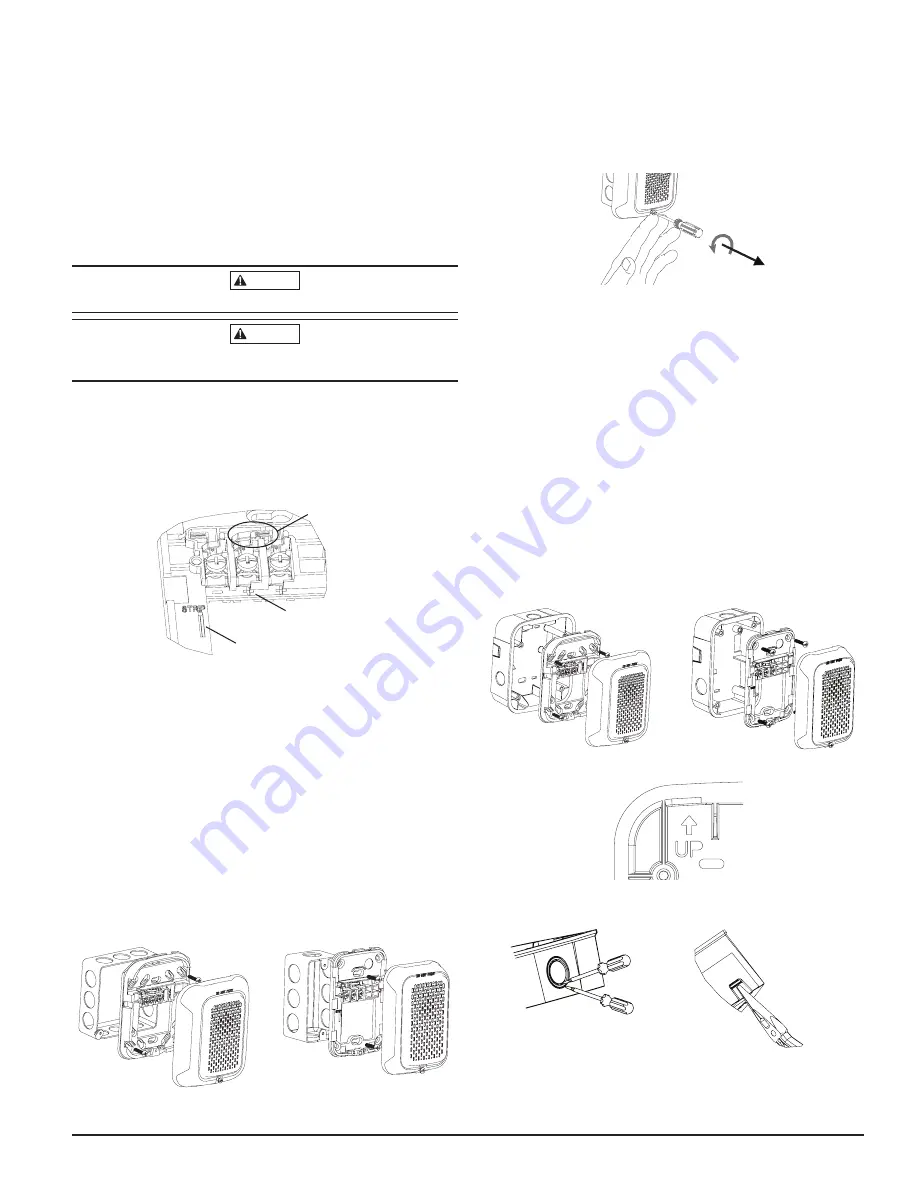
3
I56-5844TRG-002
2/1/2021
TAMPER SCREW
For tamper resistance, the standard captive screw may be replaced with a Torx
screw, ordered separately.
1. To remove the captive screw, back out the screw and apply pressure to the
back of the screw until it disengages from the housing. Replace with Torx
screw. (See Figure 5.)
FIGURE 5. TAMPER SCREW
T15 Torx
#6-32, 5/8"
SCREW-TMPR-50
A0478-01
INSTALLING A SURFACE MOUNT BACK BOX
1. The surface mount back box may be secured directly to the wall or ceiling.
Use of grounding bracket with ground screw is optional. (See Figures 6 and 7.)
2. The wall mount box must be mounted with the up arrow pointing up. (See
Figure 8.)
3. Threaded knockout holes are provided for the sides of the box for ¾ inch
and ½ inch conduit adapter. Knockout holes in the back of the box can be
used for ¾ inch and ½ inch rear entry.
4. To remove the ¾ inch knockout, place the blade of a flat-head screwdriver
along the outer edge and work your way around the knockout as you strike
the screwdriver. (See Figure 9.)
NOTE: Use caution not to strike the knockout near the top edge of the
surface mount back box.
5. V500 and V700 raceway knockouts are also provided. Use V500 for low
profile applications and V700 for high profile applications.
6. To remove the knockout, turn pliers up. (See Figure 10.)
FIGURE 6. STANDARD SURFACE-
MOUNT BACK BOX
A0479-00
FIGURE 7. COMPACT SURFACE-
MOUNT BACK BOX
A0480-00
FIGURE 8. SURFACE MOUNT BACK BOX UP ARROW
A0481-00
FIGURE 9 AND 10. KNOCKOUT AND WIRE MOLD REMOVAL FOR SUR-
FACE MOUNT BACK BOX
½ inch
or ¾ inch
Wire Mold Removal
A0465-01
A0466-01
NOTE: Use caution not to strike the knockout near the top edge of the wall
version of the surface mount back box.
WIRING AND MOUNTING
All wiring must be installed in compliance with the National Electric Code
and the local codes as well as the authority having jurisdiction. Wiring must
not be of such length or wire size which would cause the notification appli-
ance to operate outside of its published specifications. Improper connections
can prevent the system from alerting occupants in the event of an emergency.
Wire sizes up to 12 AWG (2.5 mm²) may be used with the mounting plate. The
mounting plate ships with the terminals set for 12 AWG wiring.
Make wire connections by stripping about
3
/
8
" of insulation from the end of
the wire. Then slide the bare end of the wire under the appropriate clamping
plate and tighten the clamping plate screw.
We provide a wire strip guide. See Figure 2 for wiring terminals and strip
guide reference.
CAUTION
Factory finish should not be altered: Do not paint!
CAUTION
Do not over tighten mounting plate screws; this may cause mounting plate
to flex.
SHORTING SPRING FEATURE
These notification appliances
come with a shorting spring that is provided be-
tween terminals 2 and 3 of the mounting plate to enable system continuity
checks after the system has been wired, but prior to installation of the final
product. (See Figure 2.) This spring will automatically disengage when the
product is installed, to enable supervision of the final system.
FIGURE 2. WIRING TERMINALS, SHORTING SPRING, AND STRIP GUIDE
Shorting Spring
Strip Guide
WIRING TERMINALS
1. Negative (-). Line in and out
2. Positive (+). Line in and out
3. Positive (+). Line in and out
A0475-01
MOUNTING AND REMOVING APPLIANCE
1. Attach mounting plate to junction box. (See Figures 3 and 4.)
2. Connect field wiring according to terminal designations. (See Figure 2.)
3. If the product is not to be installed at this point, use the protective dust
cover to prevent contamination of the wiring terminals on the mounting plate.
4. To attach product to mounting plate:
a. Remove the protective dust cover.
b. Hook the tabs on the top of the product housing into the grooves on
mounting plate.
c. Pivot the product into position to engage the terminals on the mounting
plate. Make sure that the tabs on the back of the product housing fully
engage with the mounting plate.
d. Hold product in place with one hand, and secure product by tightening the
single mounting screw in the front of the product housing.
FIGURE 3. STANDARD DEVICE
FIGURE 4. COMPACT DEVICE
A0476-00
A0477-00