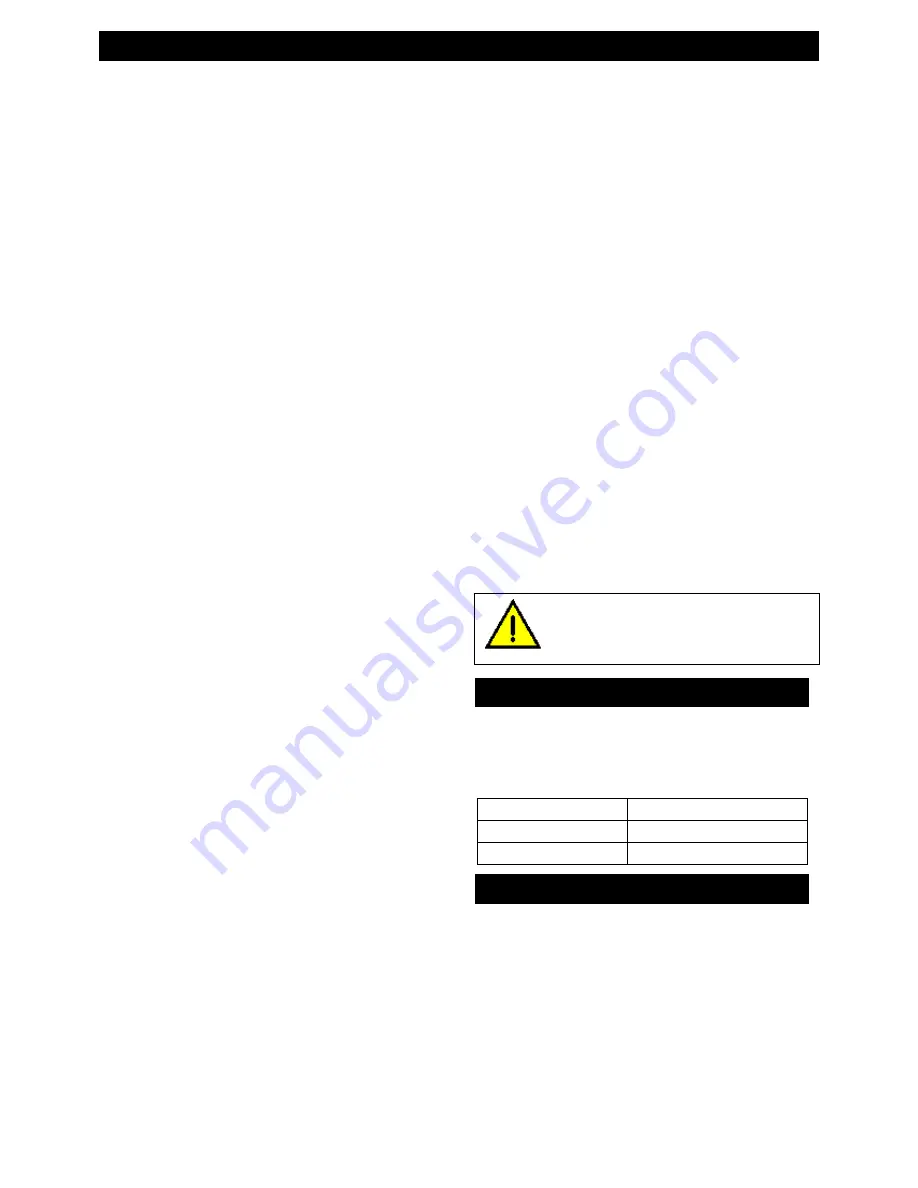
5
This booklet, along with the accompanying user
manual, should be kept by the householder and
should always stay with the boiler, even when the
appliance is transferred to another system.
Please read these instructions carefully, as they
provide important directions for the safe installation,
use and maintenance of the appliance.
Any use of the boiler not sanctioned by these
instructions is strictly prohibited and will invalidate the
guarantee.
Installation, commissioning and servicing of the boiler
must only be carried out by a CORGI-trained and
registered engineer.
Any person(s) who carries out other remedial work,
e.g. electrical fault-finding, must have suitable
engineering qualifications.
The appliance contains no asbestos or other
substances which contravene the COSHH
Regulations (Control of Substances Hazardous to
Health Regulations, 1988).
Flue systems must not be modified in any way other
than as described in the installation manual.
Do not store or use any combustible materials close
to, or within the appliance.
In the case of structural work or maintenance close to
the pipework, flue system, appliance or accessories,
switch off the boiler prior to the commencement of
such work. Only reactivate the boiler once these have
been thoroughly checked by suitably-qualified
personnel.
The appliance must be serviced annually by a
CORGI-registered engineer, unless the requirements
of the installation demand more frequent service.
Do not obstruct the clean air supply to the boiler, or
the flue terminal.
When installing the appliance, do not mount it on
chairs, ladders, stools or any other unstable surface.
To clean the appliance casing, switch off the boiler
and isolate the power supply. Wipe with a damp cloth.
Do not use detergents, harsh liquids, or other toxic
products.
Before operating the appliance, please ensure that all
gas and water supply valves are open, and that the
system has been correctly filled with water.
The system must be flushed of all deposits before
filling.
Installation is the purchaser’s responsibility.
Any repair should be carried out using original spares.
Failure to do so may invalidate the guarantee and
jeopardise the safety of the boiler. Trianco is not held
liable for the malfunction of any of these components
It is forbidden to climb on the appliance.
Always turn off the gas cock before carrying out any
work on components which carry gas.
If you smell gas:
-
do not operate any electrical appliances
-
extinguish any fires
-
close the main gas valve upstream of the meter
-
open all windows and doors to ventilate the room
-
telephone the gas company
If you smell combustion fumes from the boiler:
-
switch off the boiler
-
open all windows and doors to ventilate the room
-
call your local authorised engineer
Before carrying out any work on the
boiler, always switch off the power to
the appliance at the mains isolation
.
This appliance is in accordance with the applicable
requirements of the Gas Appliance Directive, Boiler
Efficiency Directive, Electromagnetic Compatibility
Directive, and the Low Voltage Directive.
PIN
CE 0694 BM 3593
Category UK
II
2H 3P
Appliance Type
C
13
, C
83
, B
23
, B
33
The boiler carton should include:
-
Boiler
-
Pipework connection manifold
-
Wall mounting bracket and templates
-
Instruction/guarantee pack
-
Bag of screws/fixings
-
Diverter valve connection (SB model only)
-
External controls connection (SB model only)
1
WARNINGS & SAFETY ADVICE
1.1 E.C. DECLARATION OF CONFORMITY
1.2 CONTENTS OF PACK
Содержание TRISTAR OPTIMA JUNIOR K CB
Страница 2: ...2...
Страница 4: ...4...
Страница 7: ...7 2 TECHNICAL SPECIFICATION...
Страница 9: ...9 2 2 WALL MOUNTING TEMPLATE FIG 2...
Страница 28: ...28 6 16 VERTICAL BALANCED FLUE SCHEMATIC FIG 39...
Страница 32: ...32...
Страница 42: ...42...
Страница 43: ...43...
Страница 44: ...44 Issue 1 Rev 0 July 2005 Item No 510062 LB 1480 01 09 2005...