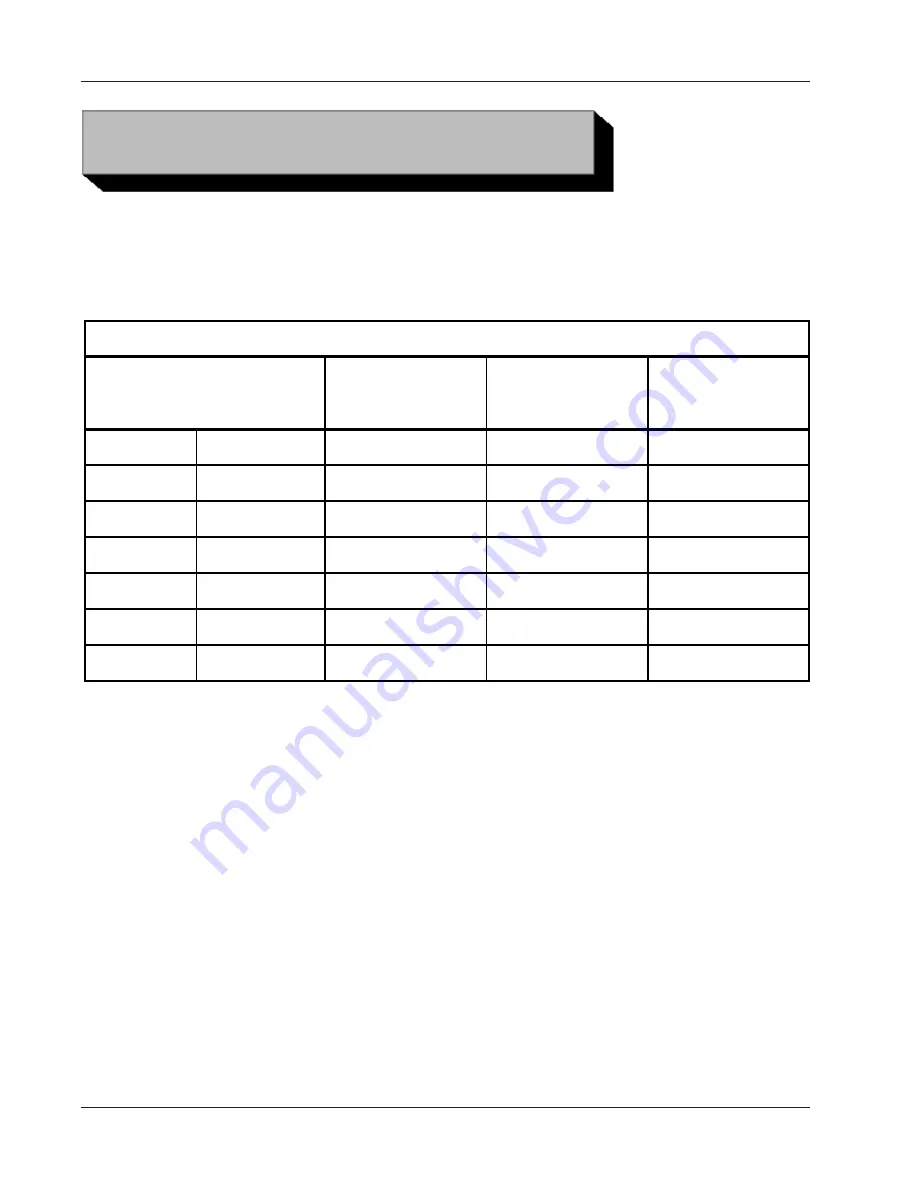
16
TRI TOOL INC.
92-0660 : Rev. 080423
CUTTING SPEEDS AND FEEDS
CUTTING SPEEDS
The chart below shows RPM required to obtain a specified Tool Bit cutting speed on
the surface of a pipe or tube.
Use 200 surface inches per minute (5080 surface millimeters per minute) for:
Stainless steels in general when no coolant is allowed, all heavy wall tube and some
of the chrome/molybdenum alloys.
Use 250 surface inches per minute (6350 surface millimeters per minute) for:
Mild steels and some thin wall stainless steels when coolants are permitted and
used.
Use 300 surface inches per minute (7620 surface millimeters per minute) for:
Aluminum and thin-wall mild steel tube with coolant.
CUTTING FEEDS
Use very light feed for initial severing or until a continuous cut is established.
Use a feed rate .002” to .003” (.05mm to .08 mm) per revolution once a continuous
cut is established.
RPM for
200 in/min
(5080 mm/min)
RPM for
250 in/min
(6350 mm/min)
RPM for
300 in/min
(7620 mm/min)
.25"
6.4 mm
255
318
382
.38"
9.5 mm
169
209
251
.50"
12.7 mm
127
159
191
.75"
19.1 mm
85
106
127
1.00"
25.4 mm
64
80
95
1.50"
38.1 mm
42
53
64
2.00"
50.8 mm
32
40
48
Tube Size
Cutting Speeds (Approximately)