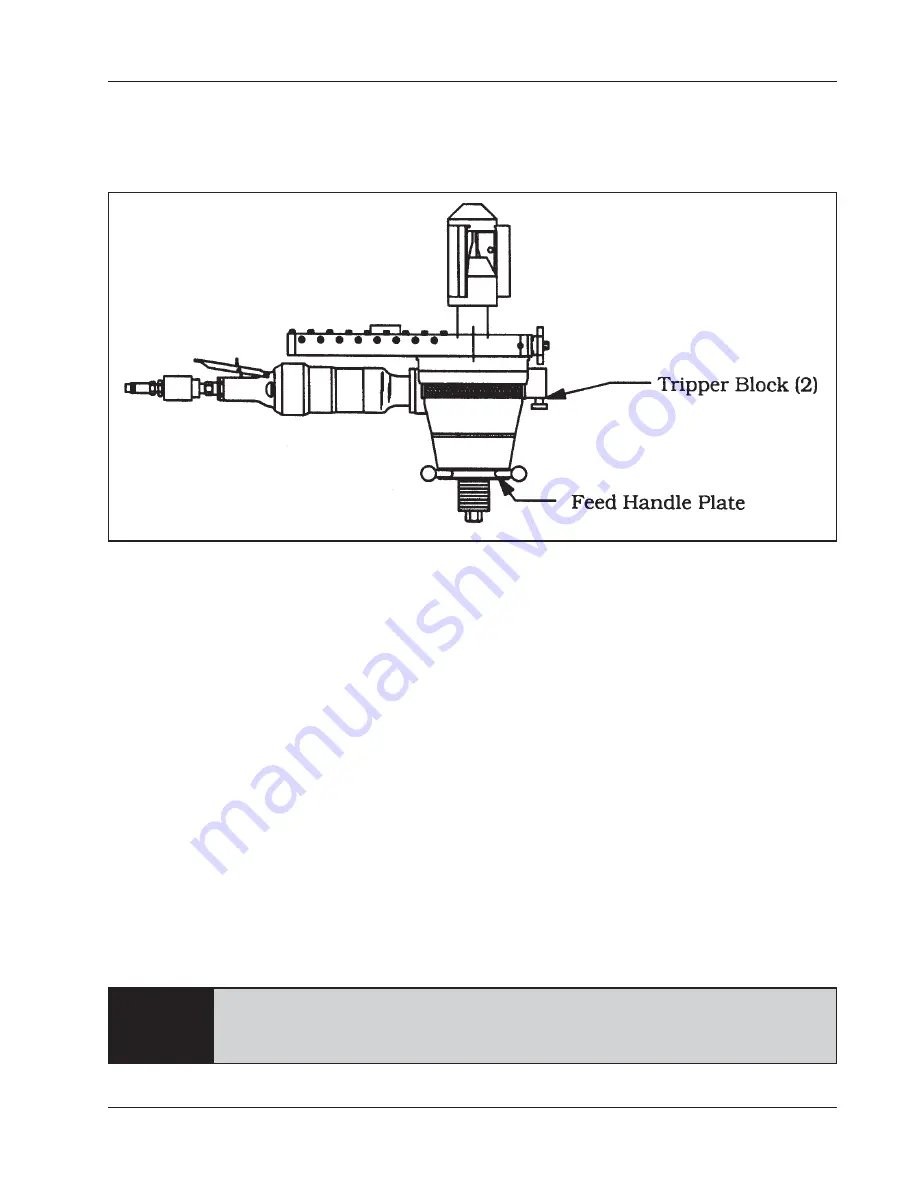
13
Model 212B-FF Flange Facer
92-0291 : Rev. 921230
WARNING:
Check that the Tool Holder runs smoothly and evenly for the full length of travel.
Re-adjust as necessary.
Location of the Tripper Blocks
To adjust the depth of cut of the Tool Bit to flange, rotate the Feed Knob on the
Model 212B until the desired position is achieved.
Depth of the cut for roughing should not exceed .030” (.76 mm).
Finish cut for optimum finishes should be .005” to .015” (.13 to .38 mm).
Lock the Mandrel in place using the Mandrel Lock Set Screw. Located in the back
of the Feed Handle Plate.
FEED RATE
The feed rate is .013” (.33 mm) per revolution per Tripper Block.
Two Tripper Blocks are supplied with the kit.
INSTALLATION OF THE TOOL BITS
To select the appropriate Tool Bits refer to the section “Tool Bits”.
Use of dull or improperly designed Tool Bits or Tool Bits not manufactured by
Tri Tool Inc. may result in poor performance and may constitute abuse of this
machine and therefore voids the Tri Tool Inc. factory warranty.