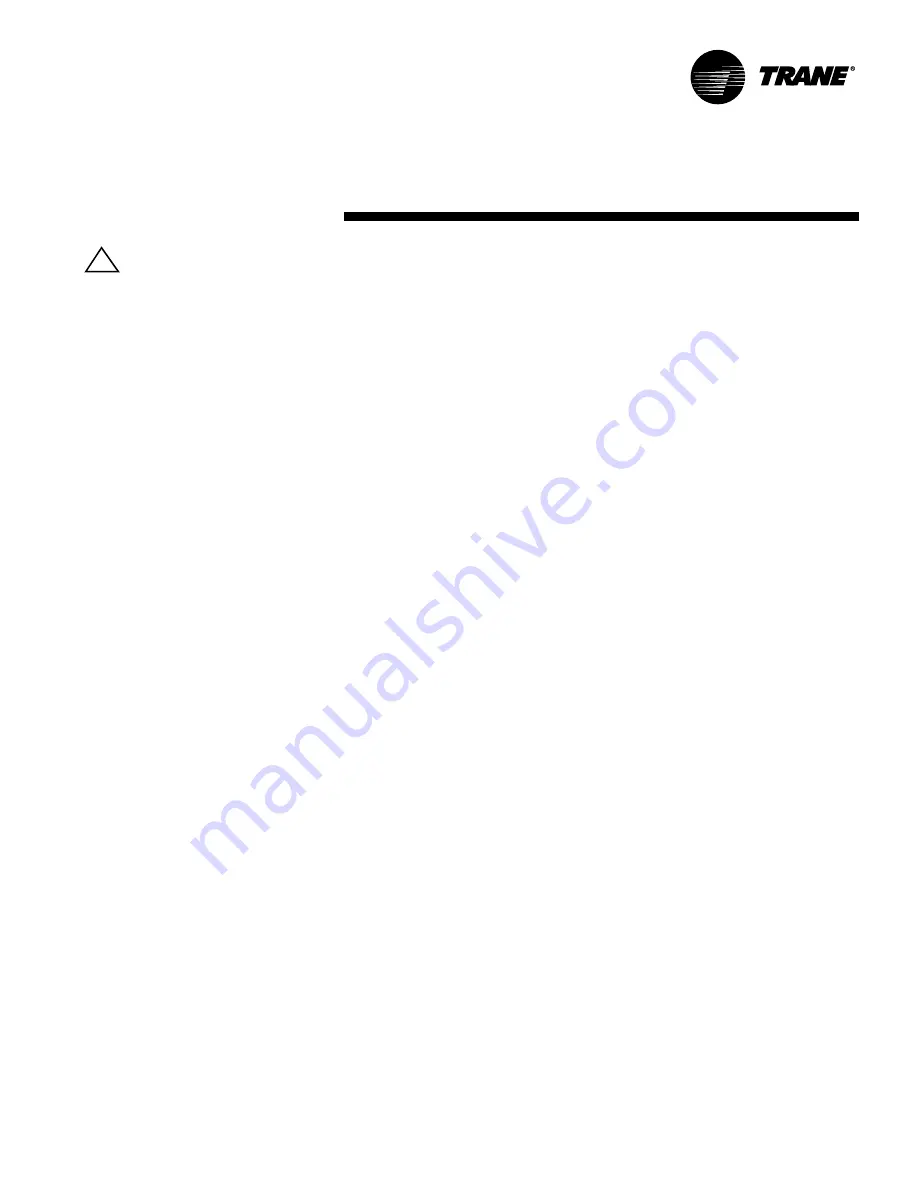
UV-SVN03D-EN
29
WARNING
Hazardous Service
Procedures!
The maintenance and trouble-
shooting procedures recommend-
ed in this section of the manual
could result in exposure to electri-
cal, mechanical or other potential
safety hazards. Always refer to
the safety warnings provided
throughout this manual concern-
ing these procedures. When possi-
ble, disconnect all electrical
power including remote discon-
nects before servicing. Follow
proper lockout/tagout procedures
to ensure the power can not be in-
advertently energized. When nec-
essary to work with live electrical
components, have a qualified li-
censed electrician or other indi-
vidual who has been trained in
handling live electrical compo-
nents perform these tasks. Failure
to follow all of the recommended
safety warnings provided, could
result in death or serious injury.
Modulating Valves
The valve should be serviced by a
trained, experienced technician. For
detailed installation and removal
steps, refer to Pages 18-20 in this man-
ual.
For general servicing or malfunction,
follow one of the appropriate steps:
1
If the valve is leaking, drain system
OR isolate valve from the system.
DO NOT remove valve body from
plumbing.
2
Ensure the cartridge needs to be
replaced. If so, follow appropriate
steps explained for cartridge as-
sembly removal.
3
If the motor or other internal parts
of the actuator is damaged, replace
the entire actuator assembly.
Note: These hydronic valves are de-
signed and tested for silent operation.
However, water noise may occur as a
result of high water velocity. Piping
noises may also occur in high temper-
ature (over 212° F) systems with insuf-
ficient water pressure.
Note: Do not use petroleum-based or
mineral oil type boiler additives. Com-
pounds with a 50% water dilution that
can be used are diethylene glycol,
etheylene glycol and propylene glycol.
Coil Cleaning
Periodically the hydronic coils should
be cleaned from dirt accumulation that
could reduce the unit performance. To
clean the equipment coil:
1
Remove the unit’s front panel.
2
Remove the unit’s front nosing.
3
Removed the coil’s solid steel
front cover.
4
Vacuum the dust/particles from
the coil face.
5
Reverse order for re-installation.
Preventive Maintenance
A comprehensive preventive mainte-
nance program should be established
for a unit ventilator system. The fol-
lowing are several key elements:
•
Inspect the filters monthly. Follow
the Filter Replacement instruc-
tions.
•
Inspect and clean the drain pan
every three months.
•
Check the coils for ‘‘dirt’’ accumu-
lation every three to six months.
Clean the coils at least once each
year
.
•
Inspect the unit ventilator insula-
tion every three months; thor-
oughly clean as needed.
Maintenance
!
Содержание VUV
Страница 8: ...8 UV SVN03D EN Dimensions Standard Depth Unit ...
Страница 9: ...UV SVN03D EN 9 Dimensions Falseback Unit ...
Страница 10: ...10 UV SVN03D EN Dimensions Dynamic Air Barrier Unit ...
Страница 11: ...UV SVN03D EN 11 Dimensions End Covers ...
Страница 12: ...12 UV SVN03D EN Dimensions Wall Boxes ...
Страница 33: ...UV SVN03D EN 33 Unit Wiring Field Installed Wiring 120V 1 PH 3 Speed ...
Страница 34: ...34 UV SVN03D EN Unit Wiring End Device Controls 120V 1 PH 3 Speed DX Hot Water ...
Страница 35: ...UV SVN03D EN 35 Unit Wiring End Device Package 480V 3 PH 3 Speed Chilled Water Electric Heat 6 Element page 1 ...
Страница 36: ...36 UV SVN03D EN Unit Wiring End Device Package 480V 3 PH 3 Speed Chilled Water Electric Heat 6 Element page 2 ...
Страница 37: ...UV SVN03D EN 37 Unit Wiring End Device Package 120V 1 PH 3 Speed 4 Pipe Hot Water Chilled Water ...
Страница 38: ...38 UV SVN03D EN Unit Wiring Tracer ZN520 120V 1 PH 3 Speed 4 Pipe Hot Water Chilled Water ...
Страница 39: ...UV SVN03D EN 39 ...