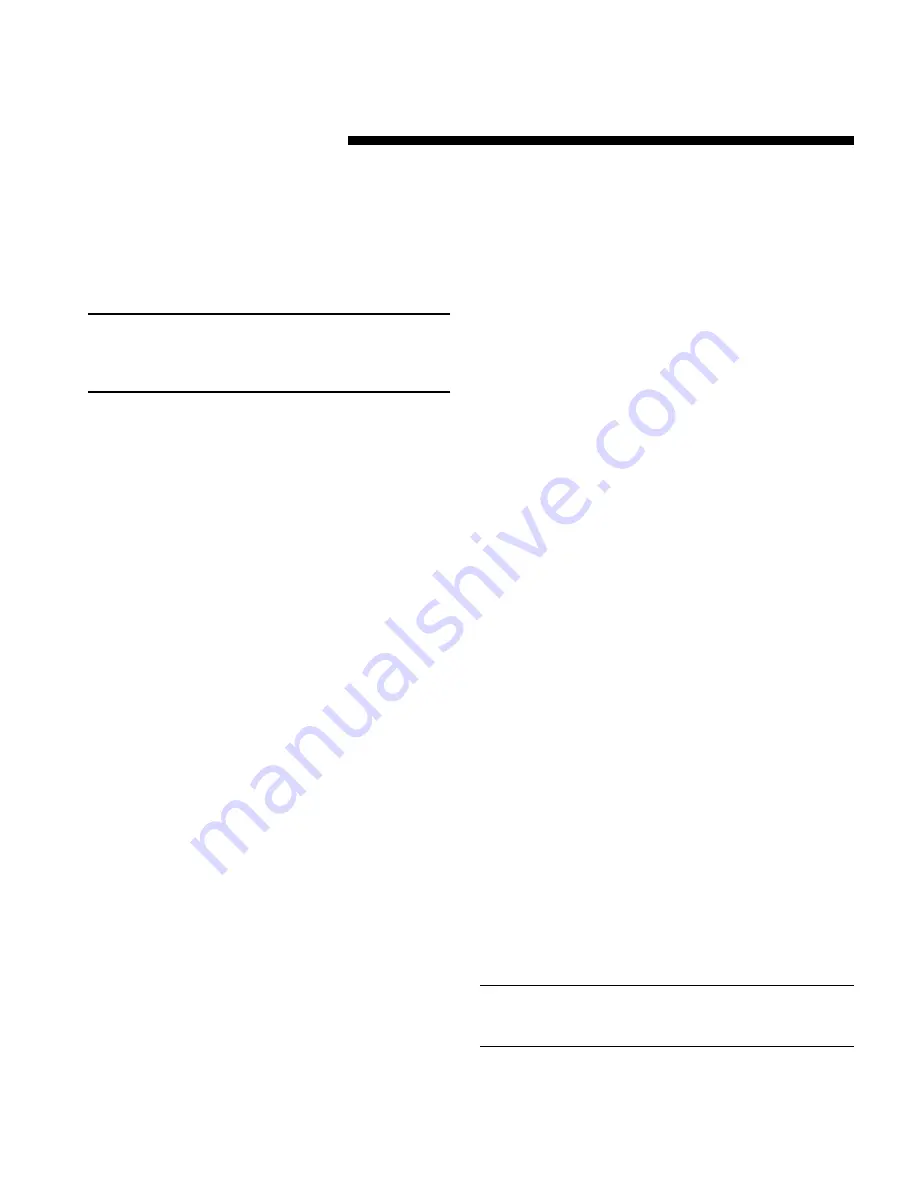
TWA-SVX01A-EN
17
Sequence of Operation
Unit Start-Up
Once the unit is properly installed and pre-start procedures
are complete, start the unit by turning the System Switch on
the indoor thermostat to either HEAT, COOL or AUTO. The
system should operate normally.
CAUTION:
Ensure the disconnect for the indoor air
handler is closed before operating the system.
Operating the indoor unit without the indoor fan
energized, can cause unit trip-out on high pressure
control and/or liquid flood back to the compressor.
General
Operation of the unit is controlled by the HEAT and/or COOL
setting in the thermostat. (An optional automatic changeover
thermostat, when in the AUTO position, automatically
changes to heat or cool cycles with sufficient room
temperature change.) The fan switch can be placed in either
the ON position, causing continuous indoor fan operation, or
the AUTO position causing fan operation to coincide with
heating or cooling run cycles. With the disconnect switch in
the closed position, current is supplied to the compressor
crankcase heater(s) and the control transformer. The
outdoor fan relay (ODF) is energized through a continuous
24 volt circuit from the transformer, and controlled through
normally closed contacts on the defrost control board (DFC).
Cooling Mode
With the system switch on the thermostat set to COOL,
current is supplied from the “R” terminal to the “O” terminal
on the low voltage terminal board of the outdoor unit. This
energizes the switch-over valve (SOV) and places it in the
cooling position. The evaporator defrost relay (EDR) is also
energized at this time, opening EDR-1 contacts to allow the
evaporator defrost control (EDC) to function while in the
cooling mode, and opening EDR-2 contacts to prevent
defrost control (DFC) operation while in cooling mode. When
the room temperature is 1 ½ degrees above the thermostat
setting, a cooling cycle is initiated by closing of the TSC-1
contacts in the thermostat. When closed, these contacts
supply power from “R” terminal through TSC-1 to “Y”
terminal on the low voltage terminal board of the outdoor
unit, which supplies power to the (CC) compressor
contactor, (compressor auxiliary relay (CCA) or auxiliary
compressor contactor (ACCA) on specific models. This
closes the compressor contacts, which starts the
compressor and outdoor fan motor. TSC-1 contacts also
supply power to the “G” terminal in the thermostat, which
energizes the fan relay (F), starting the indoor fan motor
(provided the fan switch is in the AUTO position).
On dual circuit units, when second stage cooling is
required, “Y2” terminal from the thermostat energizes
auxiliary compressor contactor (ACC) which energizes
compressor contactor B (CC-B), (ACCB on some models)
provided the HPCO and LPCO are closed. An “O” signal for
cooling is supplied to the defrost control board (DFC-B)
through the evaporator defrost relay (EDR) which was
previous energized. This signal causes an output to the
switch-over valve (SOV-B), placing it in the cooling mode.
System Start Procedure
Heating Mode
With the system switch on the thermostat set to the HEAT
position, and the room temperature drops approximately 1 ½
degrees below the thermostat setting, a heating cycle is
initiated by closing of the TSH-1 contacts. When closed, these
contacts supply power from “R” terminal through TSH-1 to “Y”
terminal on the low voltage terminal board of the outdoor unit,
which supplies power to the (CC) compressor contactor,
(compressor auxiliary relay (CCA) or auxiliary compressor
contactor (ACCA) on specific models). This closes the
compressor contacts, which start the compressor and outdoor
fan motor. TSH-1 contacts also provide power to the “G”
terminal on the thermostat, which energizes the fan relay (F),
starting the indoor fan motor (provided the fan switch is in the
AUTO position). While in the normal heating position, “O”
terminal, which powers the switch-over valve (SOV) and the
evaporator defrost relay (EDR), will remain de-energized by
the thermostat. EDR-1 contacts close, bypassing the
evaporator defrost control (EDC). EDR-2 contacts close which
supply power to the defrost control timer (DFC), allowing it to
operate during the heating cycle.
On dual circuit units, when second stage heating is required,
“Y2” from the indoor thermostat will energize auxiliary
compressor contactor (ACC), which will energize compressor
contactor B (CC-B) (ACCB on some models), provided HPCO
and LPCO are closed. Control power for the “B” compressor is
supplied from the second transformer (TNS-B) which also
powers the supplementary heaters through the heat relay (H)
when additional heat is required by “W” terminal.
Time Temperature Defrost
During the heating cycle, the outdoor coil may require a
defrost cycle which is controlled by the defrost control timer
(DFC). It is energized continuously, allowing a defrost cycle
every 50, 70 or 90 minutes when the defrost terminator (DT)
closes at the appropriate line temperature. The defrost control
timer (DFC) opens the circuit to the outdoor fan relay (ODF),
and closes a circuit through the timer board which energizes
the switch-over valve (SOV), and provides power to the “X2”
terminal for supplementary heat placing the unit into the
defrost cycle. The compressor will start 30 seconds after the
initiation of the defrost cycle. Supplementary heat is brought
on to control indoor temperature during defrost. When the
liquid line temperature reaches approximately 70 degrees, or a
10 minute timed cycled expires, the defrost control timer
(DFC) closes the to the outdoor fan relay (ODF) and opens the
circuit to the switch-over valve (SOV) and the “X2” terminal,
returning the unit to the heating mode.
On dual circuit units, defrost of each outdoor coil is
independent and will occur as required. Low pressure cutout
(LPCO) is disabled during defrost.
Note: Do not change from the 70 minute full timing
cycle in the Southern U.S. (“sunbelt”) areas. In
Northern climates, the 50 minute defrost cycle may be
needed, especially in areas of frequent snow
.