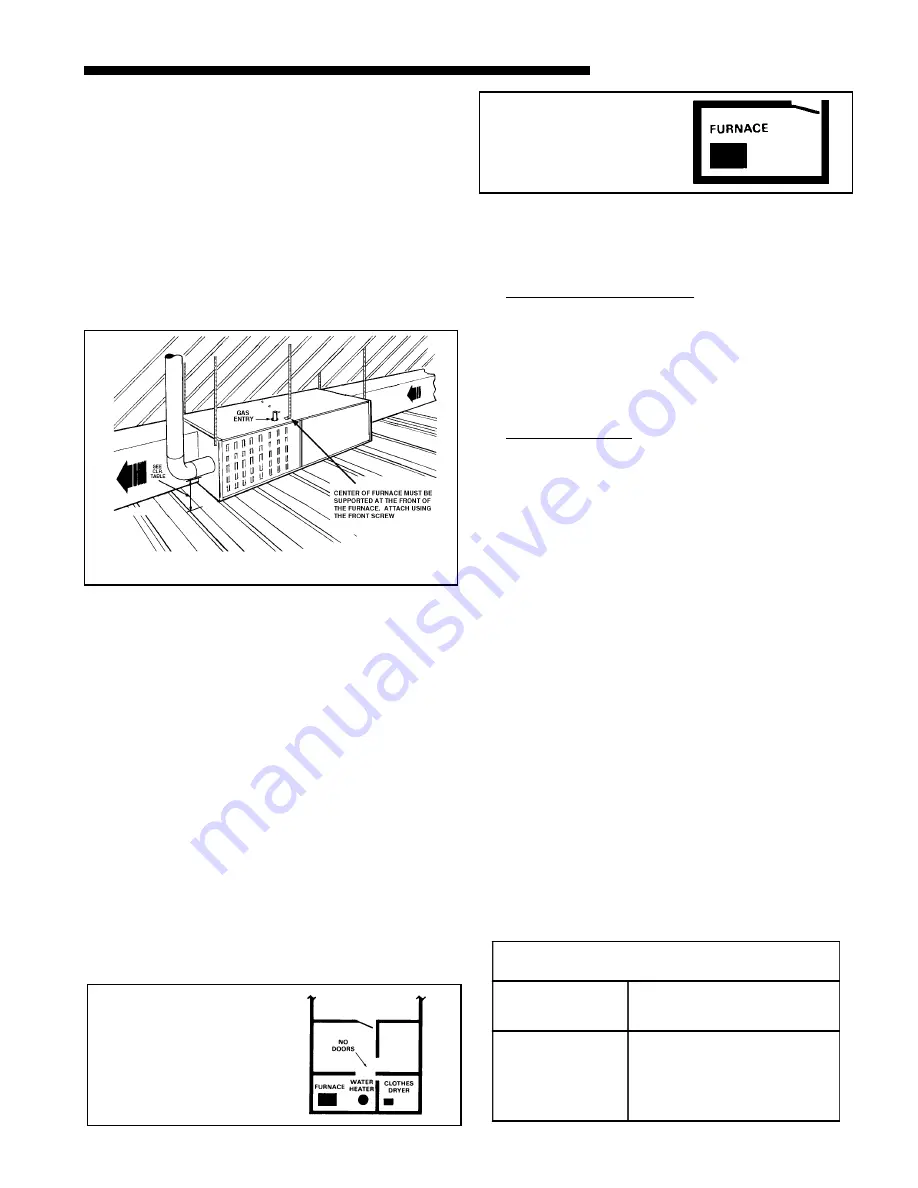
18-CD19D7-22
7
Installer’s Guide
Line contact is only permissible between lines formed by
the intersection of the top and two sides of the furnace
casing and the building joists, studs, or framing.
A cutout is provided on both sides of the downflow furnace
cabinet to allow a 90° elbow to be attached inside the cabinet
and the vent piping to connect there. In horizontal, the
downflow furnace may be vented through the top of the
cabinet if needed. In vertical configuration, the downflow
furnace may be vented using the side cabinet cutouts. This
venting configuration could be used if an electronic air
cleaner is installed.
When the downflow furnace is vented through the left
side of the furnace cabinet in horizontal or vertical
configuration, Type B vent pipe must be used within the
cabinet.
AIR FOR COMBUSTION AND VENTILATION
Adequate flow of combustion and ventilating air must not be
obstructed from reaching the furnace. Air openings provided
in the furnace casing must be kept free of obstructions which
restrict the flow of air. Airflow restrictions affect the effi-
ciency and safe operation of the furnace. Keep this in mind
should you choose to remodel or change the area which
contains your furnace. Furnaces must have a free flow of air
for proper performance.
Provisions for combustion and ventilation air shall be made
in accordance with “latest edition” of Section 5.3, Air for
Combustion and Ventilation, of the National Fuel Gas Code,
ANSI Z223.1, or Sections 7.2, 7.3 or 7.4 of CAN/CGA B149
Installation Codes, and applicable provisions of the local
building codes. Special conditions created by mechanical
exhausting of air and fireplaces must be considered to avoid
unsatisfactory furnace operation.
Furnace locations may be in “confined space” or “unconfined
space”. Unconfined space is defined in Table 2 and Figure 7.
These spaces may have adequate air by infiltration to
provide air for combustion, ventilation, and dilution of flue
gases. Buildings with tight construction (for example,
weather stripping, heavily insulated, caulked, vapor barrier,
etc.), may need additional air provided as described for
confined space.
6
TYPICAL SUSPENDED INSTALLATION
(UPFLOW/HORIZONTAL FURNACE SHOWN)
Confined spaces are installations with less than 50 cu. ft. of
space per 1000 BTU/hr input from all equipment installed.
Air for combustion and ventilation requirements can be
supplied from inside the building as in Figure 9 (page 8), or
from the outdoors, as in Figure 10 (page 8).
1. All air from inside the building as in Figure 9 (page 8):
The confined space shall be provided with two perma-
nent openings communicating directly with an addi-
tional room(s) of sufficient volume so that the combined
volume of all spaces meets the criteria for an unconfined
space. The total input of all gas utilization equipment
installed in the combined space shall be considered in
making this determination. Refer to Table 3 (page 8), for
minimum open areas required.
2. All air from outdoors as in Figure 10 (page 8): The
confined space shall be provided with two permanent
openings, one commencing within 12 inches of the top
and one commencing within 12 inches of the bottom of
the enclosure. The openings shall communicate directly,
or by ducts, with the outdoors or spaces (crawl or attic)
that freely communicate with the outdoors. Refer to
Table 3 (page 8), for minimum open areas required.
3. The following types of installations will
require
use of
OUTDOOR AIR for combustion, due to chemical
exposures:
* Commercial buildings
* Buildings with indoor pools
* Furnaces installed in commercial laundry rooms
* Furnaces installed in hobby or craft rooms
* Furnaces installed near chemical storage areas
Exposure to the following substances in the combustion
air supply will also require OUTDOOR AIR for
combustion:
* Permanent wave solutions
* Chlorinated waxes and cleaners
* Chlorine based swimming pool chemicals
* Water softening chemicals
* Deicing salts or chemicals
* Carbon Tetrachloride
* Halogen type refrigerants
* Cleaning solvents (such as perchloroethylene)
* Printing inks, paint removers, varnish, etc.
* Hydrochloric acid
* Cements and glues
* Antistatic fabric softeners for clothes dryers
* Masonry acid washing materials
TABLE 2
MINIMUM AREA IN SQUARE FEET FOR
UNCONFINED SPACE INSTALLATIONS
FURNACE MAXIMUM
BTUH / INPUT RATING
WITH 8 FOOT CEILING
MINIMUM AREA IN SQUARE FEET
OF UNCONFINED SPACE
40,000
60,000
80,000
100,000
120,000
140,000
250
375
500
625
750
875
50 CU. FT. OR MORE
PER 1000 BTU/HR. INPUT
ALL EQUIP. INSTALLED
UNCONFINED
7
CONFINED
LESS THAN 50 CU. FT.
PER 1000 BTU/HR. INPUT
ALL EQUIP INSTALLED
8
Содержание DD1A040A9241A Series
Страница 22: ...22 18 CD19D7 22 Installer s Guide NOTES...
Страница 23: ...18 CD19D7 22 23 Installer s Guide NOTES...