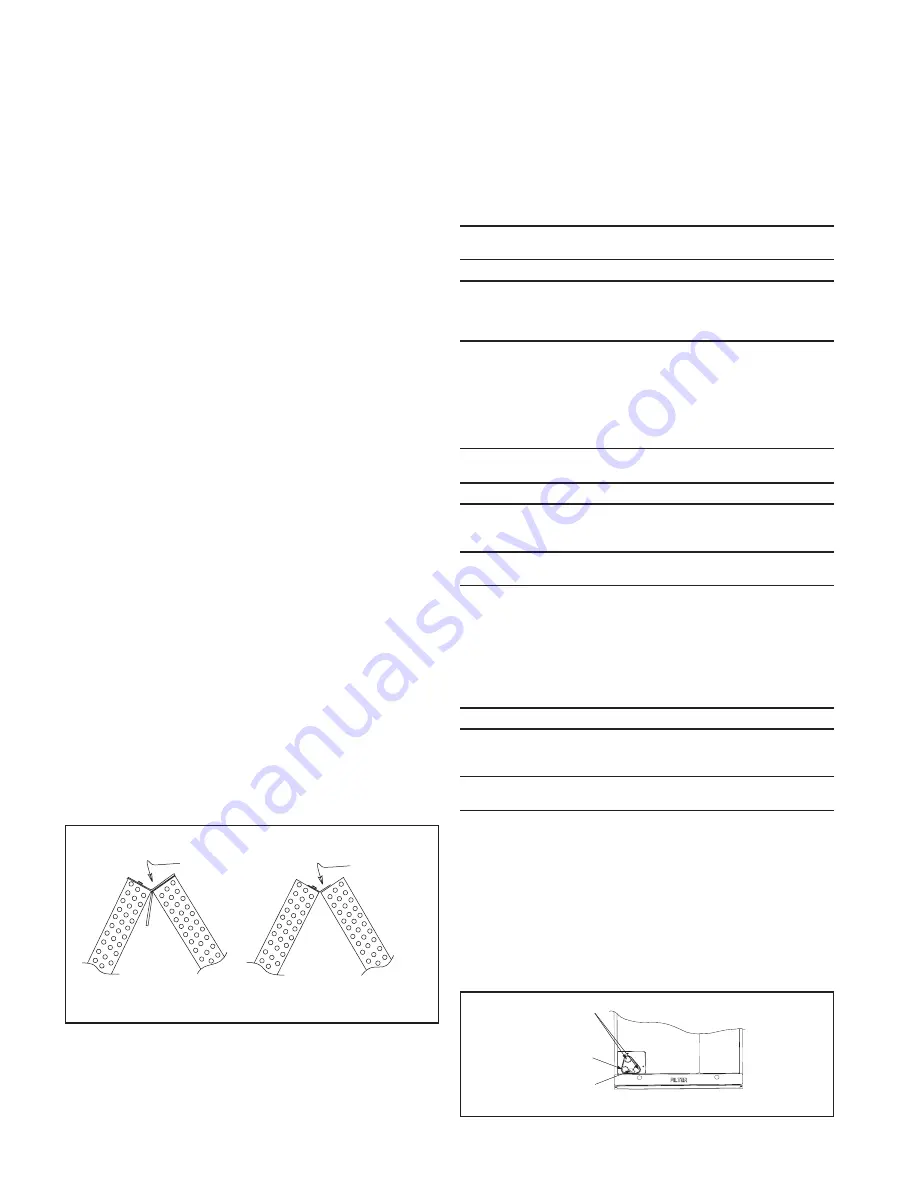
2
18-GJ02D1-2
Installer’s Guide
f. It is always recommended that an auxiliary drain pan be installed under a hori-
zontal air handler (See Condensate Drain Piping) to prevent possible damage to
ceilings.
g. Isolate the auxiliary drain pan from the unit or from the structure.
h. Connect the auxiliary drain line to a separate drain line (no trap is needed in this
line) and terminate according to local codes.
i. If a return duct is connected to the Air Handler, it must be the same dimensions
as the return opening shown in the outline drawings.
Remove
and
Discard
Replace
with
Narrow
Baffle
Figure 1. For Maximum Efficiency on Upflow
2/4TGB3F042A & 2/4TGB3F048A Only
handler must be made to allow access for refrigerant lines, or attach refrigerant
lines to air handler when installing.
11. Make sure there are provisions for installing condensate drain lines.
12. Route refrigerant & condensate drain lines away from air handler so they do not
interfere with access panels and filters.
13. When external accessories are used, the additional height and width require-
ments must be considered in the overall space needed.
14. These units are not approved for outdoor installation.
15. These units are approved for draw-through application only.
B. UNIT INSTALLATION
UPFLOW
a. For maximum efficiency, the horizontal drip tray should be removed. Tray
removal requires that the coil be removed by sliding the coil out on the coil
channel supports. The tray is detached by removing the two screws at the drain
pan and the two screws holding the two brackets at the top of the coil.
b. Openings where field wiring enters the cabinet must be completely sealed. The
Refrigerant lines must be sealed and Electrical inlets need to be sealed both
the low and the high voltage. Location of power entry is shown on the Outline
Drawing.
c.
2/4TGB3F042A & 2/4TGB3F 48A Only:
Remove the factory installed baffle
assembly from the apex of the coil by removing the 5/16" hex head screws.
Replace this baffle with the factory supplied narrow coil baffle using the screws
removed previously (See Figure 1).
d. Position unit on Pedestal or other suitable foundation. If Pedestal is not used,
a frame strong enough to support the total weight must be provided. Provide a
minimum height of 14 inches for proper unrestricted airflow.
e. If a return air duct is connected to the air handler, it must be the same dimen-
sions as shown in the outline drawing.
f. Pedestal and unit should be isolated from the foundation using a suitable isolat-
ing material.
HORIZONTAL LEFT
a. For maximum efficiency and Customer ease of filter maintenance, it is recom-
mended that a properly sized remote filter and grille be installed for horizontal
applications. Airflow should not exceed the face velocity of the filter being used.
The factory installed filter should then be removed from the unit.
b. The unit is shipped from the factory in the horizontal left airflow position.
c. Openings where field wiring enters the cabinet must be completely sealed . The
Refrigerant lines must be sealed and Electrical inlets need to be sealed both
the low and the high voltage.Location of power entry is shown on the Outline
Drawing.
d. The unit may be suspended as long as the unit is supported from both ends as
well as the middle to prevent sagging and service access is not obstructed.
e. If the unit is not suspended it must be isolated carefully to prevent sound trans-
mission. Vibration isolators (purchased locally) must be placed under the unit.
C. DUCT CONNECTIONS
The supply and return air ducts should be connected to the unit with flame retardant
duct connectors.
Convertible duct flanges can be field fabricated to make a “flush fit” for ¾” or 1-1/2”
ductboard applications. See the Outline drawing for sizes of the discharge opening
and flange dimensions. After ductwork is secured, seal the ductwork per local and
national codes to prevent air loss/infiltration.
D. Refrigerant Piping
IMPORTANT: Refrigerant piping must be routed to maintain service access to
blower compartment and provide easy removal of filter access panel and filter.
1. Refrigerant connections are made outside the cabinet.
NOTE: TXV bulb MUST be protected (wrap a wet rag around the suction line
between the TXV bulb and the braze joint) or removed, while brazing the tubing.
Overheating of the sensing bulb will affect the functional characteristics and
performance of the air handler.
2. If changing the Thermostatic valve (TEV/TXV), be sure to use a wrench and
backup wrench to tighten the mechanical fittings 1/6 turn past finger tight upon
installation.
3. Installation of refrigerant lines is covered in the installation instructions pack-
aged with the outdoor unit. Evacuation, leak testing and brazing procedures are
included in those instructions. Read those instructions before starting installa-
tion of refrigerant lines.
NOTE: TXV Equipped is Non-Bleed, and may require a start kit on the outdoor
unit.
NOTE: Refrigerant line openings must be sealed along with field wiring.
E. BRAZING TO EVAPORATOR SECTION
IMPORTANT: Do not unseal refrigerant tubing until ready to cut and fit refriger-
ant lines.
1. Remove the sealing caps from indoor coil field connections.
2. Field supplied tubing should be cut squared-off, ensuring the tube is still round
and free of burrs at the connecting end. Clean the tubing to prevent contami-
nants from entering the system.
3. Run refrigerant tubing into the stub sockets of indoor unit coil. Refrigerant line
openings must be completely sealed.
4. Braze and evacuate according to indoor and outdoor installation instructions.
NOTE: Painted areas of unit must be shielded during brazing.
F. CONDENSATE DRAIN PIPING
NOTE: Make certain that the unit has been installed in a level position to ensure
proper draining.
The indoor blower is downstream of the evaporator coil which creates a negative
pressure at the condensate drain connections during operation. The condensate
drain connections in front of the indoor coil are 3/4" NPT. The lower connection is the
primary drain. See Figure 2.
Two secondary drain connections are provided for the different orientations (See Fig-
ure 2). The lower of the two should be connected as a backup to prevent condensate
overflow by a blocked primary drain. The weep hole in center of drain coupling area
should be sealed with caulk or RTV.
For proper drainage of condensate, the following steps should be followed:
1. The primary drain line must be trapped with a minimum of 2" water seal as
shown in Figure 3.
Figure 2. Condensate Drain Locations
3/4" NPT
Primary drain
connection
3/4" NPT Secondary
drain connection
Seal weep hole