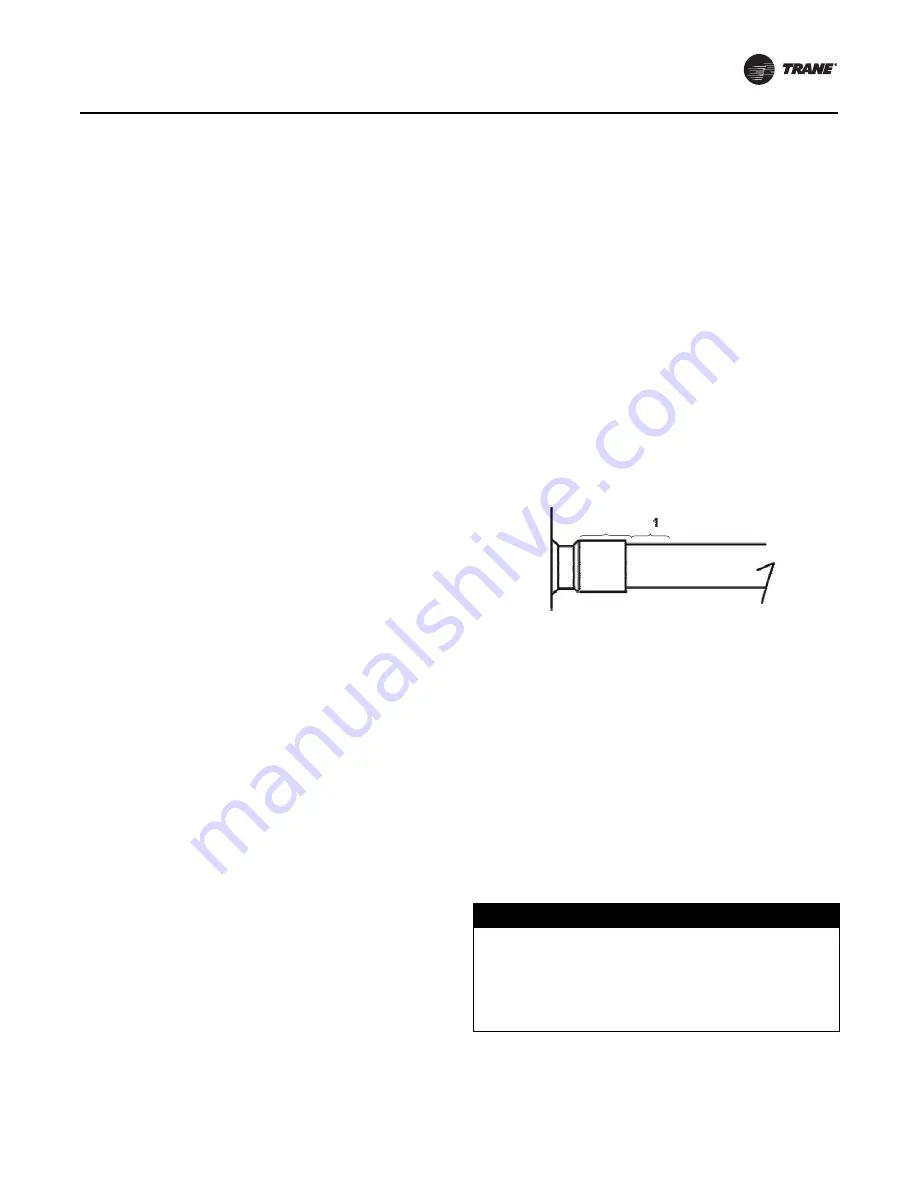
Removal and Installation
COM-SVN003B-EN
13
•
Remove equalizer rubber plug and drain oil from
replacement compressor.
•
Install replacement compressor in unit using slip
couplings on suction and/or discharge tubing, as
necessary.
•
Equalizer tubes that remain full diameter (1.125")
between compressors can also be reassembled
with slip couplings.
•
Equalizer tubes which reduce to 0.25" tubes should
not be modified. If the 1.125" adapter tube is
damaged during removal from the failed
compressor, replace with new tube and cap.
•
Recharge oil to compressors as necessary to
equally replace the oil amount that was removed.
a. Removal Instructions
Tip:
Before removing the existing tubing from the
compressor, apply flux to the joint. This will aid in
the flow of the braze material and help keep the
joint clean for rebrazing. After fluxing, heat the joint
evenly to slightly higher temperature than the
melting temperature of the filler material. At this
point, the two parts of the assembly should be
easily separated.
b. Installation
c. Preparation:
i. For proper capillary action to occur, the tube and
the fitting must be free of oil, grease, burrs, and
oxide contamination. To remove the oil and
grease a commercial solvent or denatured
alcohol can be used. The surface may be
properly cleaned by brushing with a stainless
shell brush or by a stiff rubbing with emery cloth.
Wipe the joint clean to remove small foreign
particles such as emery dust, by wiping the
surface with a clean cloth. Once the surfaces are
clean, be careful not to touch them as oil from
the skin will contaminate the surfaces.
ii. Pre-fit the existing tubing into the compressor to
check that it has full insertion into the
compressor fitting.
iii. Apply flux with a brush to the outside of the
compressor connecting tubing, taking care to
evenly apply the flux around the entire diameter.
Care must also be taken not to get the flux inside
of the tubing as this may result in contamination
of the refrigerant system.
iv. Reinsert the tube into the compressor
connection. If the tubing does not stay fully
inserted, it must be restrained to prevent it from
backing out of the compressor connection
during the brazing process.
d. Brazing Technique
i. If possible, use a double-side torch while
brazing.
ii. Use 40% silver brazing alloy with flux.
iii. Start heating the tube first. Evenly heat the tube,
location 1 (see the figure below), until it reaches
a dull red color. When using flux, this color is
also a good indicator of when the proper brazing
temperature has been reached. Continue
heating the tube until the flux passes the
“bubbling” temperature range and becomes
quiet, completely fluid, and transparent—it
should have the appearance of clear water.
iv. Direct the flame from the tube to the fitting,
evenly heating it until the flux that may be
remaining in the fitting is also completely fluid.
v. Sweep the torch between the fitting and the
tube, locations 1 and 2 (see the figure below),
with most of the heat being applied to the
heavier and slower-heating fitting until the tube
and fitting reach and maintain a uniform heat in
both parts.
vi. Pull the flame slightly back and feed the brazing
material in between the fitting and the tube. If the
joint has been properly heated, the braze
material should flow around and into the joint.
Important:
The heated base metal should melt the
filler; the heat from the torch flame should
not be what melts the filler.
vii.Once the braze material has flowed around and
into the joint, briefly move the torch around the
fitting to ensure complete capillary action into
the joint.
viii.Check the joint to visually ensure that the braze
material is completely around the joint.
e. Post-Braze
•
When brazing refrigerant connections, protect
compressor body and terminal box from torch heat
damage.
Figure 3. Brazing locations 1 and 2
NOTICE
Equipment Damage!
Flux is corrosive and could lead to long-term problems
and equipment damage if not properly removed. If not
cleaned off, flux could hide leaks. Quench the joint with
water or a wet rag while the joint is still hot—but below
900°F—to shock off the flux.
2