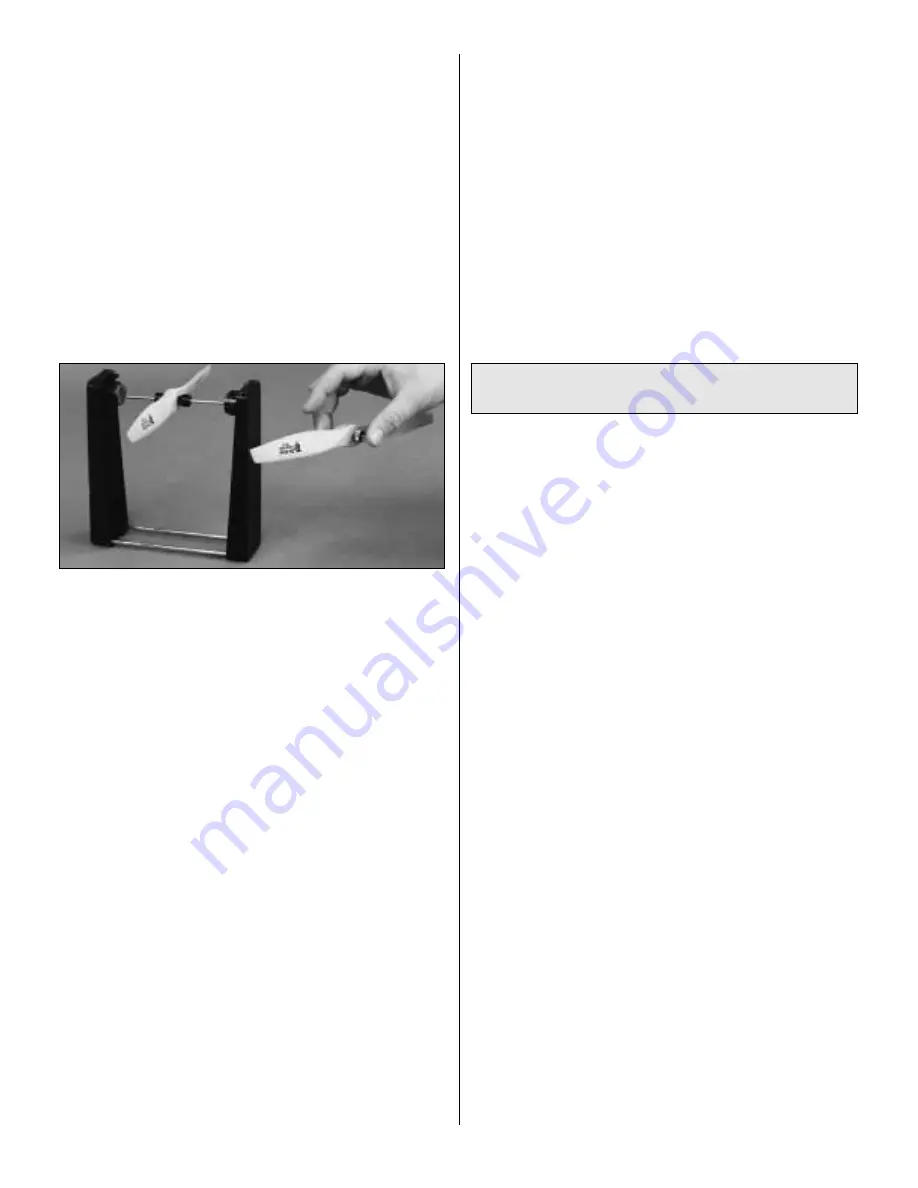
charge your transmitter and receiver batteries the night before
you go flying, and at other times as recommended by the radio
manufacturer.
Note: Checking the condition of your receiver battery pack is
highly recommended. All battery packs, whether it’s a trusty
pack you’ve just taken out of another model, or a new battery
pack you just purchased, should be cycled, noting the
discharge capacity. Oftentimes, a weak battery pack can be
identified (and a valuable model saved!) by comparing its actual
capacity to its rated capacity. Refer to the instructions and
recommendations that come with your cycler. If you don’t own
a battery cycler, perhaps you can have a friend cycle your pack
and note the capacity for you.
Balance the Propellers
Carefully balance your propeller and spare propellers before
you fly. An unbalanced prop can be the single most significant
cause of vibration that can damage your model. Not only will
engine mounting screws and bolts loosen, possibly with
disastrous effect, but vibration may also damage your radio
receiver and battery. Vibration can also cause your fuel to foam,
which will, in turn, cause your engine to run hot or quit.
We use a Top Flite Precision Magnetic Prop Balancer
™
(TOPQ5700) in the workshop and keep a Great Planes
Fingertip Prop Balancer (GPMQ5000) in our flight box.
Ground Check
If the engine is new, follow the engine manufacturer’s
instructions to break-in the engine. After break-in, confirm
that the engine idles reliably, transitions smoothly and rapidly to
full power and maintains full power–indefinitely. After you run
the engine on the model, inspect the model closely to make
sure all screws remained tight, the hinges are secure, the prop
is secure and all pushrods and connectors are secure.
Range Check
Refer to your radio system’s manual and ground check the
operational range of your radio before the first flight of the day.
With the transmitter antenna collapsed and the receiver and
transmitter on, you should be able to walk at least 100 feet away
from the model and still have control. Have an assistant stand
by your model and, while you work the controls, tell you what
the control surfaces are doing. Repeat this test with the engine
running at various speeds with an assistant holding the model,
using hand signals to show you what is happening. If the control
surfaces do not respond correctly, do not fly! Find and correct
the problem first. Look for loose servo connections or broken
wires, corroded wires on old servo connectors, poor solder
joints in your battery pack or a defective cell, or a damaged
receiver crystal from a previous crash.
ENGINE SAFETY PRECAUTIONS
Keep all engine fuel in a safe place, away from high heat,
sparks or flames, as fuel is very flammable. Do not smoke near
the engine or fuel; and remember that engine exhaust gives off
a great deal of deadly carbon monoxide. Therefore, do not run
the engine in a closed room or garage.
Get help from an experienced pilot when learning to operate
engines.
Use safety glasses when starting or running engines.
Do not run the engine in an area of loose gravel or sand; the
propeller may throw such material in your face or eyes.
Keep your face and body as well as all spectators away from
the plane of rotation of the propeller as you start and run
the engine.
Keep these items away from the prop: loose clothing, shirt
sleeves, ties, scarves, long hair or loose objects such as pencils
or screwdrivers that may fall out of shirt or jacket pockets into
the prop.
Use a “chicken stick” or electric starter to start the engine. Do
not use your fingers to flip the propeller. Make certain the glow
plug clip or connector is secure so that it will not pop off or
otherwise get into the running propeller.
Make all engine adjustments from behind the rotating propeller.
The engine gets hot! Do not touch it during or right after
operation. Make sure fuel lines are in good condition so fuel will
not leak onto a hot engine, causing a fire.
To stop a glow engine, cut off the fuel supply by closing off the
fuel line or following the engine manufacturer’s recommendations.
Do not use hands, fingers or any other body part to try to stop
the engine. Do not throw anything into the propeller of a
running engine.
Failure to follow these safety precautions may result
in severe injury to yourself and others.
26